乘用车用前桥检测的重要性
乘用车前桥作为车辆底盘系统的核心部件,承担着转向、承载、传递驱动力与制动力等多重功能,其性能直接影响车辆的安全性、操控性和舒适性。随着汽车工业对轻量化、高强度和智能化要求的提升,前桥的结构设计与材料选择日益复杂。为确保车辆在复杂路况和长期使用中的可靠性,前桥检测成为生产制造、质量控制和维修保养中不可或缺的环节。通过科学的检测手段,能够及时发现材料缺陷、装配误差或疲劳损伤,避免因前桥失效导致的转向失灵、车轮脱落等重大安全隐患。
前桥检测的主要项目
1. 外观与几何尺寸检测
通过目视检查、三维扫描或影像测量仪,检测前桥表面是否存在裂纹、变形、锈蚀等缺陷。几何尺寸检测包括主销内倾角、前轮外倾角、轮距、轴头端面跳动等关键参数,需符合GB/T 26043-2010《汽车驱动桥台架试验方法》等行业标准。
2. 材料性能检测
包括材料化学成分分析、金相组织观察、硬度测试及抗拉强度试验。例如,对高强度钢前桥需检测其屈服强度是否达到500MPa以上,铝合金材质需验证耐腐蚀性和疲劳寿命。超声波探伤和磁粉探伤常用于检测内部裂纹或夹杂缺陷。
3. 动态性能测试
