复合材料缺陷检测的重要性与技术挑战
复合材料因其高强度、轻量化及耐腐蚀等特性,被广泛应用于航空航天、汽车制造、风力发电等高端领域。然而,其制造过程中易出现分层、孔隙、裂纹、异物夹杂等内部缺陷,直接影响结构安全性和使用寿命。传统人工目视检测已无法满足精度需求,而基于齐全技术的自动化检测成为行业刚需。据国际航空协会统计,复合材料失效案例中约65%源于未及时发现的隐蔽缺陷。因此,开发高效、精准的缺陷检测技术是保障复合材料应用安全的关键环节。
核心检测项目与技术方法
1. 超声检测(Ultrasonic Testing, UT)
利用高频声波在材料中的传播特性,通过接收反射波信号识别缺陷位置与尺寸。相控阵超声(PAUT)技术可生成三维成像,实现0.1mm级孔隙检测,适用于碳纤维层合板的分层检测。该技术需配合耦合剂使用,检测速度可达5m²/h。
2. 射线检测(X-ray/CT检测)
通过X射线穿透材料后形成的衰减图像分析内部结构,工业CT技术可实现微米级分辨率的三维重构。特别适用于蜂窝夹芯复合材料中胶接失效、芯材塌陷等复杂缺陷的识别,检测精度达±0.05mm。
3. 红外热像检测(IRT)
