煤矿用液压凿岩机检测的重要性与技术要点
煤矿用液压凿岩机是井下巷道掘进、岩层破碎的核心设备,其性能直接关系到煤矿开采效率和作业安全。由于井下环境复杂多变,设备长期处于高负荷、高冲击、高湿度的工作状态,可能导致液压系统泄漏、零部件磨损、动力输出不稳定等问题。因此,定期开展系统性检测不仅是保障设备正常运行的必要措施,更是预防机械故障、降低安全事故风险、延长设备使用寿命的重要手段。根据国家《煤矿安全规程》(AQ 1043-2007)和《液压凿岩机通用技术条件》(GB/T 23507-2009)要求,液压凿岩机的检测需覆盖机械性能、安全防护、能耗效率等核心指标。
核心检测项目与实施标准
1. 动力性能检测
通过冲击能量测试仪测定凿岩机的冲击频率(标准值≥40Hz)、单次冲击能量(≥180J)及扭矩输出稳定性,要求连续工作状态下功率波动幅度不超过额定值的±5%。测试需模拟实际工作负载,记录液压系统压力曲线,确保在25-35MPa额定压力范围内无异常波动。
2. 液压系统密封性检测
采用荧光示踪法配合压力衰减试验,重点检测主油缸、蓄能器、控制阀组的密封性能。在1.5倍额定压力下保压30分钟,泄漏量应小于0.5mL/min。同时对液压油进行污染度测试,要求NAS 1638标准等级不超过8级。
3. 结构强度与疲劳测试
