机器人用谐波齿轮减速器检测
实验室拥有众多大型仪器及各类分析检测设备,研究所长期与各大企业、高校和科研院所保持合作伙伴关系,始终以科学研究为首任,以客户为中心,不断提高自身综合检测能力和水平,致力于成为全国科学材料研发领域服务平台。
立即咨询机器人用谐波齿轮减速器检测的重要性
谐波齿轮减速器作为机器人关节驱动的核心部件,其性能直接决定了机器人运动的精度、稳定性和寿命。随着工业自动化与协作机器人需求激增,谐波齿轮减速器的检测要求愈发严格。由于其在高速、高负载、微小间隙等复杂工况下运行,任何制造缺陷或装配误差都可能导致传动效率下降、振动加剧甚至失效。因此,从原材料筛选到成品验收的全流程检测体系,已成为保障机器人可靠性的关键技术环节。
关键检测项目及方法
1. 传动精度测试
通过高精度激光干涉仪和编码器测量输入/输出轴的转角误差,评估单向重复定位精度(≤1 arcmin)和回差(≤3 arcmin)。需在额定扭矩下进行正反向加载测试,模拟实际工况下的齿隙变化。
2. 扭转刚度分析
采用扭矩传感器搭配角度测量系统,绘制扭矩-转角曲线。检测轴向/径向刚度比值是否满足ISO 1328标准,确保减速器在动态负载下变形量不超过设计阈值的0.05°。
3. 温升与效率测试
在恒温箱内进行连续72小时满载试验,利用红外热像仪监测柔轮应力集中区域的温度分布。要求温升不超过45℃且传动效率≥85%,同时检测润滑油黏度变化是否在±10%允许范围内。
