机动车用液化石油气钢瓶检测的重要性
机动车用液化石油气(LPG)钢瓶作为清洁能源车辆的核心部件,其安全性直接关系到车辆运行和人员生命财产保障。由于LPG具有易燃易爆特性,且钢瓶长期承受高压、振动及环境腐蚀,国家强制标准要求定期进行专业检测。通过系统化的检测项目,可及时发现钢瓶潜在缺陷,避免因泄漏、爆裂等事故引发严重后果。我国《特种设备安全法》明确规定,液化石油气钢瓶使用周期内需每3-5年接受一次全面检验,出租车等高频使用车辆更需缩短检测周期。
核心检测项目与技术规范
1. 外观与结构完整性检测
通过目视检查、磁粉探伤等手段,重点检测瓶体表面是否存在裂纹、凹陷、腐蚀或变形。使用测厚仪测量关键部位壁厚,对比原始数据判断金属损耗率。根据GB/T 8334标准,瓶体凹陷深度超过1.5%直径或腐蚀面积达30%即需报废。
2. 阀门系统密封性检测
采用氦质谱检漏仪或肥皂水试验法,对安全阀、充装阀、液位计等组件进行气密性测试。压力保持试验要求达到工作压力的1.5倍并稳压3分钟,压降不得超过0.5%。同时检查O型圈、密封垫等易损件的老化状况。
3. 内胆超声波探伤