使用超声波探伤仪对钎尾、活塞杆等关键承力部件进行裂纹检测,磁粉探伤抽查比例不低于20%。通过动态应力测试系统记录8000次冲击循环后的零部件变形量,要求钎尾径向跳动偏差≤0.15mm,活塞杆直线度误差≤0.05mm/m。
4. 安全防护装置检测
验证防卡钎装置的响应时间(≤0.3秒)和脱扣可靠性,模拟钎杆卡死工况进行20次重复试验。检查急停按钮功能有效性,要求断电响应时间≤0.5秒。同时检测减振系统性能,手传振动值应低于2.5m/s²(GB/T 13441标准)。
5. 环境适应性检测
在模拟工况试验台进行72小时连续作业测试,环境温度设定为-10℃至50℃,湿度95%RH条件下验证操控系统可靠性。检测电气部件的IP防护等级,要求电机、控制箱等关键部位达到IP65防护标准。
检测数据管理与改进建议
建立检测数据库,对比历次检测参数变化趋势,针对液压油温升超标(>65℃)、冲击能效衰减(>15%)等情况提出预防性维保方案。推荐每500工作小时进行常规检测,大修周期不超过8000小时。通过数字化检测手段,实现设备健康状态的动态评估,为智能化矿山建设提供数据支撑。
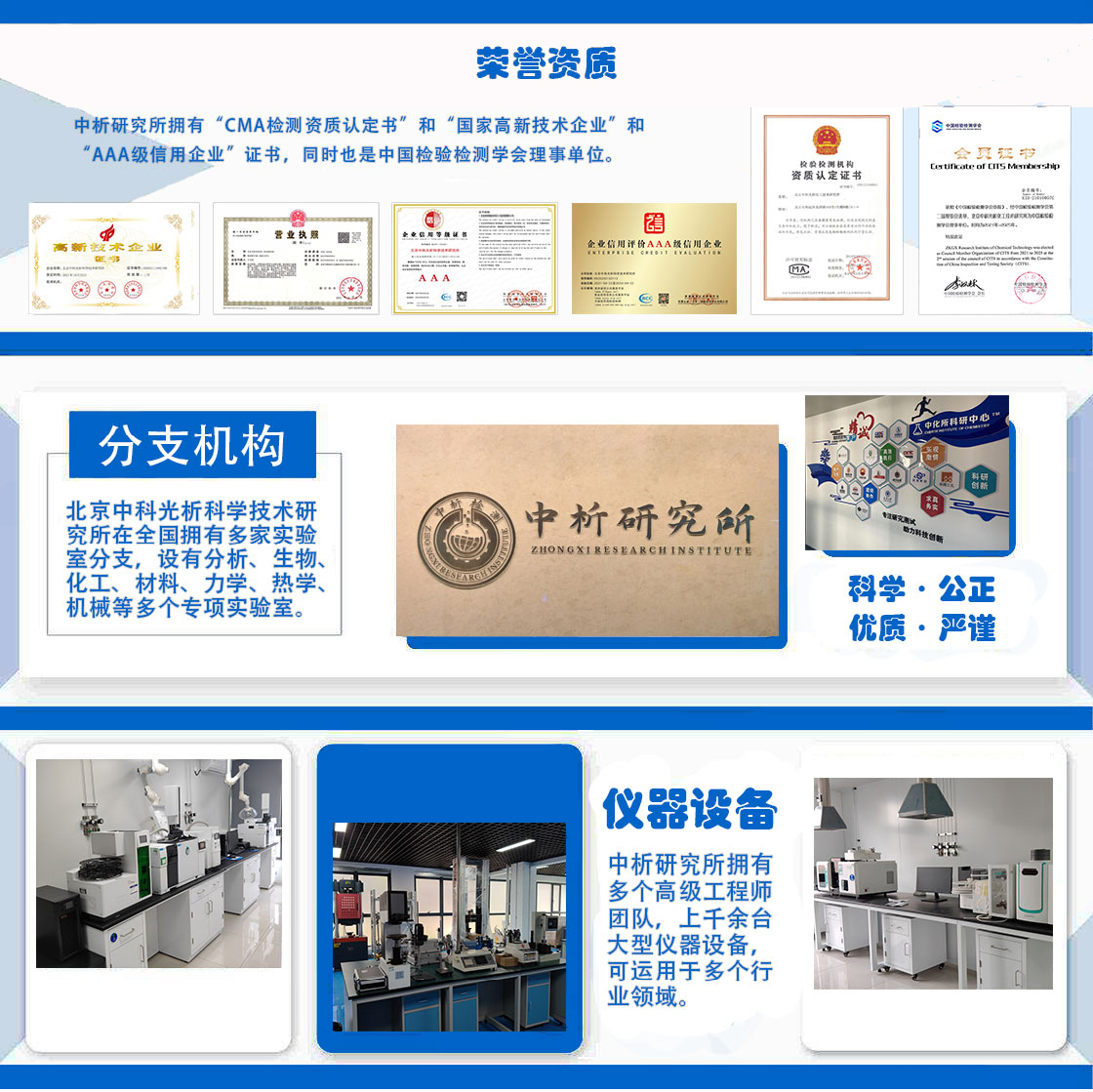
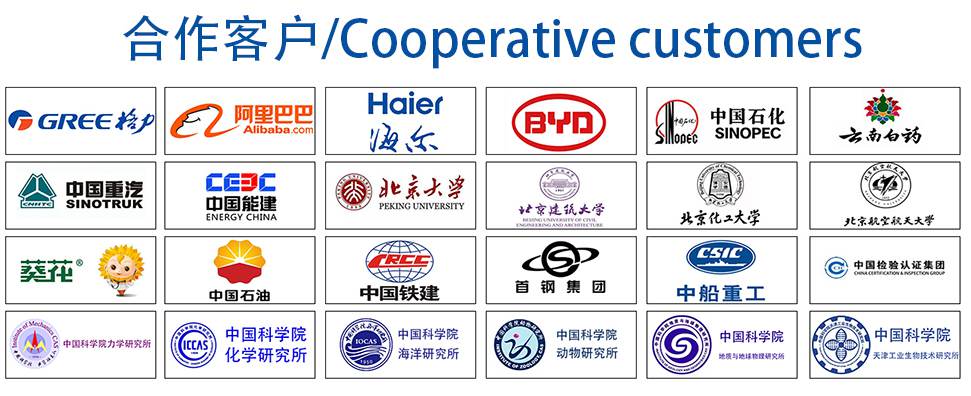