采煤机螺旋滚筒检测的重要性
采煤机螺旋滚筒作为煤矿机械化开采的核心部件,其性能直接影响采煤效率、设备寿命和井下作业安全。滚筒在运行过程中长期承受高强度冲击载荷、煤岩磨损及复杂地质条件考验,可能导致齿座变形、截齿脱落、筒体开裂等问题。开展系统性检测不仅是保障设备安全运行的必要手段,更是实现煤矿高效生产和预防重大事故的关键环节。
核心检测项目与技术规范
1. 几何尺寸与形位公差检测
采用三维激光扫描仪测量滚筒直径、螺旋升角、叶片间距等关键参数,对比GB/T 25706-2010《采煤机螺旋滚筒》标准要求。重点检查筒体同轴度误差(≤0.5mm/m)、端面跳动量(≤1.2mm)及叶片对称度,确保装配精度符合设计指标。
2. 动平衡性能测试
通过动平衡试验机在模拟转速(30-120r/min)下检测滚筒质量分布,要求残余不平衡量不超过G6.3级标准。异常振动值(>4.5mm/s)需通过配重调整,避免高速旋转时引发整机共振。
3. 焊接质量无损检测
对齿座焊缝、筒体环焊缝进行100%超声波探伤(UT)和20%射线探伤(RT),按照NB/T 47013-2015标准评定缺陷等级。重点关注未熔合、气孔、裂纹等缺陷,单个气孔直径不得超过2mm,裂纹类缺陷零容忍。
