客车座椅及其车辆固定件检测的重要性
在客车安全体系中,座椅及其固定件的可靠性直接关系到乘客的生命安全。据统计,车辆碰撞事故中约30%的乘员伤害与座椅失效相关,其中固定件断裂、连接松动等问题占主要因素。通过系统的检测项目,可验证座椅结构强度、固定件抗冲击性及长期使用稳定性,确保其符合GB 13057《客车座椅系统强度要求及试验方法》等国家标准,同时满足欧盟ECE R80、美国FMVSS 207等国际法规要求。检测范围涵盖从原材料力学性能到整车动态试验的全流程,是客车生产企业和配件供应商质量控制的核心环节。
核心检测项目及技术要求
1. 座椅结构强度测试
采用万能试验机进行静态载荷测试:垂直方向施加相当于座椅自重20倍的载荷,保持5分钟无永久变形;水平方向模拟急刹车工况,施加相当于座椅自重8倍的纵向载荷。动态冲击测试通过摆锤装置模拟16g加速度冲击,要求座椅骨架无断裂、铰链机构保持正常功能。
2. 固定件耐久性检测
针对螺栓、焊接点等连接部件,执行20万次循环振动测试(频率5-500Hz,振幅±2.5mm),检测螺纹副磨损量需小于0.15mm。使用扭矩扳手测量固定件预紧力衰减值,要求5次拆卸重装后保持初始扭矩的85%以上。盐雾试验模拟沿海环境,按GB/T 10125标准进行720小时测试,表面腐蚀面积不得超过5%。
3. 阻燃性能评估