在模拟工况下进行静载试验与疲劳试验,评估前桥的承载能力和耐久性。典型测试包括: - 垂直静载荷试验:施加1.5倍额定载荷,检测变形量是否≤1.5mm - 扭转刚度试验:测量扭矩-变形曲线,确保刚度系数≥8000N·m/rad - 循环疲劳试验:模拟15万次交变载荷后,检查是否出现断裂或塑性变形
4. 装配配合精度检测
重点检查转向节、轮毂轴承、制动器等关键零部件的配合间隙。轮毂轴向间隙需控制在0.05-0.15mm,主销与衬套的配合过盈量应满足0.02-0.05mm的精度要求。激光对中仪可快速检测整体装配的同轴度误差。
5. 智能化检测技术应用
随着智能制造的发展,机器视觉系统可实时监测焊接质量,嵌入式传感器可采集前桥运行时的应力、温度数据。基于大数据的预测性维护系统能提前识别潜在故障,检测效率较传统方式提升40%以上。
结语
乘用车前桥检测是保障车辆安全的核心环节,需从材料、工艺、装配到动态性能进行全维度验证。通过建立标准化检测流程并引入智能化技术,可显著提升产品质量控制水平,为消费者提供更安全可靠的驾乘体验。
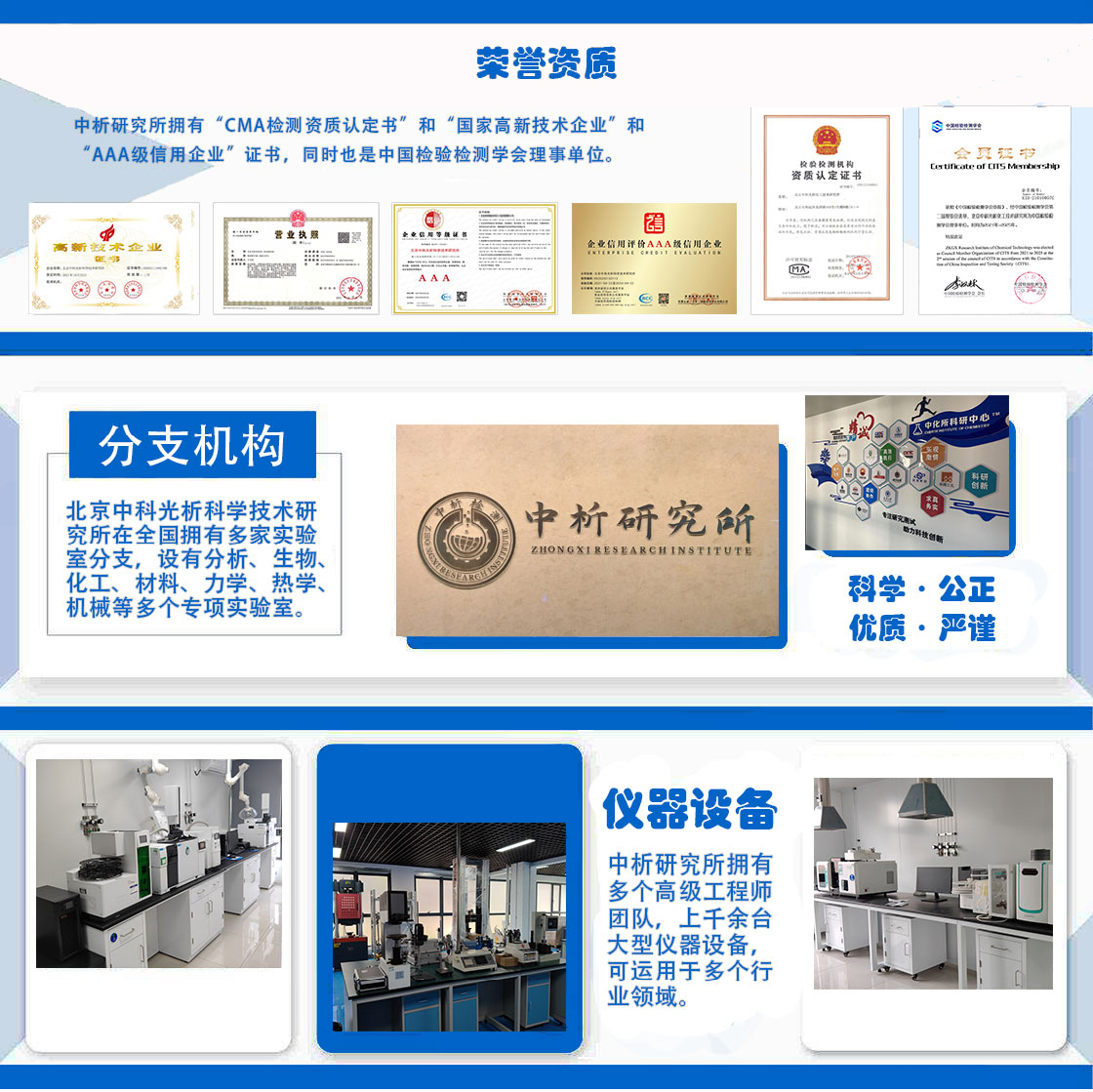
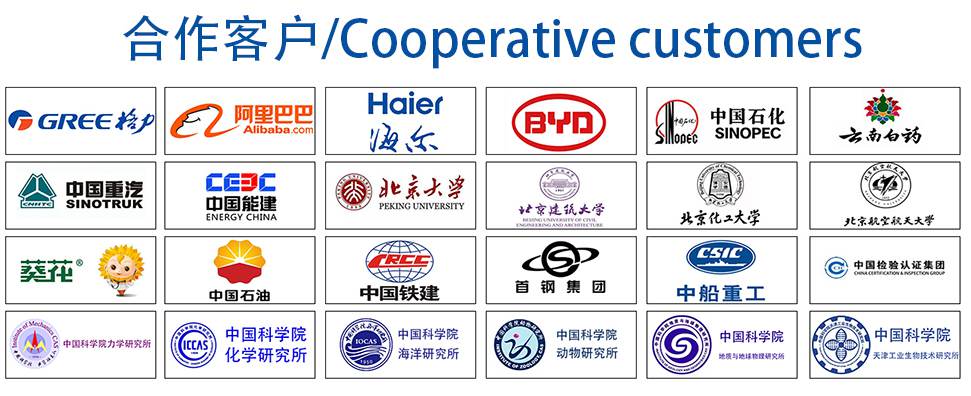