制动间隙调整臂检测的重要性
制动间隙调整臂作为车辆制动系统的核心部件,承担着调节刹车片与制动鼓/盘之间间隙的关键功能。其性能直接关系到制动响应速度、制动力分配均匀性以及紧急情况下的行车安全。随着车辆使用时间的增加,调整臂可能因磨损、腐蚀或机械疲劳导致功能失效,进而引发制动滞后、偏磨甚至制动失效等严重问题。因此,定期开展制动间隙调整臂的专项检测不仅是车辆维护的必要环节,更是预防交通事故、保障道路安全的重要技术手段。
关键检测项目及技术要求
1. 外观与尺寸检测
通过目视检查结合精密量具测量,确认调整臂表面无裂纹、变形及过度磨损。重点测量蜗轮蜗杆啮合间隙(通常要求≤0.15mm)、壳体安装孔直径公差(需符合ISO 286标准)、调节臂总成轴向窜动量(规范值≤0.3mm)等关键尺寸参数。
2. 动作性能测试
在专业试验台上模拟不同工况,检测调整臂的自动调节功能。包括:在30-200N·m扭矩范围内检验调节灵敏度(响应时间应<0.5秒),测试反向空程角度(须≤5°),以及验证双向往复调节的同步精度(偏差≤±0.1mm)。
3. 耐久性试验
采用液压脉冲试验系统模拟5万次以上调节循环,检测部件表面硬度变化(HV值波动应<10%)、密封件老化程度(渗漏量≤0.1ml/h),并记录调节力衰减曲线(末期输出力不得低于初始值的85%)。