基于材料热传导差异的主动式检测方法,通过外部热源激励后捕捉表面温度场变化。可快速筛查大面积复合材料中的脱粘、分层缺陷,典型检测灵敏度为3mm直径缺陷,适用于风电叶片等现场检测场景。
4. 激光剪切散斑检测(LSSI)
利用激光干涉原理捕捉材料受载后的表面位移场异常,对近表面裂纹具有高敏感性。适用于检测0.5mm深度的表面下裂纹,在航空航天复材构件检测中误差率低于0.3%。
5. 声发射监测(AE)
通过捕捉材料受载时缺陷扩展释放的弹性波,实现动态损伤评估。可在线监测复材结构服役过程中的裂纹扩展行为,频率范围覆盖20kHz-1MHz,定位精度优于5mm。
智能化检测技术发展趋势
随着深度学习算法的突破,基于机器视觉的自动缺陷识别系统(ADR)正在快速普及。采用YOLO、U-Net等网络模型,结合多模态数据融合技术,可将缺陷分类准确率提升至98%以上。德国弗劳恩霍夫研究所开发的AI检测平台,已实现每分钟600张CT图像的实时分析能力。未来5G+工业互联网的深度应用,将进一步推动复合材料检测向云端化、远程化方向发展。
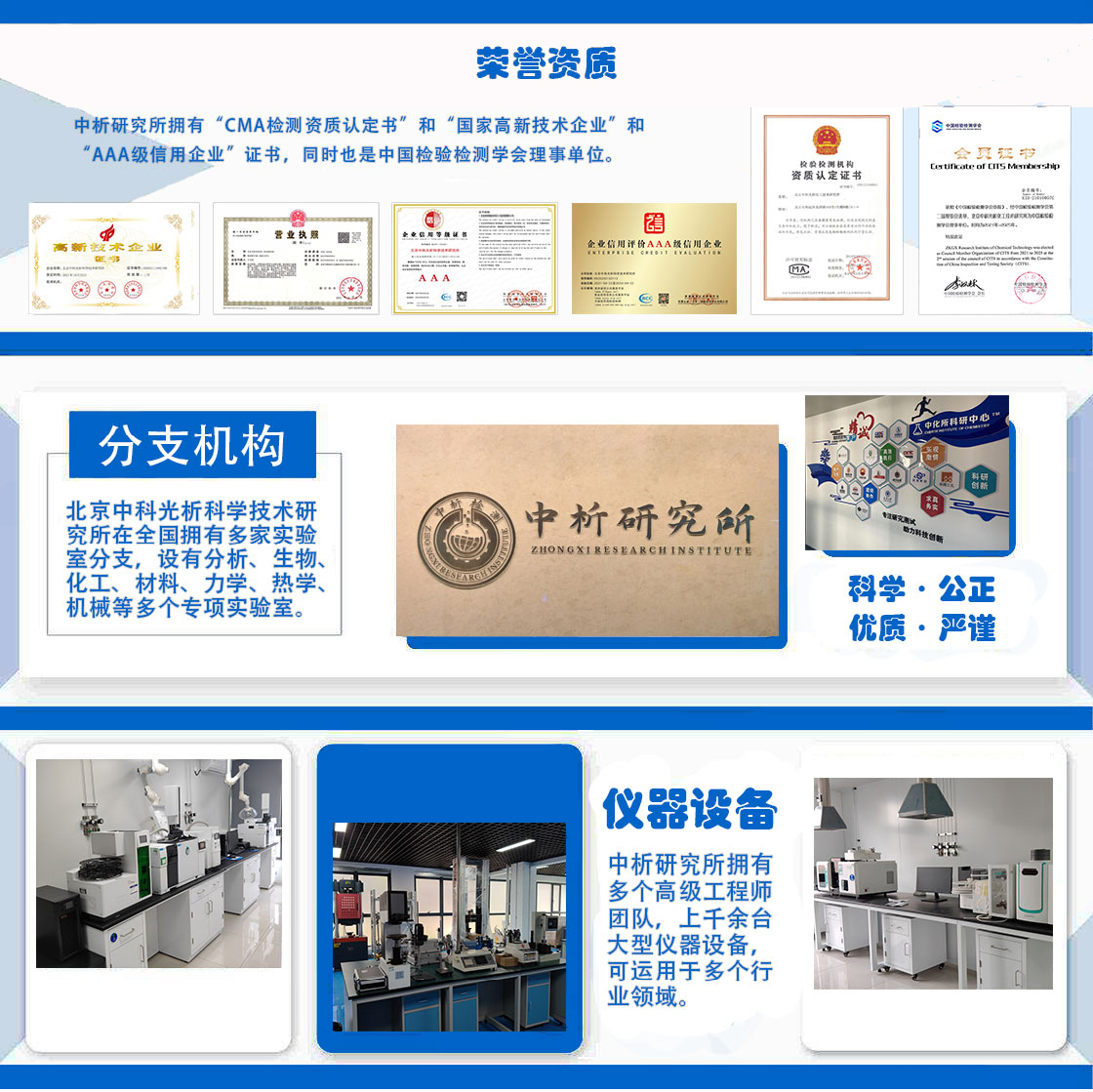
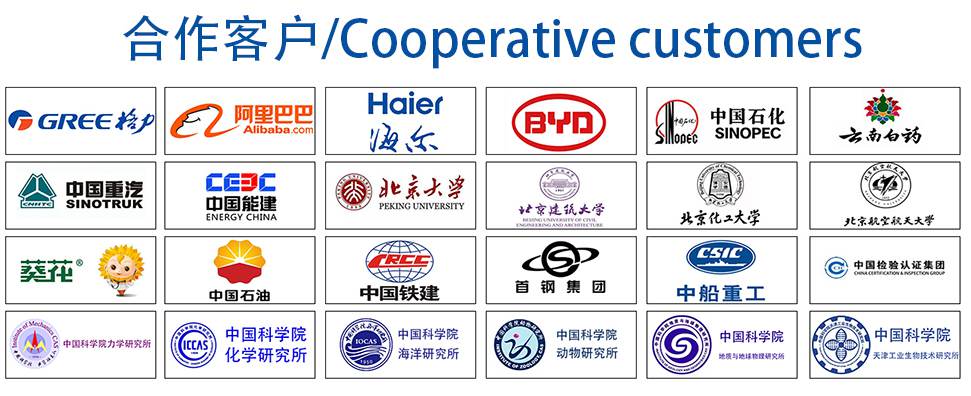