营运车辆爆胎应急安全装置检测的重要性
随着道路交通流量的激增和车辆使用频率的提高,营运车辆的安全性能备受关注。其中,爆胎是引发重大交通事故的主要诱因之一,据行业统计,高速行驶中爆胎导致的车辆失控占交通事故总数的15%以上。为应对这一风险,爆胎应急安全装置(如爆胎应急支撑装置、失压续跑系统等)已成为客车、货车等营运车辆的标配设备。然而,装置的质量稳定性与功能可靠性直接影响其实际防护效果。因此,建立科学规范的检测体系,定期对营运车辆爆胎应急安全装置进行系统性检测,成为保障道路运输安全的重要技术手段。
核心检测项目与技术要求
1. 装置结构完整性检测
通过三维扫描与力学分析,验证装置主体结构是否满足GB/T 35178-2017标准规定的抗变形要求。重点检测支撑臂厚度误差(需≤0.2mm)、连接部件焊接强度(抗拉强度≥350MPa)及整体装配精度,确保在极端负载下不发生结构性失效。
2. 材料耐久性测试
采用盐雾试验箱模拟5年周期腐蚀环境,验证装置金属部件的耐腐蚀等级(需达到ASTM B117-19标准9级);通过-40℃~120℃高低温交变试验,检测高分子材料部件的抗老化性能,观察是否出现龟裂、脆化等劣化现象。
3. 安装适配性验证
依据JT/T 1176-2018规范,使用轮毂定位仪测量装置与不同规格轮毂(16-22.5英寸)的匹配度,要求轴向偏差≤0.15mm。同时进行动态平衡测试,确保加装后轮毂不平衡量≤10g·cm,避免引发异常振动。
4. 应急功能实效检测
