粘条率检测:定义与行业意义
粘条率检测是工业生产中针对粘性材料附着性能的核心质量控制环节,尤其在包装、纺织、印刷及电子元器件制造领域具有关键作用。该检测通过量化分析粘合材料(如胶带、标签、薄膜等)与基材之间的结合强度及稳定性,评估产品在实际应用中的可靠性。粘条率的优劣直接决定了产品能否满足运输、存储、使用过程中的环境耐受性要求,例如高温高湿下的抗脱落能力、反复开合后的粘性保持度等。据统计,制造业中因粘条率不合格导致的退货率高达3%-8%,而通过系统性检测可将这一比例降低至0.5%以下。
核心检测项目与技术规范
1. 初始粘接力测试
采用斜面滚球法(ASTM D3121)或环形初粘法(GB/T 4852),测量粘性材料在标准温湿度条件下(23℃±2℃,50%RH±5%)与测试基板接触后5秒内的粘附强度。检测设备需配备精密压力控制系统,确保接触压力控制在(700±15)g/cm²范围内。
2. 持粘性检测
依据GB/T 4851标准,将25mm×25mm试样悬挂于标准砝码(1kg±10g)下,记录在(70±2)℃热老化环境中的持续悬挂时间。高端检测系统配备红外热成像模块,可实时监测粘接界面的应力分布变化。
3. 剥离强度测试