4. 材料分析
通过光谱检测验证蜗杆材料是否达到20CrMnTiH标准,壳体铸件需满足QT600-3球墨铸铁成分要求。关键接触面硬化层深度应达到0.8-1.2mm,显微硬度HV550-650,确保耐磨性能。
5. 防腐蚀检测
依据GB/T 10125标准进行盐雾试验,电镀件需通过720小时中性盐雾测试,达9级腐蚀等级;磷化处理件应满足480小时无红锈要求。关键配合面粗糙度Ra≤3.2μm以保持密封性。
6. 标识规范性检查
核查产品标识是否完整包含制造商代码、生产批次、材料等级、最大调节行程等技术参数,二维码追溯系统需能完整读取制造工艺数据和质检记录。
检测标准与设备配置
检测过程应严格参照GB 12676-2014《商用车制动系统技术要求及试验方法》及ISO 7634:2015相关条款。推荐配置三坐标测量仪(精度±1.5μm)、动态扭矩传感器(量程0-300N·m)、显微硬度计(HV标尺)及智能型盐雾试验箱等专业设备,确保检测结果的科学性和权威性。
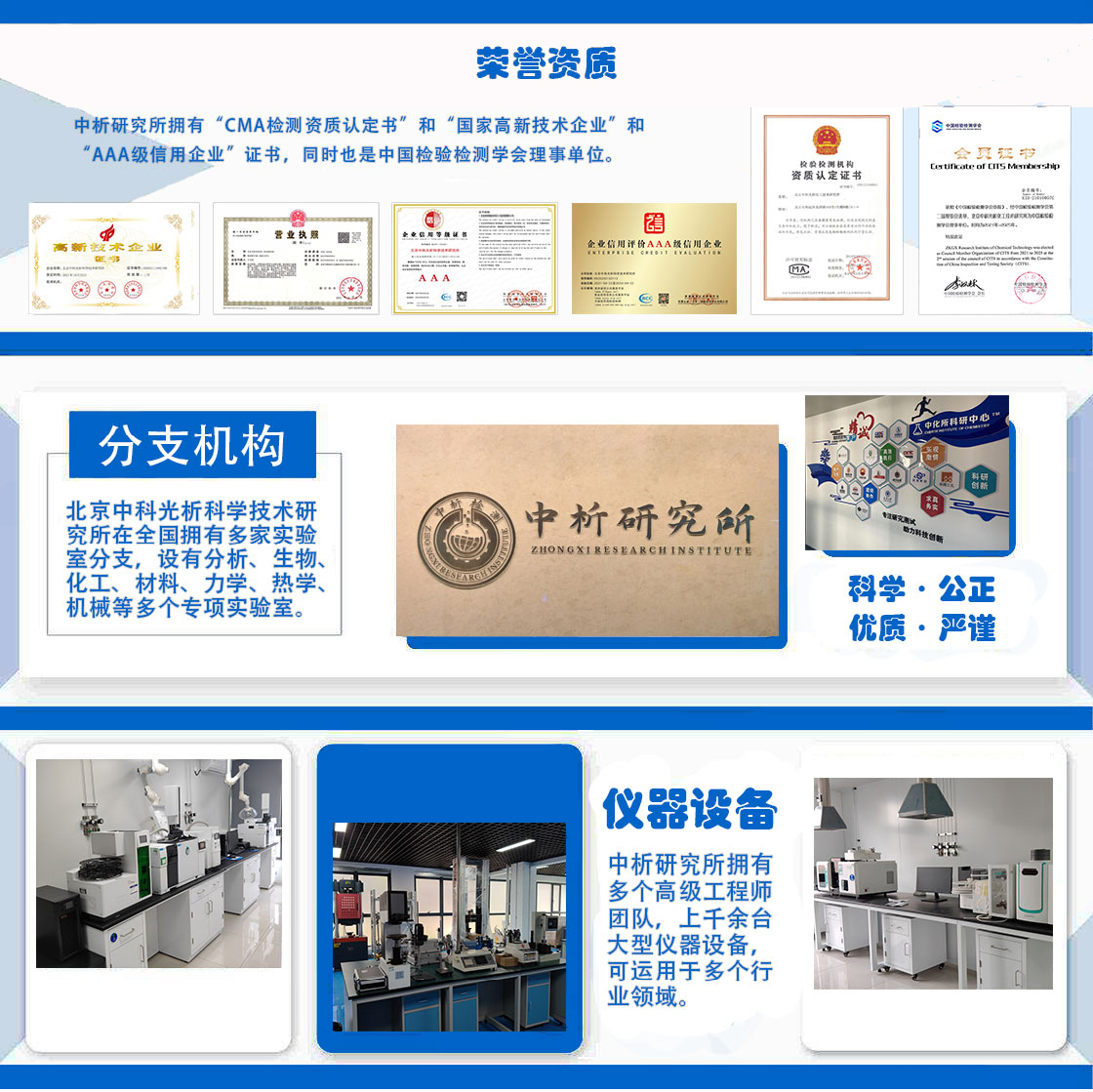
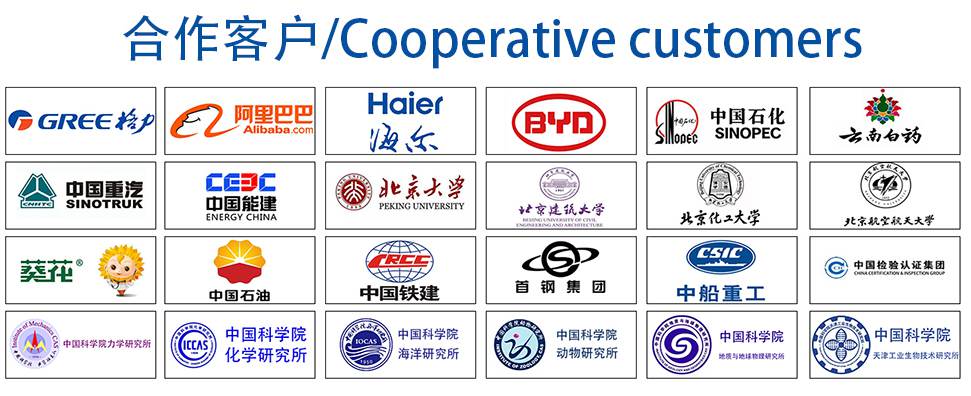