液压轴向柱塞泵检测的核心内容与流程
液压轴向柱塞泵作为液压系统的核心动力元件,其性能直接影响设备运行效率和安全性。由于长期处于高压、高速工况下,泵体易出现磨损、泄漏、效率下降等问题,定期检测成为预防故障、延长使用寿命的关键措施。检测过程需结合机械性能测试、密封性验证和材料损耗分析,涵盖静态与动态参数,并参照GB/T 7935、ISO 4409等行业标准,确保检测结果的准确性和可比性。
关键检测项目及技术要点
1. 容积效率测试:通过测量实际输出流量与理论流量的比值(通常要求≥90%),判断柱塞副配合间隙、配流盘磨损程度。需在额定压力和转速下使用流量计进行动态检测。
2. 压力性能检测:包括额定压力测试、压力波动值测量(应≤±1.5MPa)及压力冲击耐受试验,使用压力传感器记录泵出口压力曲线,分析压力脉动是否超标。
3. 温度与温升监控:在连续运转工况下,采用红外热像仪监测泵体温度分布,油液温升应不超过35℃,异常高温可能预示配流副烧蚀或轴承失效。
4. 振动与噪声分析:利用加速度传感器和声级计采集数据,振动烈度值需符合JB/T 7043标准,高频噪声异常可能反映气蚀或机械碰撞问题。
5. 泄漏检测:包含外泄漏(壳体密封)和内泄漏(柱塞/配流副间隙)检测,采用氦质谱检漏仪或流量对比法,内泄漏率应小于额定流量的5%。
辅助检测与维护建议
材料磨损评估:通过油液铁谱分析检测金属磨粒浓度,配合柱塞表面硬度测试(HRC58-62)和缸体粗糙度检测(Ra≤0.4μm),量化关键部件磨损量。
控制机构检查:对变量机构的伺服阀响应特性、斜盘摆动角度进行标定,确保排量调节精度误差≤2%,必要时进行动态响应特性曲线测试。
检测周期建议每运行2000小时或年检一次,检测后需根据结果更换密封件、调整配合间隙或修复磨损表面。对于效率下降超过15%或压力波动超标的泵体,应立即进行大修或更换,避免引发系统级故障。
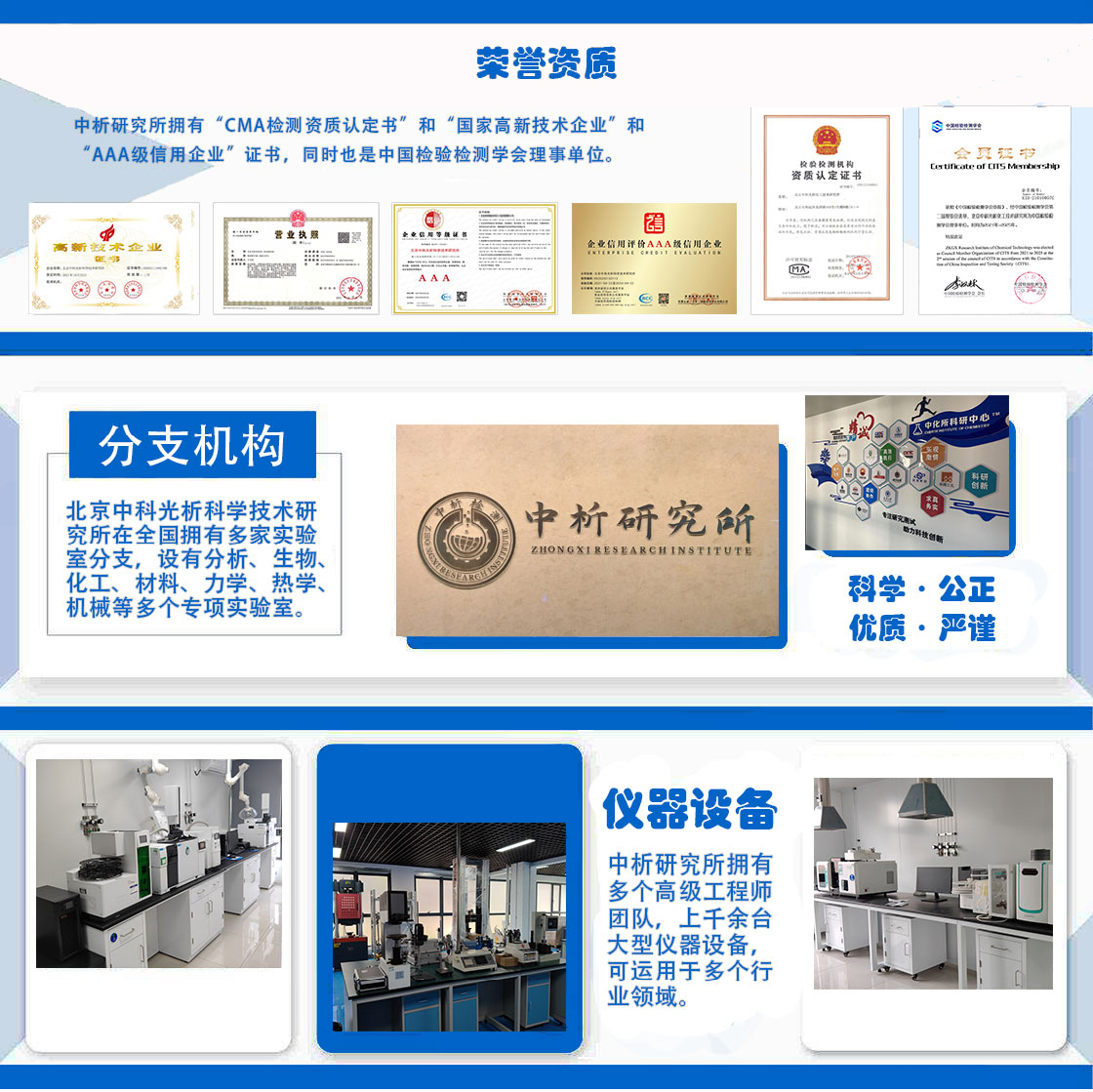
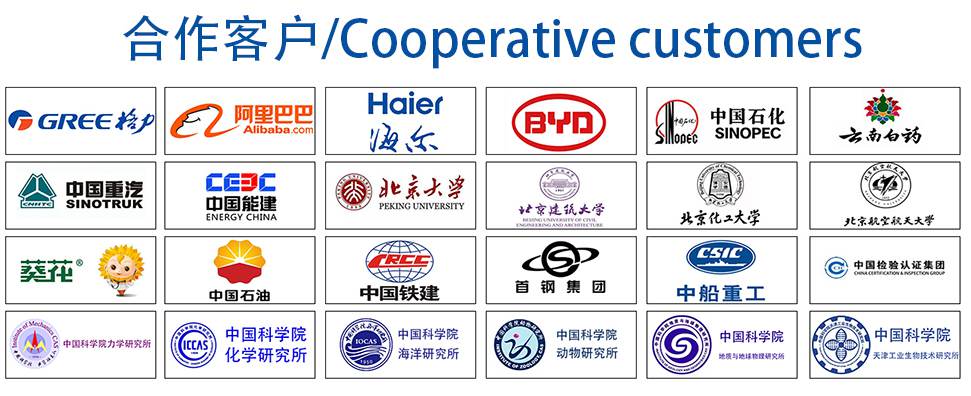