摆线针轮减速机检测的重要性
摆线针轮减速机是一种高精度、高承载能力的传动装置,广泛应用于工业机器人、自动化生产线、医疗设备及精密机械领域。其核心工作原理基于摆线轮与针齿套的啮合传动,具有结构紧凑、传动效率高、噪音低等特点。然而,长期运行中可能因磨损、装配误差或润滑不良导致性能下降甚至故障。因此,定期进行摆线针轮减速机的系统化检测是保障设备稳定运行、延长使用寿命的关键环节。通过科学的检测手段,可及时发现潜在问题,避免因突发故障造成的停机损失。
核心检测项目及方法
1. 外观与结构完整性检测
通过目视检查减速机外壳是否存在裂纹、变形或渗油现象,确认紧固件(如螺栓、销轴)的锁紧状态。同时检查密封件(如O型圈、油封)是否老化或破损,防止因密封失效导致润滑剂泄漏或污染物侵入。
2. 齿部啮合间隙测量
使用千分表或激光测距仪检测摆线轮与针齿套的啮合间隙,确保其符合设计标准(通常为0.03-0.08mm)。间隙过大可能引发传动冲击,而过小则会导致摩擦加剧,需结合动态测试数据综合判断。
3. 振动与噪声分析
通过振动传感器和声级计采集运行时的振动频谱与噪声值,对比历史数据或行业标准。异常高频振动可能指向轴承损坏,而低频振动常与齿轮偏心或装配不良相关。
