气压制动软管作为车辆制动系统中的关键部件,直接关系到行车安全与制动性能的稳定性。其主要用于连接制动气室与制动阀,承受高压压缩气体的传输,在频繁的动态变形和复杂工况下易出现老化、裂纹、膨胀等问题。因此,针对气压制动软管的检测是商用车、工程机械等领域质量管控的核心环节。依据GB/T 7127《汽车液压制动系统用制动软管组件》、ISO 3996等标准要求,检测项目需覆盖物理性能、化学性能及耐久性三大维度,以确保其符合耐压性、密封性及抗环境侵蚀能力。
一、外观与尺寸检测
通过目视检查和精密测量工具,确认软管表面是否存在划痕、气泡、局部变形等缺陷,同时测量内径、外径、长度等参数是否符合设计公差。标准规定软管外层橡胶应无分层、龟裂,编织层或缠绕层均匀无松散,接头部位无锈蚀或变形。
二、耐压性能测试
在液压试验机上模拟实际工况,进行静压试验与脉冲试验。静压试验要求软管在1.5倍工作压力下保持2分钟无渗漏或膨胀异常;脉冲试验需完成20万次压力循环(通常为0~工作压力的交变载荷),试验后软管体积膨胀率需≤3%,且无破裂或接头脱落。
三、高温与低温耐受性检测