4. 谐波发生器的波发生器检测
使用三坐标测量仪(CMM)验证椭圆凸轮的短轴公差(±0.005mm),配合圆度仪检测柔性轴承的轨道轮廓度误差(≤0.002mm)。通过有限元分析验证应力分布均匀性。
5. 疲劳寿命试验
基于GB/T 14229标准搭建加速寿命试验台,以2倍额定负载进行10^7次循环测试。监测齿面磨损形态,评估柔轮材料的应力腐蚀敏感性,要求失效前寿命≥8000小时。
智能检测技术应用趋势
当前检测系统正向智能化方向发展,包括基于机器视觉的齿面缺陷自动识别、应用数字孪生技术的虚拟标定平台,以及结合大数据分析的寿命预测模型。例如,通过振动频谱分析可实时监测谐波齿轮的阶次特征,提前预警装配偏心或润滑不良等潜在故障。这些创新技术将检测精度提升至亚微米级,检测效率提高40%以上。
结语
谐波齿轮减速器的检测体系需要兼顾传统机械性能验证与新型智能诊断技术。随着协作机器人对紧凑化、轻量化需求的提升,检测项目将更注重微观形貌分析、材料晶相检测等精细化指标。只有通过科学严谨的检测手段,才能确保谐波齿轮减速器在机器人应用中实现精准、稳定、长寿命的运动传递。
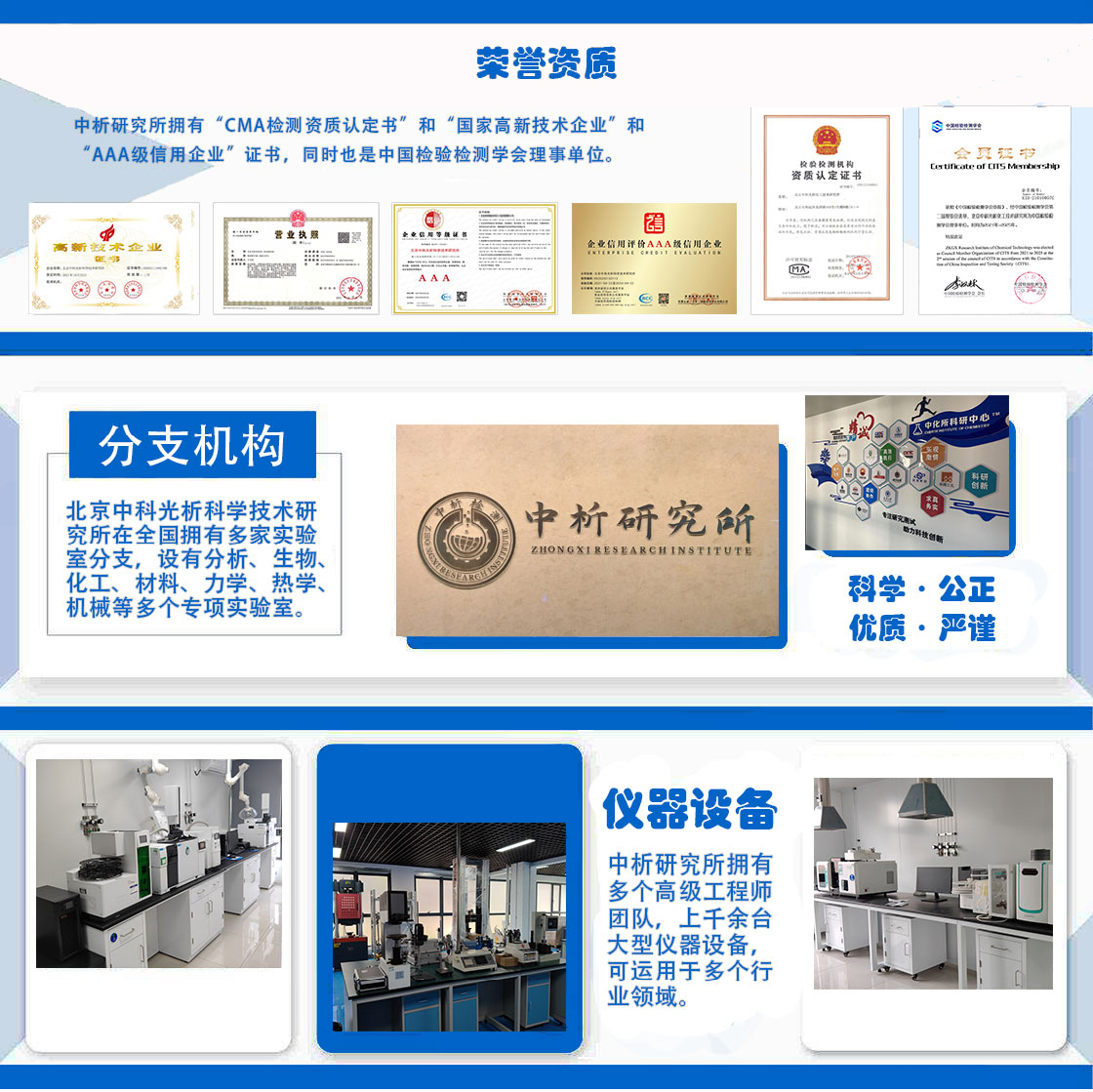
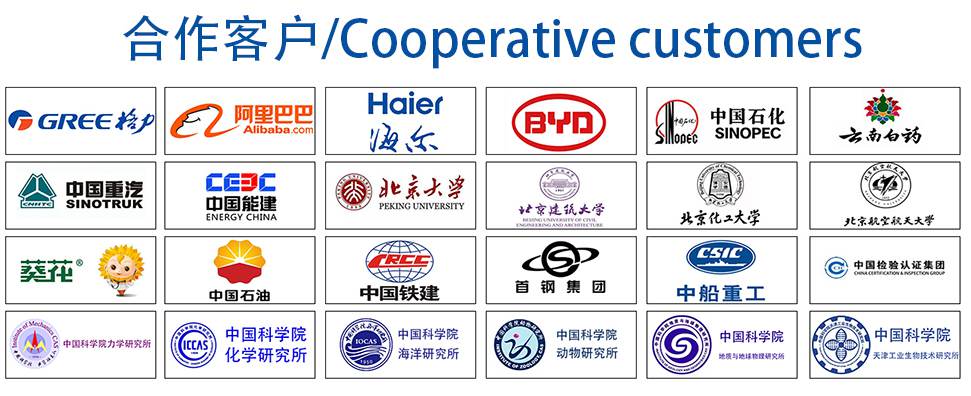