在专业测试场进行实车工况模拟,包括:
• 80km/h时速下前轮双胎同时失压测试
• 满载状态下30°斜坡侧向支撑试验
• 连续制动工况中装置抗扭转变形能力
测试后需保证车辆仍能维持直线行驶且制动距离增幅≤20%
5. 环境适应性评估
包括泥水喷射试验(验证沙尘侵入防护能力)、电磁兼容测试(确保不干扰胎压监测系统)、振动疲劳测试(模拟20万公里路谱后检查螺纹连接件松动量≤0.05mm)等复合环境适应性指标。
6. 标识与文档审查
核查产品铭牌的永久性标识是否符合GB 7258要求,包括制造商代码、适用车型、生产批次等信息;技术文档需包含完整的FMEA分析报告和第三方认证文件。
检测实施的技术路径
现代检测体系采用"实验室标准化检测+道路场景化验证"双轨模式。依托六自由度振动台、高速摄像采集系统等设备,结合大数据分析平台,建立装置性能退化模型。通过采集10万公里实载运营数据,动态修正检测阈值,确保检测结果能真实反映装置的全生命周期可靠性。
行业发展趋势与展望
随着智能网联技术的发展,新一代检测系统正融合胎压实时监测、应力分布式传感等技术,构建车联网环境下的主动预警体系。未来将通过建立云端数据库,实现对全国营运车辆应急安全装置的在线健康监测,推动检测模式从定期检修向预测性维护转型,全面提升道路运输安全水平。
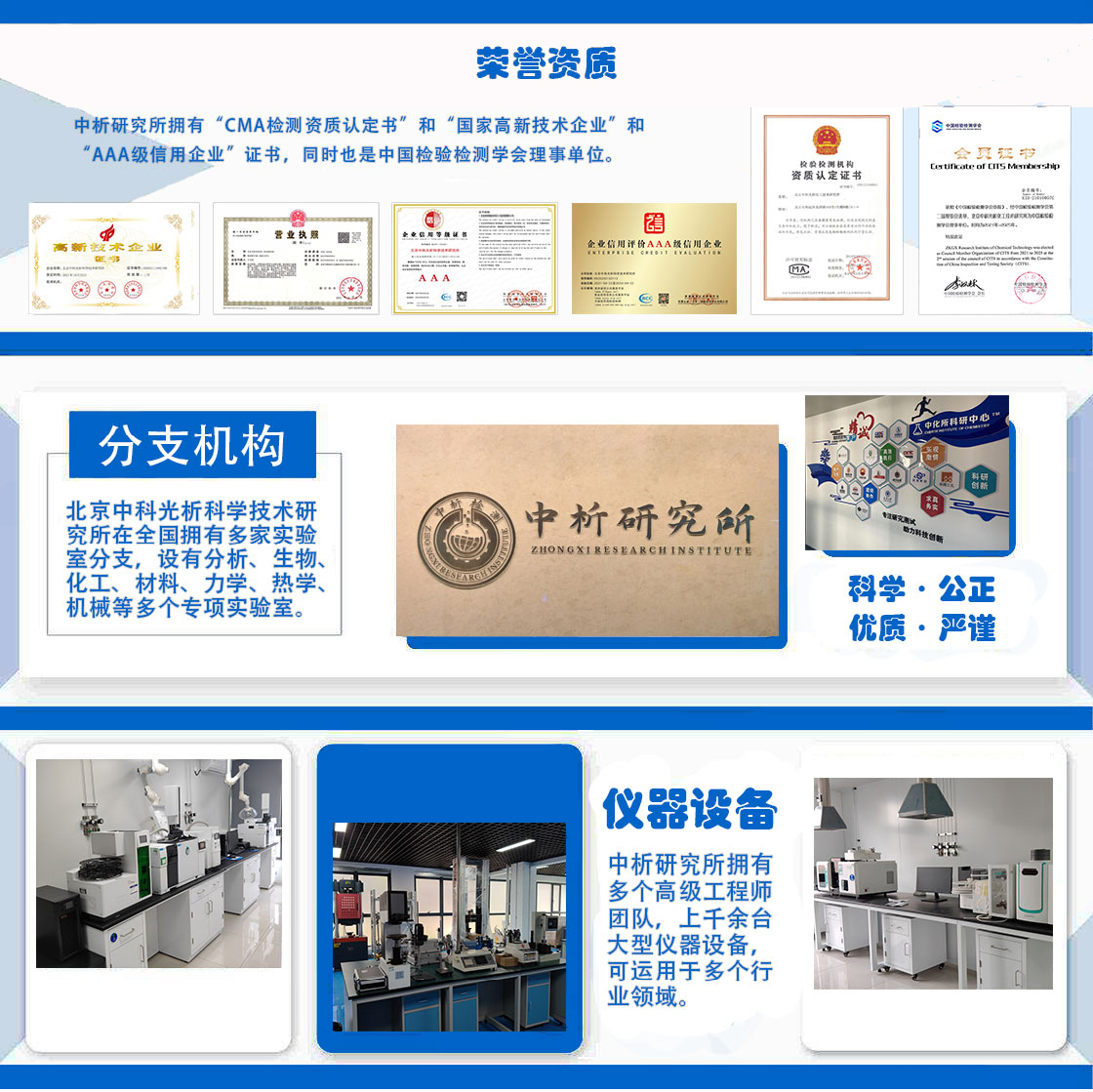
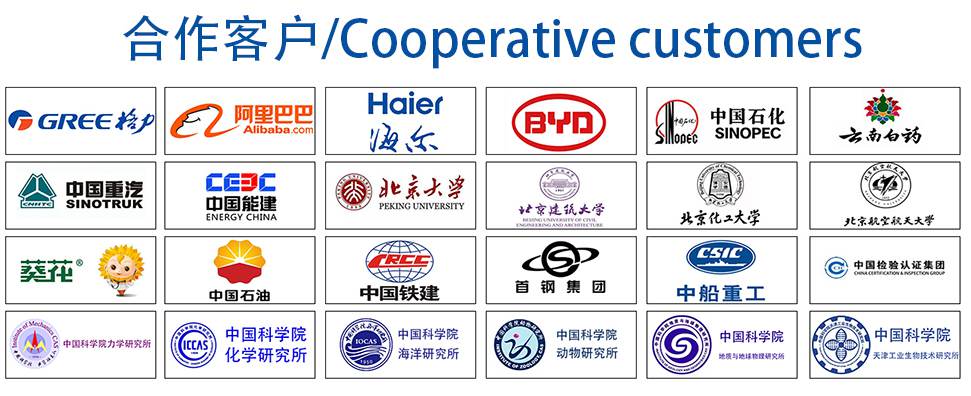