使用万能材料试验机(精度±0.5%FS)执行180°剥离试验,测试速度控制在(300±10)mm/min。需同步记录剥离过程中的最大峰值力和平均力值,符合FINAT FTM 2国际标准要求。
4. 环境耐受性检测
包含三项关键测试:
- 高温高湿测试:85℃/85%RH环境下放置500小时
- 冷热冲击测试:-40℃←→85℃循环20次
- UV老化测试:340nm紫外光照射累计1000小时
每次测试后需重新评估粘条率衰减值,衰减率须≤15%方为合格
5. 基材适应性验证
对不同材质(不锈钢、PP塑料、玻璃等)的基板进行差异化测试,建立粘条率与表面能(通过接触角测定仪获取)的对应关系矩阵。特殊场合需模拟实际工况,如汽车部件检测需增加振动测试(频率20-2000Hz,加速度6Grms)。
智能化检测技术发展
当前主流检测系统已集成机器视觉(分辨率≥5μm)、AI瑕疵分类算法和物联网数据管理模块。德国某品牌的最新设备可实现每分钟120件样品的全自动检测,并通过深度学习模型对边缘翘起、胶体迁移等18类缺陷进行毫秒级识别。检测数据实时上传MES系统,实现SPC过程控制与质量追溯。
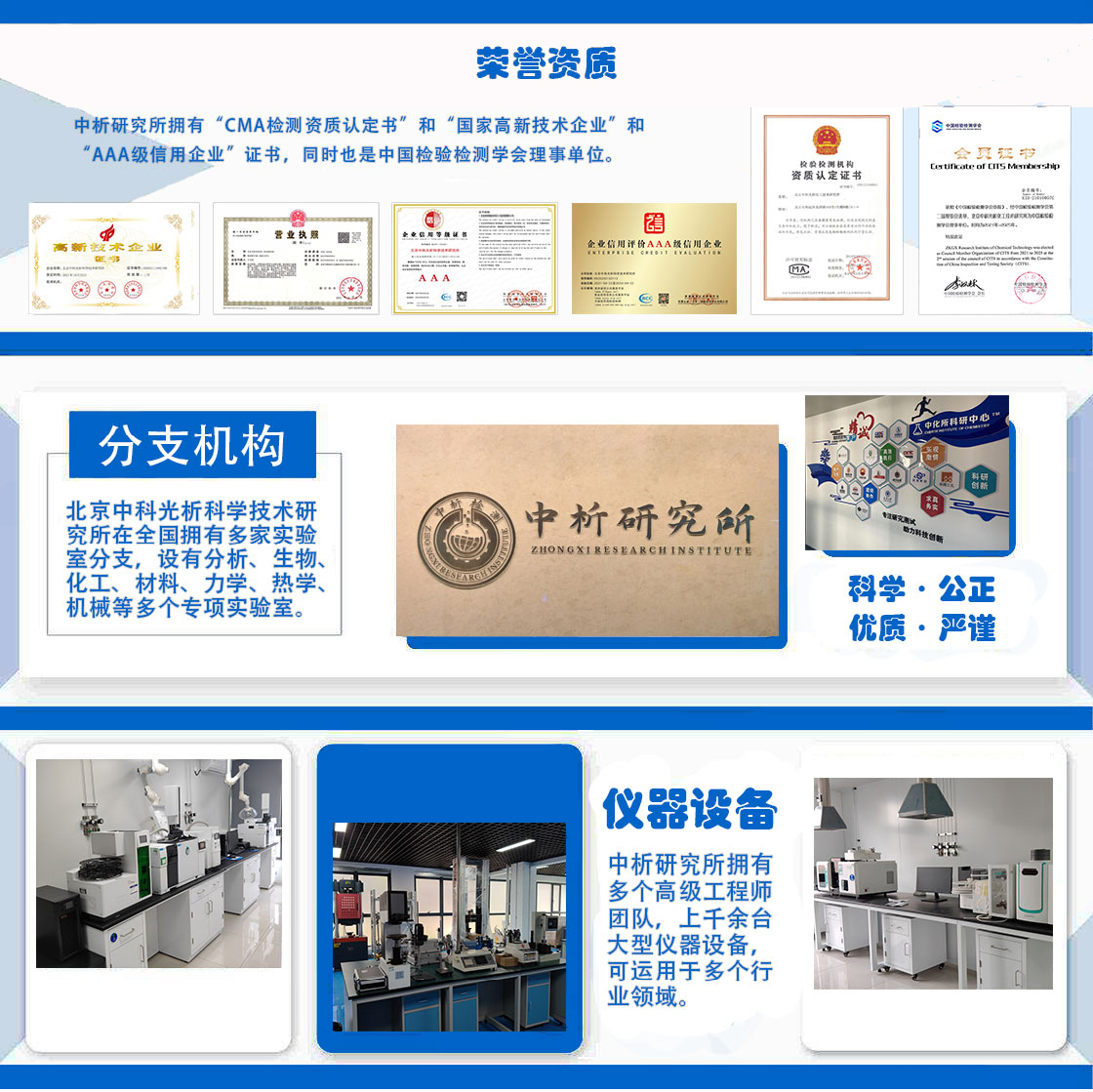
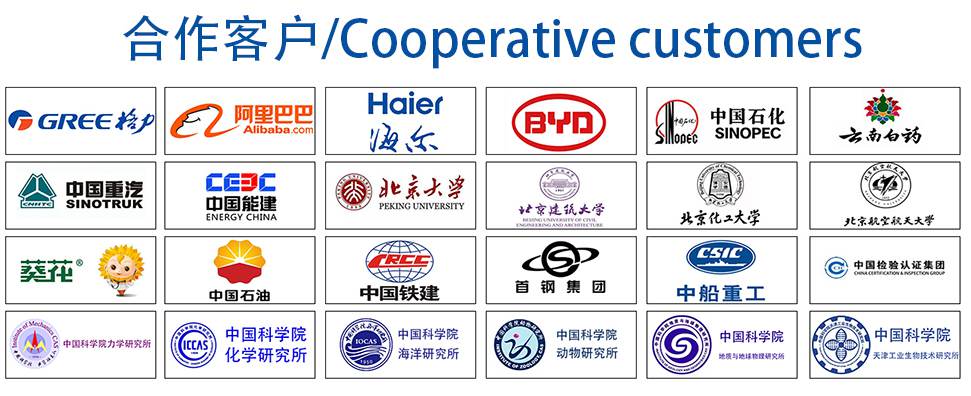