使用数字式超声波探伤仪对钢瓶内壁进行100%扫查,检测内部夹渣、气孔等制造缺陷,以及使用过程中产生的疲劳裂纹。检测分辨率需达到Φ2mm当量平底孔,符合TSG R0006-2014《气瓶安全技术监察规程》要求。
4. 水压爆破试验
对抽样钢瓶进行破坏性试验,通过分级加压测定实际爆破压力,验证残余强度系数。试验压力应为设计压力的3倍以上,确保钢瓶在极端工况下的安全裕度。试验后需进行金相分析,评估材料性能退化程度。
智能检测技术发展
随着物联网技术的普及,新一代检测系统已实现数据在线采集与云端分析。通过植入式传感器可实时监测钢瓶压力波动、温度变化及应力分布,配合AI算法预测剩余使用寿命。部分检测机构开始应用X射线数字成像(DR)技术,实现非接触式高精度缺陷识别,检测效率提升40%以上。
检测结果处理规范
经检测合格的钢瓶需在瓶肩部位打刻下次检验日期,并绑定电子标签实现全生命周期追溯。存在轻微缺陷的钢瓶允许返厂维修,但返修次数不得超过2次。达到报废标准的钢瓶必须进行去功能化处理,通过钻孔、切割等方式永久消除再充装可能。
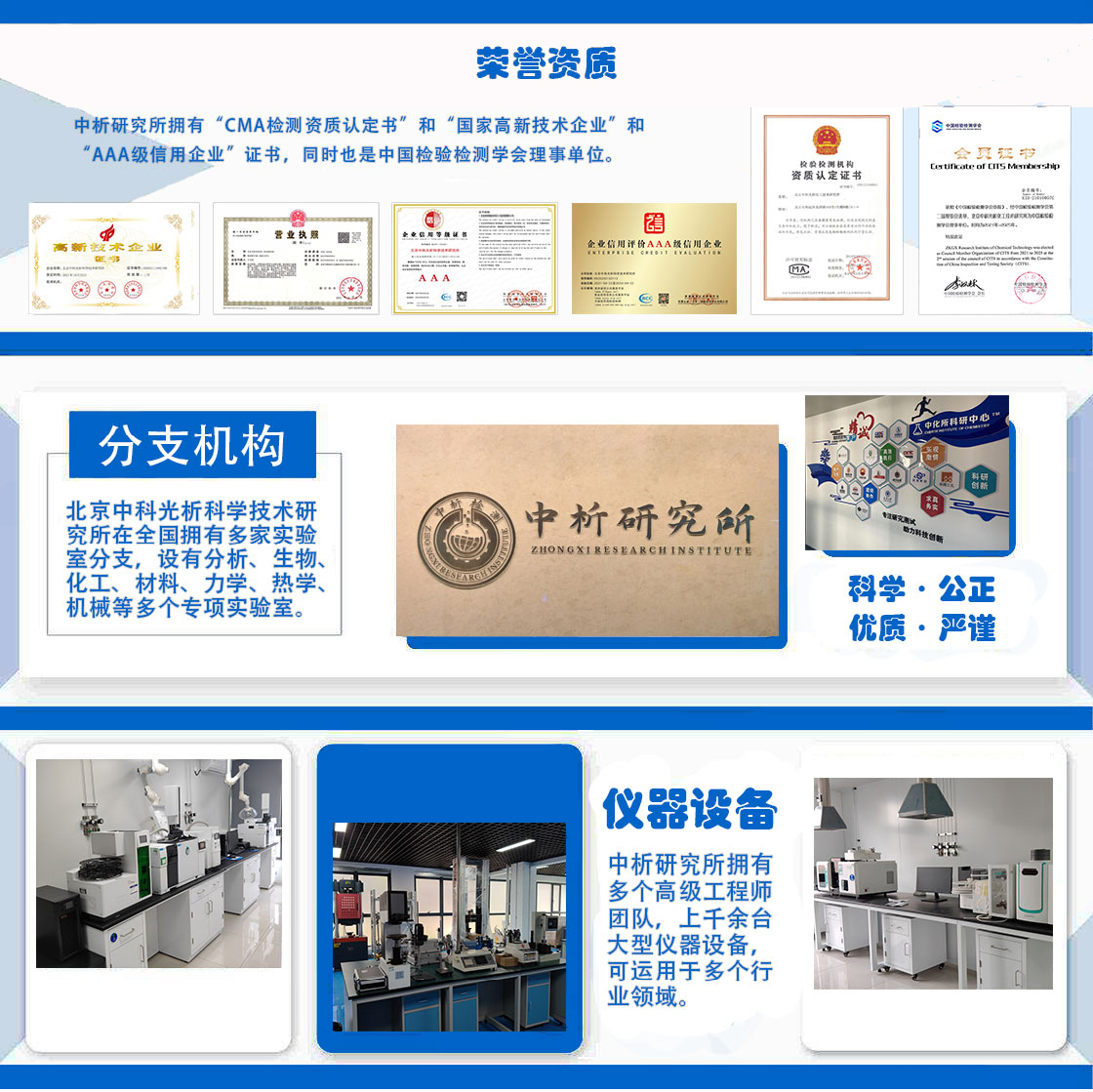
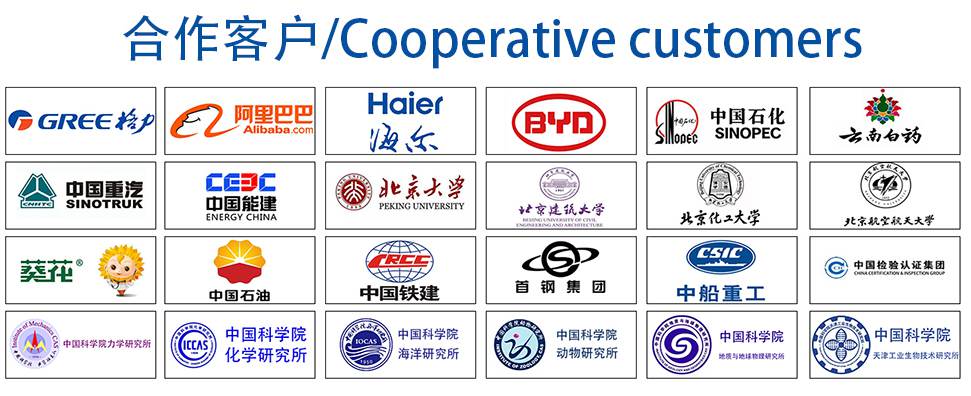