4. 材料力学性能验证
取样检测筒体材料(如Q690D高强度钢)的拉伸强度(≥750MPa)、冲击韧性(-20℃时≥34J)及硬度值(HB280-320)。对截齿进行洛氏硬度检测(HRC55-60)和耐磨层厚度测量(≥3mm),确保材料性能满足极端工况需求。
5. 截齿装配可靠性检测
使用扭矩扳手抽检20%截齿的安装紧固力矩(180-220N·m),同时进行50次模拟截割试验。要求齿套无松动位移、截齿脱落率低于0.3%,齿座定位销剪切强度需达到设计值的1.5倍以上。
6. 耐磨层厚度与附着力测试
采用涡流测厚仪测量叶片堆焊层厚度(≥8mm),划格法检测涂层附着力(≥15MPa)。对磨损率超过25%的区域进行硬度梯度分析,判断是否需要补焊修复。
智能检测技术应用趋势
随着工业4.0技术的发展,基于机器视觉的自动探伤系统、搭载振动传感器的在线监测平台逐步普及。通过建立滚筒全生命周期数据库,可实现对磨损量、应力分布的预测性维护,检测效率提升40%以上,为智能矿山建设提供技术支撑。
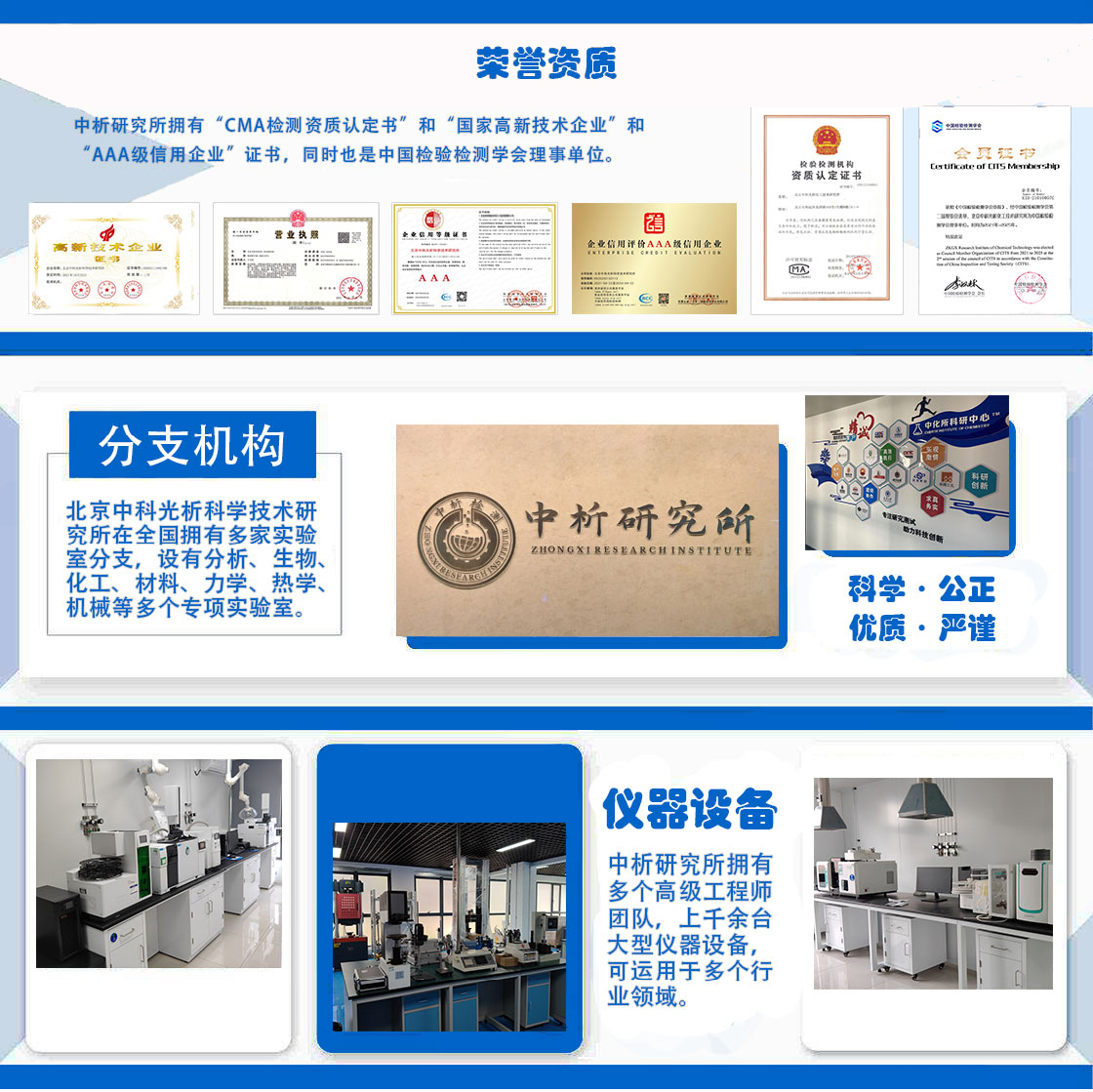
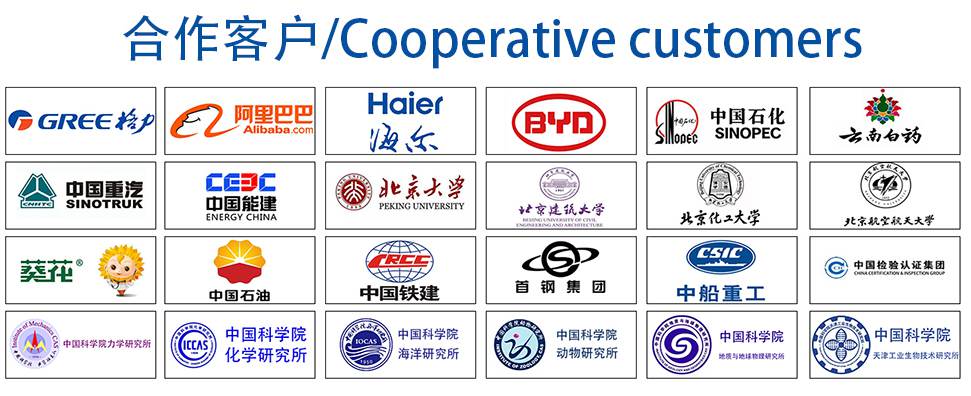