依据GB 8410《汽车内饰材料燃烧特性技术要求》,采用水平燃烧法检测座椅面料:燃烧速度≤100mm/min,续燃时间≤30秒。对发泡填充物进行氧指数测试,要求OI值≥28%。高温环境下(85℃±2℃)进行7天老化试验后,材料抗拉强度保留率应≥80%。
4. 人体工学安全测试
使用三维动态捕捉系统评估头枕吸能性能:当模拟假人头部以24km/h速度撞击头枕时,HIC(头部伤害指数)应≤500。安全带固定点强度测试需承受15kN静载力,位移量≤125mm。座椅翻转机构需通过30°斜坡驻车试验,确保紧急情况下座椅保持有效约束功能。
5. 环境适应性验证
在-40℃至85℃温度循环箱中进行热冲击试验,完成10个循环后检查塑胶件脆化情况。湿度测试(95%RH,40℃)持续500小时,金属部件不得出现可见锈蚀。针对寒区运营车辆,额外增加-50℃低温存储试验,验证材料冷脆特性。
检测技术发展趋势
随着智能网联技术的发展,检测体系正向数字化方向演进:采用有限元分析预判结构弱点,结合六维力传感器实时监测动态载荷分布。部分实验室已引入自动驾驶碰撞模拟平台,可复现128种典型事故场景。2023年新实施的ISO 22239标准更将电动车电池安全纳入联动检测范围,要求座椅固定件具备防高压电击隔离设计。
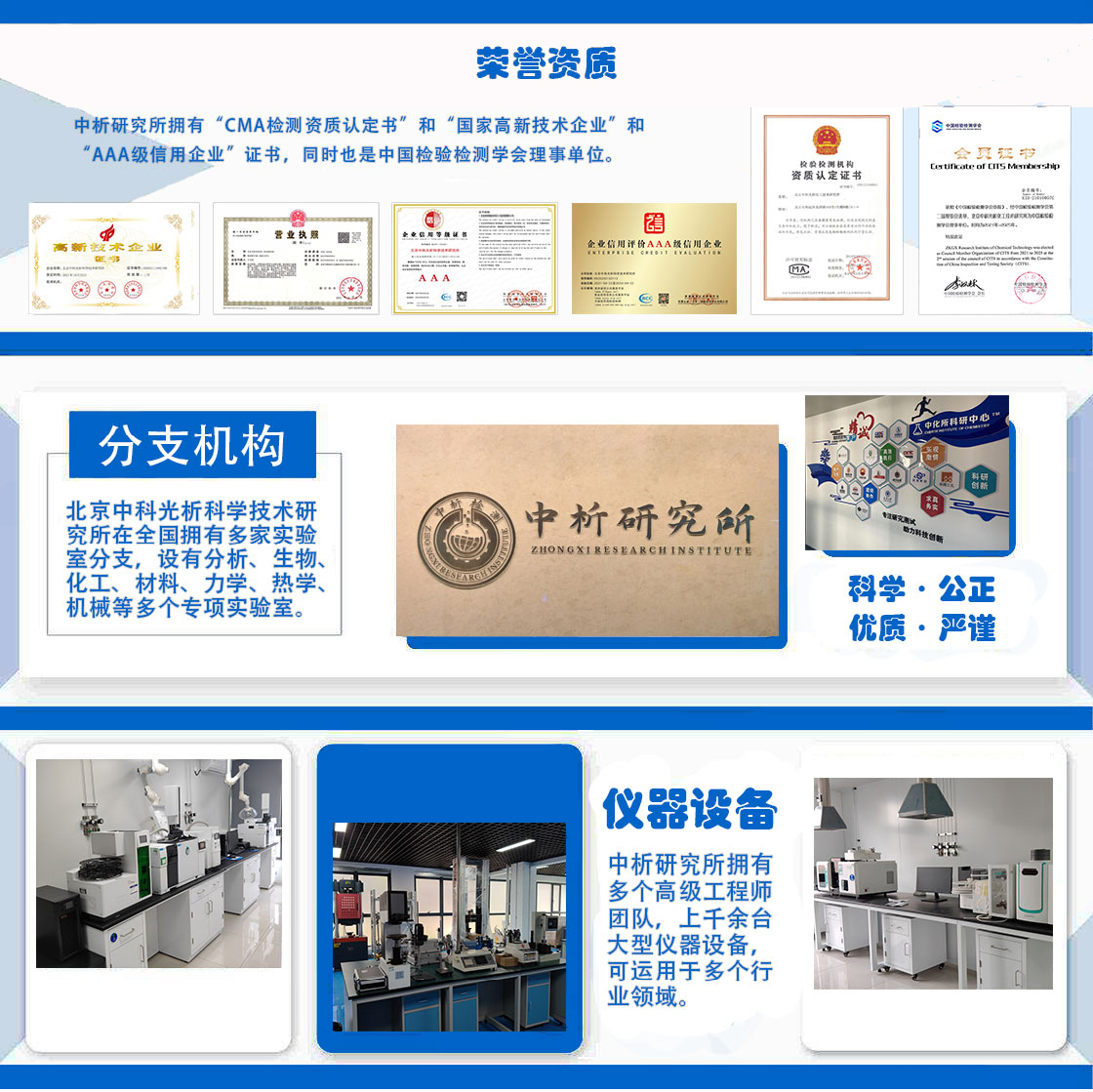
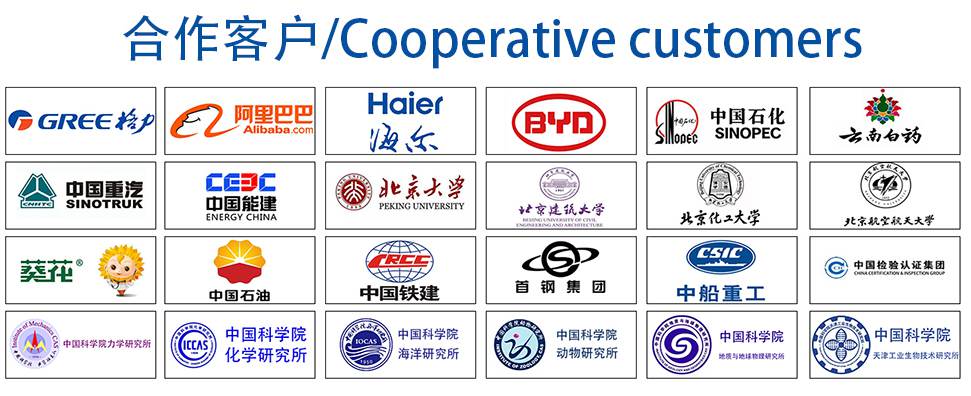