将软管置于120℃高温箱中72小时,再在-40℃低温环境中放置24小时,观察橡胶层是否硬化、脆裂或出现裂纹。试验后需通过耐压复测,验证其性能衰减是否在允许范围内。
四、屈挠疲劳试验
通过动态屈挠试验机模拟车辆行驶中的弯曲振动,以规定频率(通常5Hz)和角度对软管进行10万次循环测试。试验后软管应无泄漏、外层剥落或结构分离,弯曲部位不得出现明显磨损或变形。
五、耐臭氧老化测试
将软管置于臭氧浓度50pphm、温度40℃的环境中72小时,观察表面是否产生龟裂。该试验重点验证橡胶配方的抗臭氧老化能力,防止长期户外使用中因臭氧侵蚀导致性能劣化。
六、爆破压力检测
通过逐步加压直至软管爆破,记录最大爆破压力值。根据标准要求,爆破压力需≥4倍额定工作压力,且破坏形式应为纵向开裂而非接头脱落,以验证其安全余量是否达标。
综合上述检测项目可全面评估气压制动软管的可靠性与使用寿命。企业需建立定期抽样检测机制,并结合实际使用环境优化材料配方与生产工艺,从而保障车辆制动系统的长效安全运行。
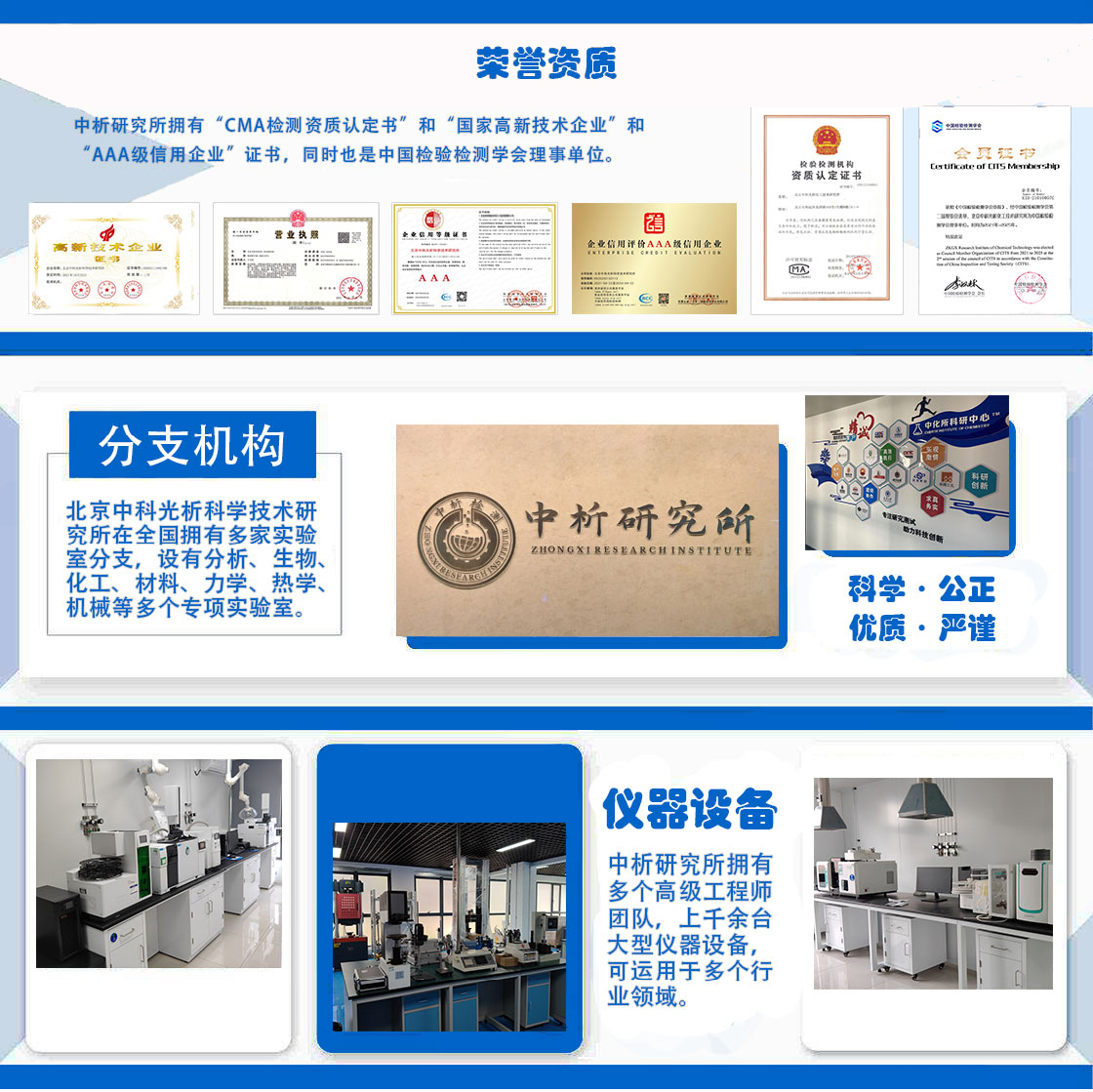
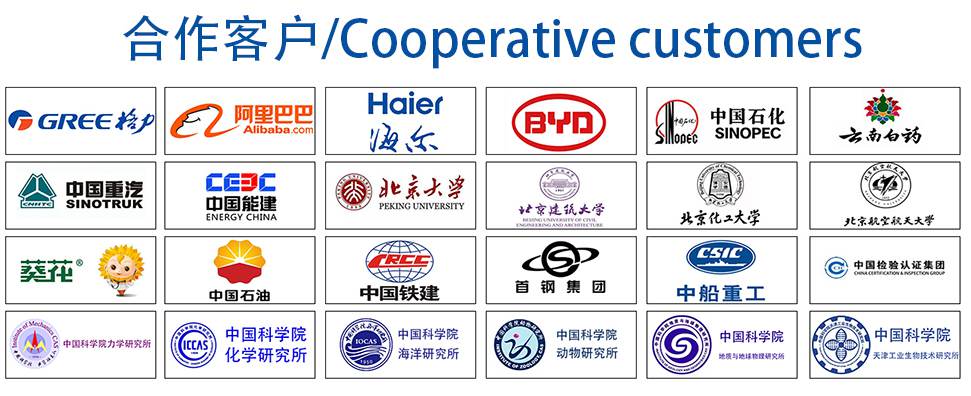