4. 温升与润滑状态检测
在额定负载下连续运行2小时后,用红外测温仪监测轴承位、齿轮啮合区等关键点的温度变化。同时抽取润滑油样进行黏度、污染度及金属颗粒检测,评估润滑系统的有效性。
5. 传动效率与回差测试
采用扭矩传感器和编码器测量输入输出端的扭矩与转速比,计算实际传动效率(理想值≥90%)。回差检测可通过反向旋转法进行,数值超过0.1°时需调整预紧力或更换磨损部件。
6. 动态载荷试验
在模拟工况下施加周期性变载荷,检测减速机的动态响应特性,包括瞬时过载能力、抗冲击性能及疲劳强度。此测试可验证减速机在极端条件下的可靠性。
检测结果的应用与维护建议
根据检测数据生成设备健康评估报告,对超标项制定针对性维修方案。例如:齿面磨损超过30%需更换摆线轮;润滑脂含水量>0.5%时应彻底清洗油箱并更换油品。建议每2000小时或半年实施一次全面检测,并建立数字化档案实现状态预测性维护。
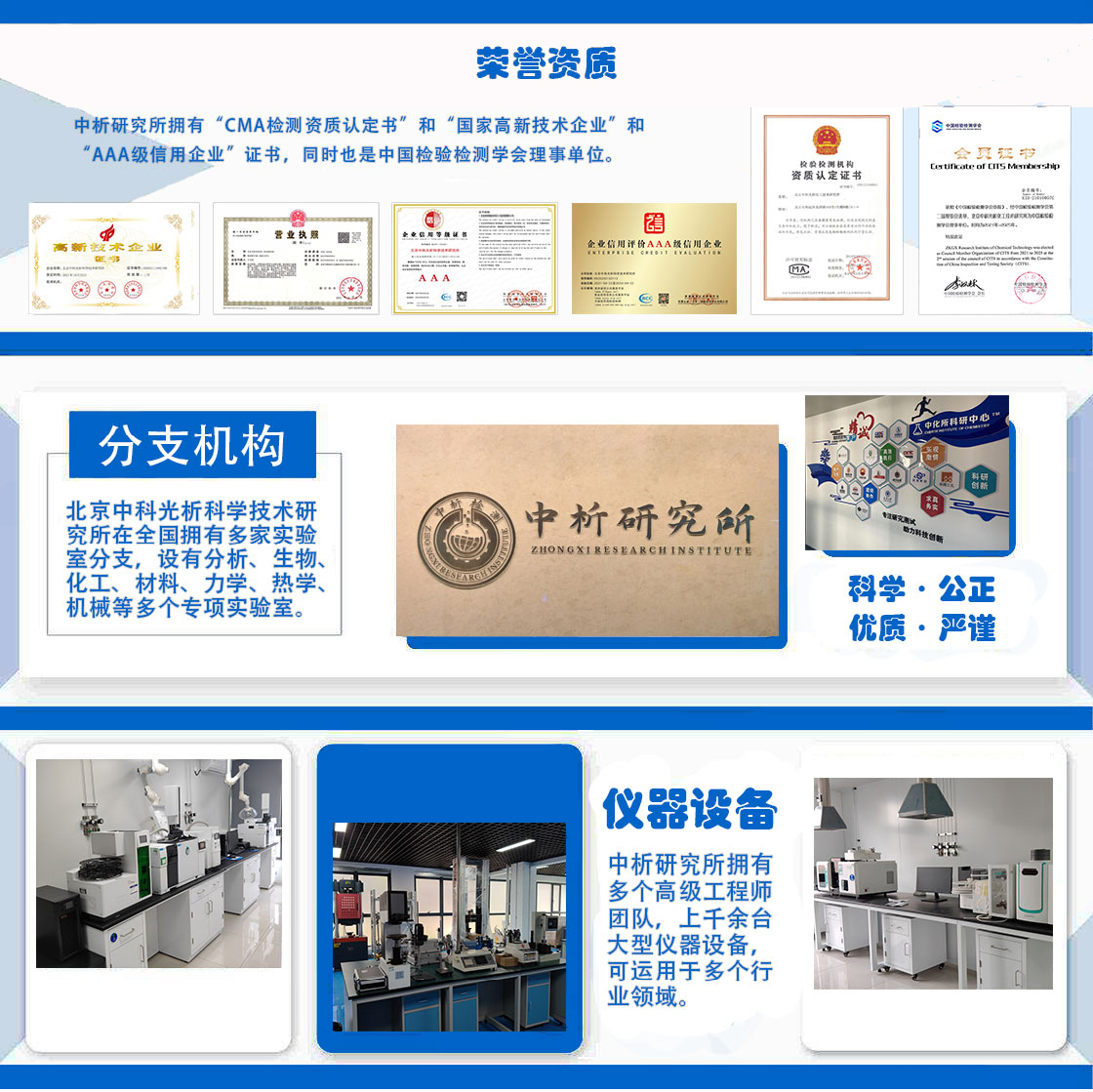
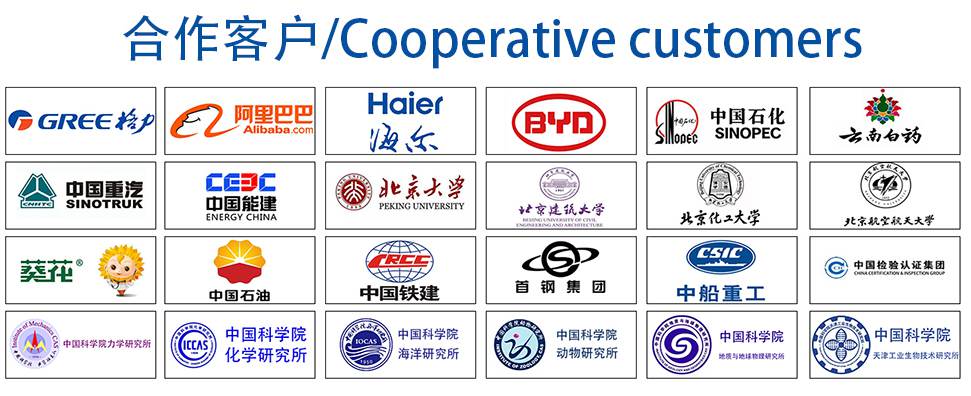