焊接切割及类似工艺用压力表检测的重要性
在焊接、切割及类似工业工艺中,压力表是保障设备安全运行和工艺质量的核心仪表之一。它用于实时监测气瓶、管道或系统中气体、液体的压力值,直接影响设备稳定性、操作人员安全及工艺精度。例如,在氧乙炔切割中,压力表的异常可能导致气体比例失调,引发回火甚至爆炸;在氩弧焊工艺中,保护气压力不足则会导致焊缝氧化缺陷。因此,压力表的定期检测与校准不仅是行业规范要求,更是预防事故、提升生产效率和产品质量的必要手段。
关键检测项目及标准
1. 基本性能检测
包括量程覆盖范围验证、指针归零测试、表盘刻度清晰度检查以及指针运动平稳性评估。需依据GB/T 1226-2017《一般压力表》标准,确保压力表在静态和动态条件下均能准确反映压力值。
2. 环境适应性测试
模拟高温、低温、震动、粉尘等工况环境,检测压力表的密封性(如IP防护等级)和抗干扰能力。焊接车间常见的电磁干扰、振动冲击可能影响仪表精度,需通过抗振性能测试(如GB/T 17214.3)确认其可靠性。
3. 安全防护检测
重点检查过压保护装置(如防爆膜、泄压阀)、耐压强度(1.5倍最大工作压力保压试验)以及连接部件的密封性。对于氧气压力表,还需严格检测油脂残留,避免与高纯度氧气接触引发燃爆风险。
4. 精度校准与误差分析
使用标准压力源(活塞式压力计或数字校准仪)进行多点校准(含零点、满量程及中间点),计算示值误差、回程误差和重复性误差。根据JJG 52-2013《弹性元件式一般压力表检定规程》,精度等级需符合工艺要求(通常不低于2.5级)。
5. 材料与结构检查
核查压力表外壳材质(如不锈钢防锈性能)、弹簧管耐腐蚀性以及接头螺纹规格(如G1/4、M20×1.5)。针对焊接切割中常见的酸性气体(如CO₂保护焊),需额外评估仪表内部元件的抗腐蚀能力。
检测周期与维护建议
常规工况下压力表应每6个月检测一次,连续振动或高频使用场景需缩短至3个月。日常使用中需避免剧烈冲击、超量程使用,并定期清洁表盘观察窗。检测不合格的压力表应立即停用,严禁通过调整齿轮机构等方式进行非标修复。
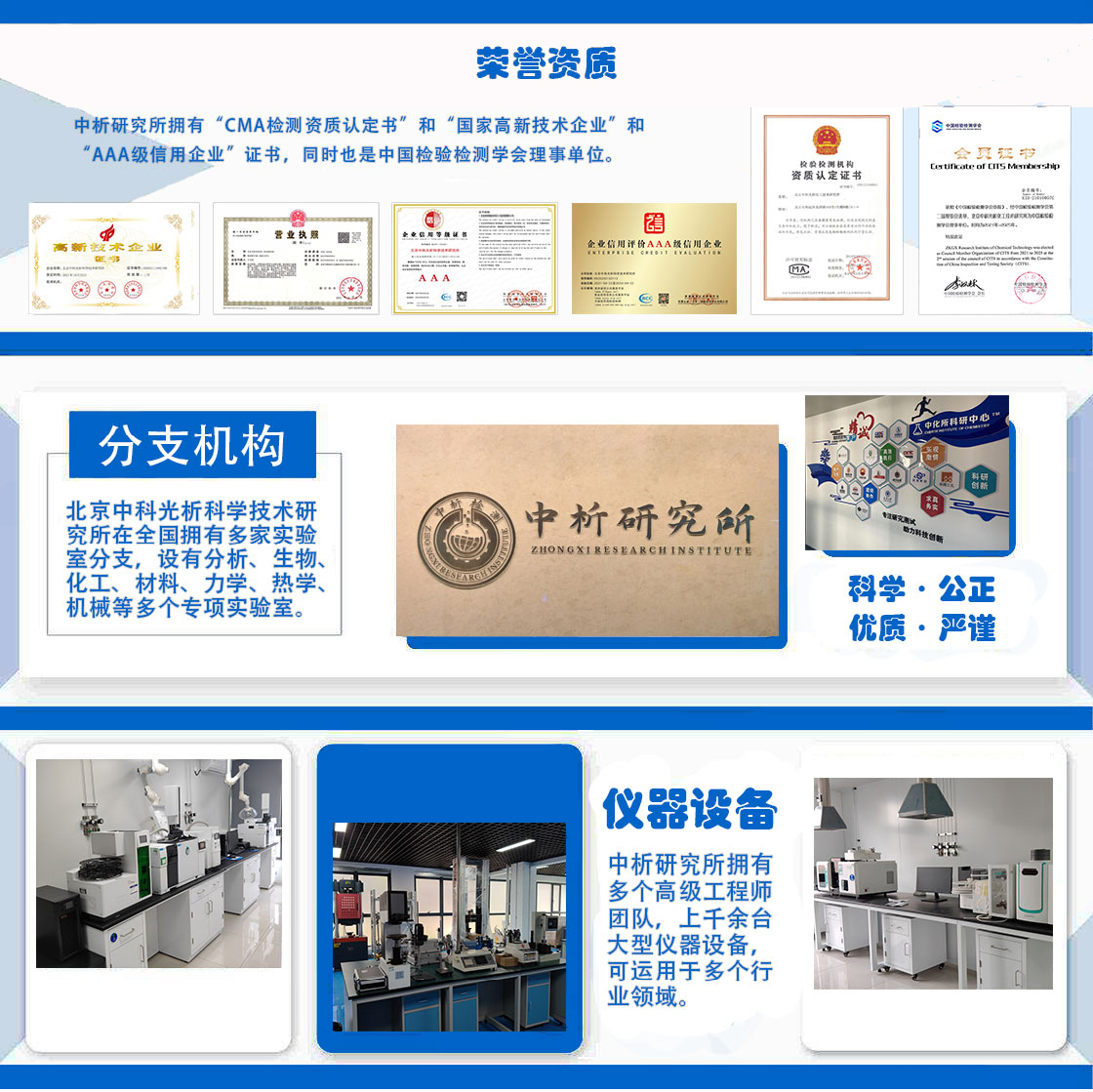
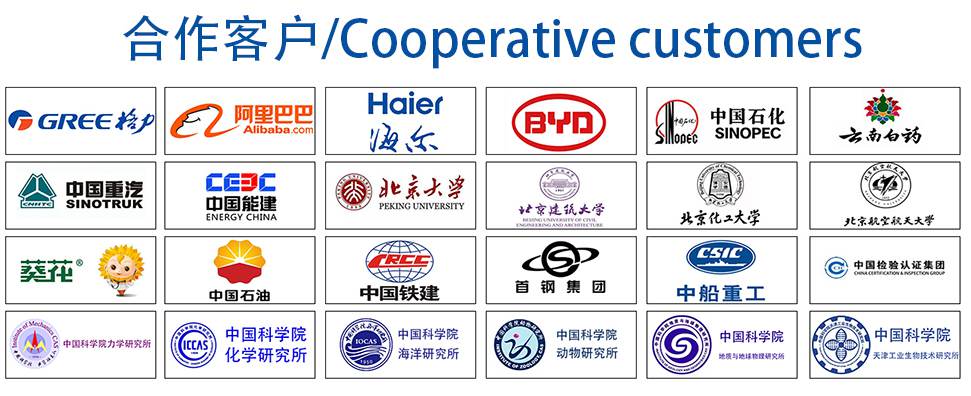