内燃机活塞环检测的重要性与核心项目
活塞环作为内燃机的核心部件之一,承担着密封燃烧室、导热、控油和支撑活塞运动的关键作用。其性能直接影响发动机的功率输出、燃油经济性及排放水平。在高温、高压、高频往复运动的极端工况下,活塞环的尺寸精度、材料强度和表面质量会逐渐劣化,甚至引发拉缸、烧机油等严重故障。因此,系统化的活塞环检测不仅是维修保养的必要环节,更是预防性维护与发动机性能优化的重要依据。
活塞环检测的核心项目与技术要求
1. 尺寸精度检测
使用千分尺、环规和投影仪等精密测量工具,重点检测活塞环的闭合间隙、端隙、背隙以及自由状态下的开口尺寸。其中闭合间隙需控制在缸径的0.3%-0.6%范围,开口间隙偏差应≤±0.02mm。三维轮廓仪可对环面弧度进行三维建模分析,确保与缸壁的贴合度>95%。
2. 弹性性能测试
通过专用弹簧试验机检测活塞环的径向弹力分布,要求单位弧度弹力均匀性误差<8%。弹性衰减率需满足行业标准:新环压缩至闭合状态后弹力损失<5%,使用后的旧环弹力下降不得超过初始值的25%。
3. 表面质量分析
