液化石油气发动机检测
实验室拥有众多大型仪器及各类分析检测设备,研究所长期与各大企业、高校和科研院所保持合作伙伴关系,始终以科学研究为首任,以客户为中心,不断提高自身综合检测能力和水平,致力于成为全国科学材料研发领域服务平台。
立即咨询液化石油气发动机检测的重要性与核心项目解析
随着环保政策的推进和能源结构的调整,液化石油气(LPG)发动机因其清洁、高效的特点,在公共交通、货运车辆及特种设备领域得到广泛应用。然而,与传统燃油发动机相比,LPG发动机在燃料供给、燃烧效率及排放控制等方面存在显著差异。为确保其安全运行、降低故障率并满足排放标准,定期开展全面检测成为关键环节。通过系统化的检测项目,既能保障设备性能稳定,也能延长发动机寿命,同时助力实现绿色低碳目标。
一、燃料系统检测
作为LPG发动机的核心,燃料系统的检测包括储气罐密封性测试、管路压力检测、电磁阀响应速度验证及减压蒸发器工作状态评估。需使用专用检漏仪对气罐连接处进行泄漏扫描,并通过压力传感器监测燃料供给稳定性,防止因气体泄漏或压力异常导致的燃烧不充分或安全隐患。
二、点火系统与燃烧效能检测
检测项目涵盖火花塞电极间隙测量、点火线圈电压输出测试、燃烧室积碳分析及空燃比校准。通过示波器采集点火波形,判断点火时序的准确性;同时利用尾气分析仪检测CO、HC等浓度,评估混合气燃烧效率,必要时调整ECU参数以优化动力输出。
三、排放控制系统专项检测
