电动汽车用动力蓄电池循环寿命检测的意义与挑战
随着新能源汽车产业的快速发展,动力蓄电池作为电动汽车的“心脏”,其性能与寿命直接决定了车辆的使用成本和用户体验。循环寿命检测是衡量动力蓄电池在多次充放电过程中性能衰减程度的核心指标,也是保障电池安全性和经济性的关键技术环节。根据相关统计,动力蓄电池的制造成本约占整车成本的40%-50%,而其循环寿命的延长可显著降低用户更换电池的频次和成本。因此,围绕动力蓄电池循环寿命的标准化检测已成为行业技术攻关的重点领域。
动力蓄电池循环寿命检测的核心项目
在国家标准(GB/T 31486-2015、GB/T 31484-2015)和行业规范中,动力蓄电池循环寿命检测主要包含以下关键项目:
1. 充放电循环测试
通过模拟实际使用场景,对电池进行恒流-恒压(CC-CV)充电和恒流放电的循环操作。测试过程中需记录每次循环的容量保持率、能量效率及电压平台变化,直至电池容量衰减至初始值的80%(行业通用寿命终点标准)。典型测试需完成1000-3000次循环,耗时长达数月。
2. 容量衰减分析
容量衰减是循环寿命的核心表征指标。检测时需结合库仑效率测试,分析电池在循环过程中的活性物质损失、电解液分解和SEI膜增厚等现象对容量的影响。通过电化学阻抗谱(EIS)和差分电压分析(DVA)等技术,可进一步揭示容量衰减的微观机制。
