自卸汽车液压系统检测的重要性与核心项目
自卸汽车作为工程运输领域的关键装备,其液压系统承担着货箱升降、倾斜等核心功能,直接影响作业效率与安全性。系统长期处于高负荷、频繁启停和复杂工况下,油液污染、密封失效、元件磨损等问题极易导致升降迟缓、举升无力甚至突发性故障。定期开展液压系统检测,既是预防设备失效的必要措施,也是降低维修成本、延长核心部件寿命的重要手段。通过科学检测可精准定位隐患,避免因系统崩溃造成的停工损失。
检测项目一:液压油品质与油量检查
使用专用油液检测仪分析液压油的粘度、含水量和污染度,观察油液是否浑浊或含金属颗粒。同时核对油位是否处于标尺正常范围,油量不足会导致油温异常升高,而油液氧化则加速密封件老化。建议每500小时或季度进行一次油样实验室检测。
检测项目二:液压缸密封性与行程测试
通过升降货箱观察各油缸同步性,使用压力表测量举升时的最大工作压力。重点检查活塞杆表面是否存在划痕或锈蚀,检测防尘圈、O型圈是否漏油。对于多级油缸,需验证每级伸缩行程是否达标,防止因内泄导致的举升高度不足。
检测项目三:齿轮泵与阀组性能验证
采用流量计测试齿轮泵输出流量是否满足设计要求(通常需≥100L/min),同时监测系统空载和负载压力变化。检查多路换向阀、溢流阀的响应灵敏度,通过压力突变测试验证安全阀开启压力是否符合标定值(一般在16-20MPa范围)。