重点针对三元催化器转化效率、氧传感器信号精度及EGR阀(废气再循环阀)作动性能进行测试。通过对比催化器前后端的排放数据,判断催化装置是否失效;同时检测EGR系统是否有效降低氮氧化物排放,确保符合国六等最新排放法规要求。
四、机械部件磨损诊断
包括气缸压缩压力测试、曲轴箱通风系统检查、正时机构同步性验证以及润滑系统油压监测。使用内窥镜观察气缸壁磨损情况,结合机油金属颗粒分析预判机械故障风险,防止因部件老化导致的功率下降或异常磨损。
五、电子控制系统完整性检测
通过OBD(车载诊断系统)读取故障代码,验证ECU对各执行器的控制逻辑。检测项目涉及燃气喷射脉宽信号测试、节气门位置传感器校准、温度/压力传感器数据合理性判断,以及CAN总线通信状态的诊断,确保电控系统与机械部件的协同运作。
六、安全装置功能性验证
强制检测气罐过压保护装置、紧急切断阀响应速度、碰撞传感器联动机制及燃气浓度报警系统。模拟异常工况触发安全保护程序,测试自动断气、报警提示等功能的可靠性,构建多层级安全保障体系。
定期开展上述检测项目,不仅能显著降低LPG发动机的故障率,还能提升燃料经济性20%-30%。结合智能化诊断设备与大数据分析技术,可建立预测性维护模型,为LPG动力设备的全生命周期管理提供科学依据。
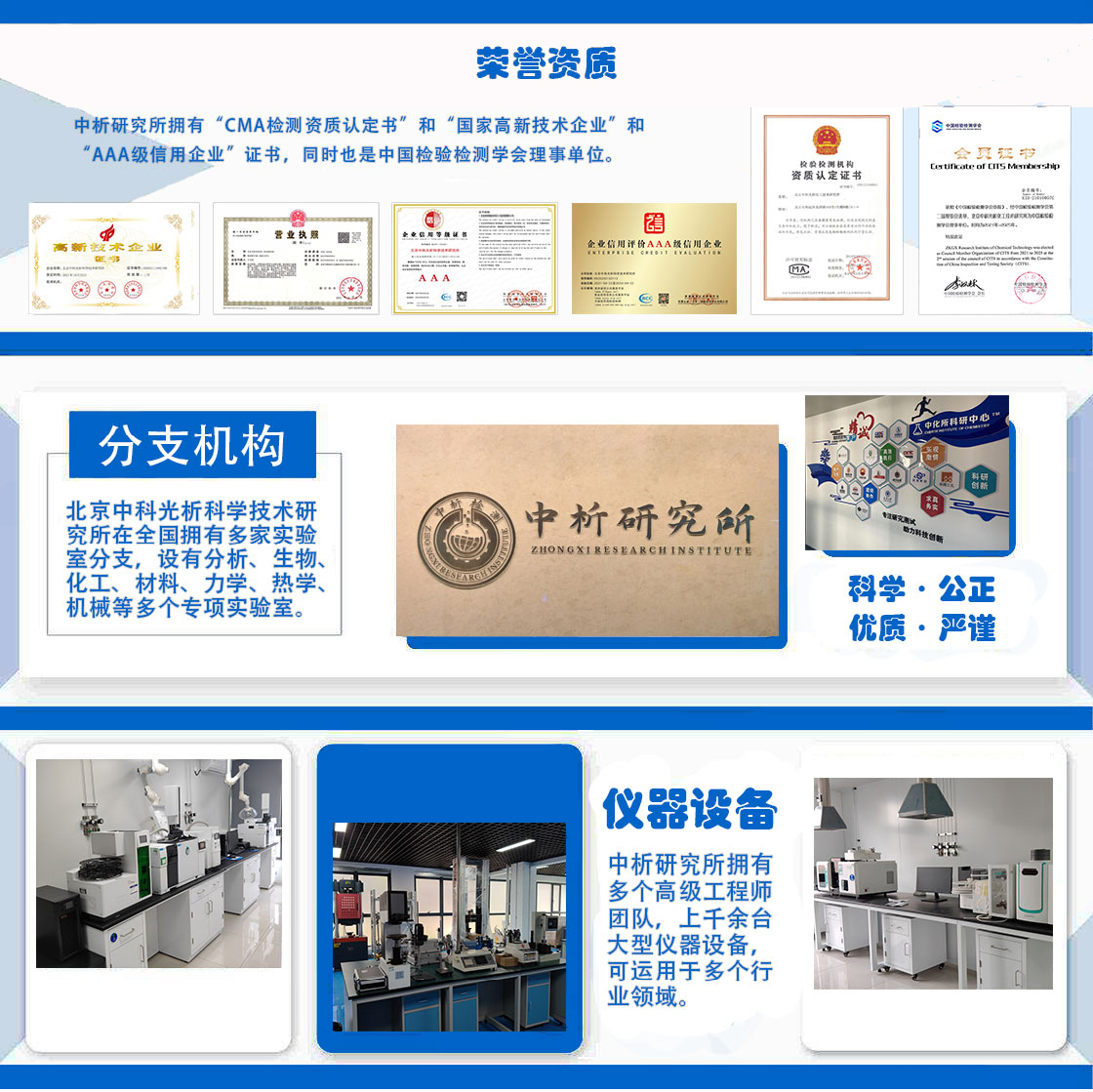
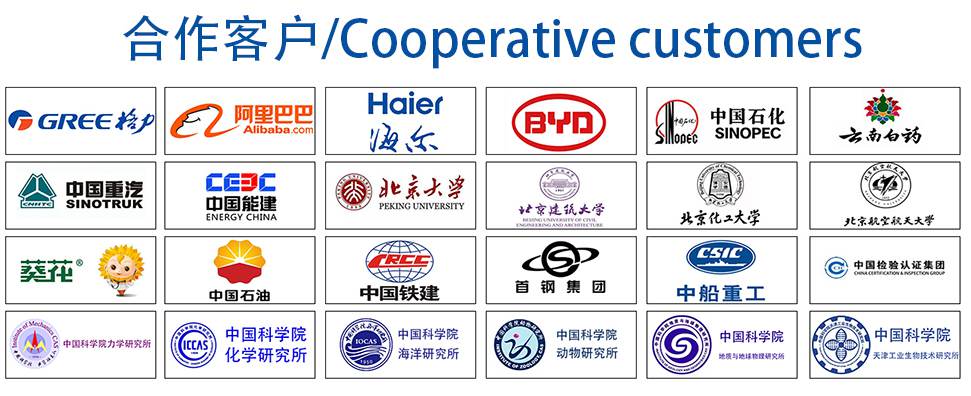