3. 内阻变化监测
电池内阻的升高会直接导致能量效率下降和热失控风险增加。检测中需采用直流内阻(DCR)和交流阻抗法(ACIR)动态监测循环过程中的欧姆内阻、电荷转移阻抗和扩散阻抗变化。内阻增长率超过15%时,通常判定电池进入衰退期。
4. 温度特性测试
通过高低温环境箱模拟-20℃至55℃工况,评估温度对循环寿命的影响。重点观察低温析锂、高温SEI膜分解等异常现象,并建立温度-循环次数-容量衰减的三维关联模型。
5. 安全性验证
在循环寿命测试末期,需对电池进行过充、短路、针刺等滥用测试,验证其热稳定性。安全检测数据将为电池管理系统(BMS)的阈值设定提供依据。
检测技术难点与发展趋势
当前动力蓄电池循环寿命检测面临测试周期长(单次测试需3-6个月)、工况模拟复杂度高、多因素耦合分析困难等挑战。行业正加速推进加速老化测试方法(如提高充放电倍率)、数字孪生技术和大数据预测模型的开发。未来,结合AI算法的寿命预测精度有望提升至95%以上,检测周期可缩短50%-70%,为动力电池技术迭代提供更强支撑。
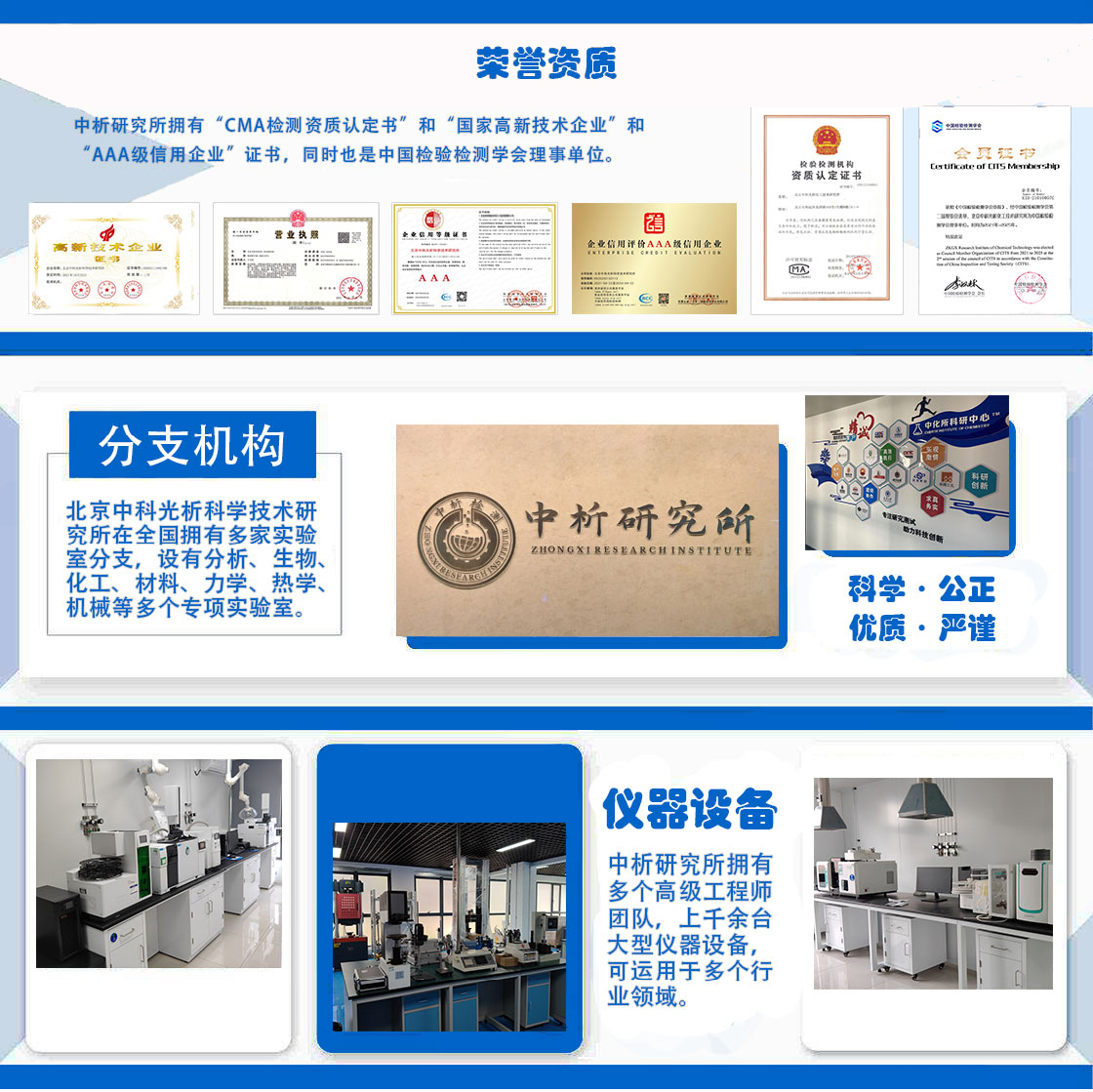
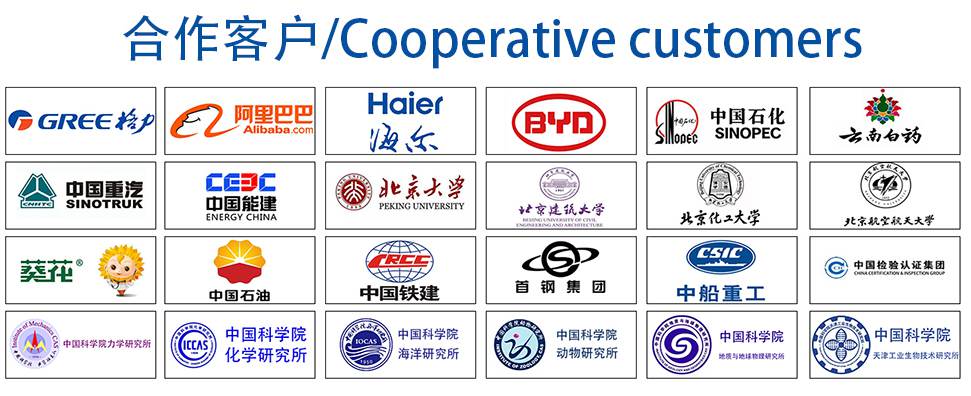