采用白光干涉仪和SEM电子显微镜进行多尺度检测:宏观层面检测划痕深度(<1μm)、表面粗糙度Ra值(0.1-0.4μm);微观层面分析涂层结构完整性,DLC类金刚石涂层的厚度偏差应<0.5μm,孔隙率<0.3%。
4. 材料性能验证
使用维氏硬度计进行截面硬度测试,基体硬度需达到HV300-400,表面硬化层硬度>HV800。通过能谱分析(EDS)验证合金成分,铸铁环的碳当量应控制在3.6-4.1,钼、铬等合金元素含量偏差<±0.15%。
5. 密封性能模拟测试
在气密性试验台上模拟工作状态,测量漏气率指标:常温下≤3L/min,高温工况(200℃)允许值提升至5L/min但持续时间不得超过30秒。采用荧光渗透法检测微泄漏路径,单个泄漏点面积需<0.02mm²。
智能化检测技术的发展趋势
当前行业正在加速推进AI视觉检测系统的应用,通过深度学习算法可实现每秒200帧的高速表面缺陷识别。基于数字孪生技术的虚拟测试平台可模拟10万小时工况,预测活塞环的寿命衰减曲线。这些创新技术将检测效率提升40%以上,同时使故障预警准确率达到98%。
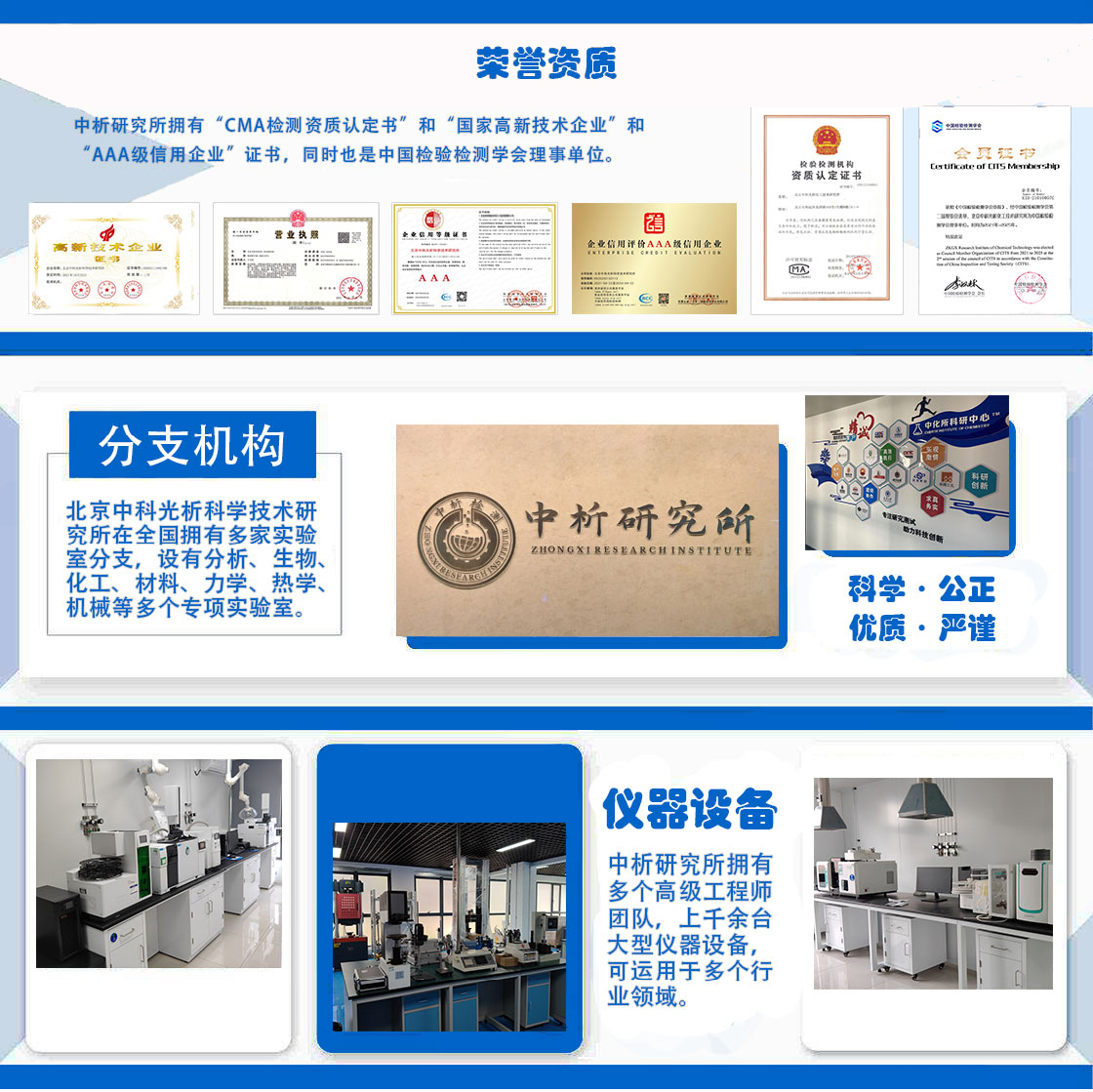
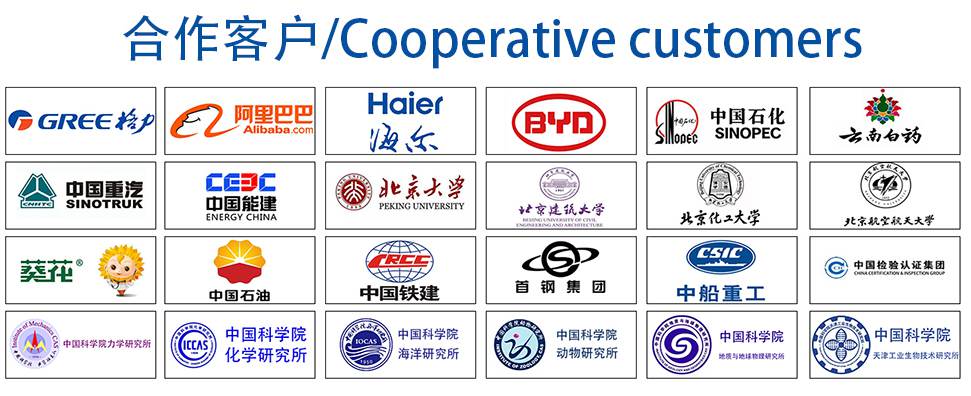