检测项目四:管路与接头完整性检测
使用内窥镜排查高压软管内部龟裂情况,借助超声波探伤仪检测金属硬管的应力裂纹。对卡套式接头进行30MPa保压测试,观察压力表是否在10分钟内下降超过2MPa。特别注意弯管部位的磨损痕迹,避免爆管风险。
检测项目五:控制系统电气联动检测
操作手柄时通过示波器检测电磁阀信号波形,验证限位开关、压力传感器的反馈精度。对PLC控制器进行故障代码读取,模拟触发过载保护功能,确保紧急下降装置能即时响应。同步检查线路绝缘电阻,防止因线路老化导致的误动作。
检测项目六:系统综合效率评估
采用功率分析仪测量液压系统总效率(正常应≥65%),记录空载循环时间和满载举升耗能。通过红外热像仪扫描系统各部件温度分布,排查异常发热点。对比检测数据与出厂参数,建立设备性能衰减趋势模型。
综合上述检测结果,可准确判断液压系统的健康状态,针对性地更换滤芯、修复密封或调整压力设定。建议建立检测档案,结合设备使用频率制定个性化维护周期。通过预防性检测,可降低30%以上的意外故障率,显著提升自卸车出勤率与作业安全性。
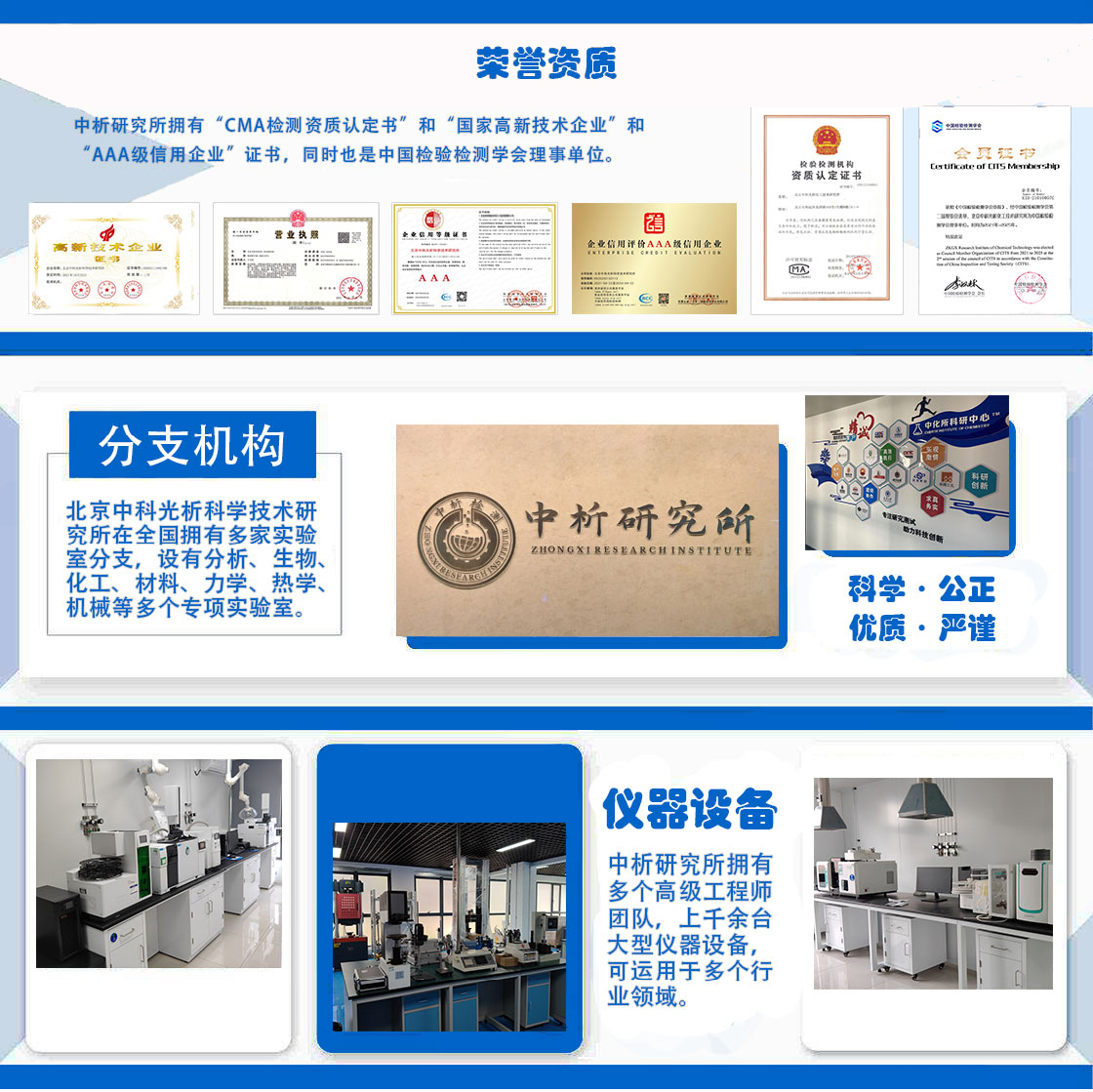
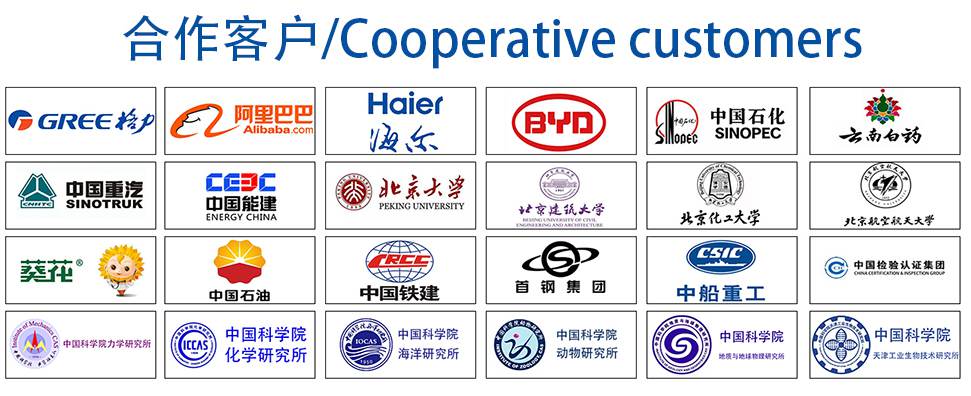