液压调速阀检测的重要性与核心项目解析
液压调速阀作为液压系统中的核心控制元件,其性能直接影响设备的运动精度、稳定性和能耗效率。在工程机械、冶金设备、船舶动力等工业领域,调速阀需要长期承受高压、高频振动和油液污染的严苛工况,因此定期检测与维护成为保障系统可靠性的关键环节。专业的检测流程不仅能够预判潜在故障,还能通过参数校准延长元件使用寿命,降低因阀体失效导致的生产停滞风险。
一、静态性能测试
通过专用试验台架验证额定压力下的流量-压力特性曲线,检测内容包括:
1. 最低启动压力测试(检测阀芯运动摩擦力)
2. 压力补偿精度验证(使用高精度压力传感器采集数据)
3. 流量稳定性测试(在油温40±4℃下连续运行2小时)
二、动态响应特性检测
采用电液伺服阀测试系统评估阀体动态性能:
- 阶跃响应时间测定:输入信号突变时阀口开度的响应延迟
- 频率响应特性:绘制Bode图分析相位裕度与幅频特性
- 负载突变适应性:模拟突然增载时的压力波动恢复时间
三、密封性能专项检测
使用氮气检漏仪配合液压油浸泡法进行多维度检测:
1. 静密封测试:在1.5倍额定压力下保压10分钟
2. 动密封检测:模拟高频换向动作后的泄漏量测量
3. 阀芯与阀体配合间隙检测(精度要求0.005-0.015mm)
四、材料耐久性分析
通过理化实验室手段评估关键零部件状态:
- 阀芯表面镀层厚度检测(铬层厚度≥0.03mm)
- 弹簧疲劳强度测试(100万次循环后的形变量)
- 密封件材料硬度测试(邵氏硬度70±5范围内)
五、环境适应性验证
在温控试验箱内模拟极端工况:
1. 低温启动测试(-20℃环境冷启动特性)
2. 高温耐久试验(90℃油温连续运行200小时)
3. 抗污染能力检测(NAS 10级污染油液下的性能衰减)
实施检测时需严格遵循ISO 10770-1、GB/T 8105等行业标准,结合在线监测与离线检测技术,运用振动分析仪、油液颗粒计数器等齐全仪器,构建涵盖全生命周期的检测体系。通过建立关键参数的数字化档案,可实现故障预测与精准维护,将液压系统故障率降低50%以上。
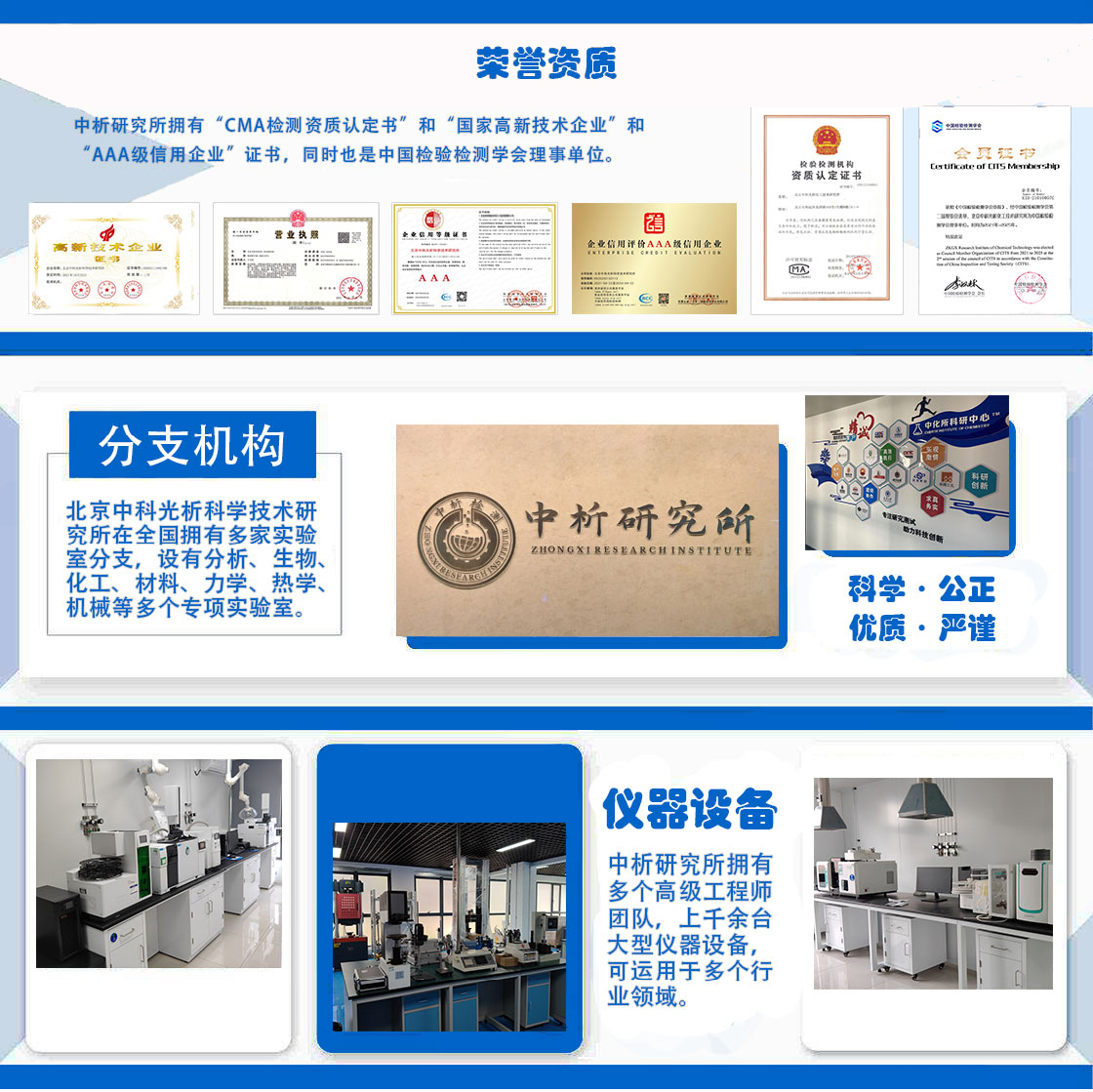
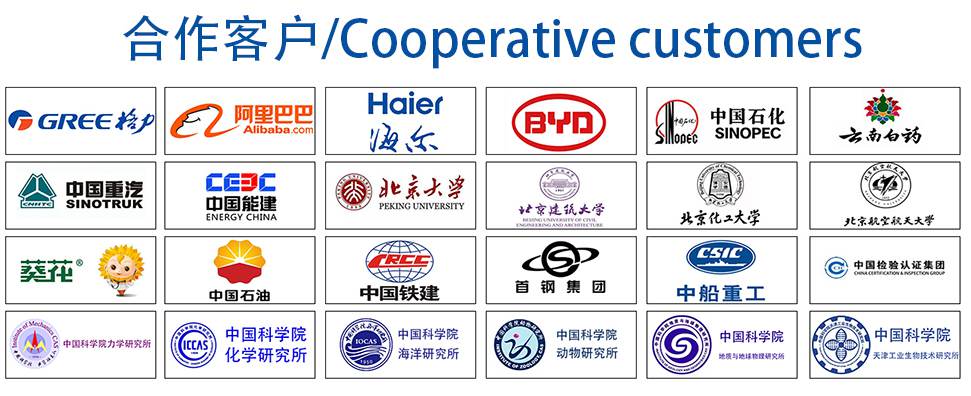