隔爆型接线盒检测的重要性与应用场景
隔爆型接线盒作为爆炸性环境中电气设备的核心安全组件,广泛应用于石油、化工、煤矿、天然气等易燃易爆危险场所。其核心功能是通过特殊结构设计,将内部可能产生的电火花或高温限制在密闭壳体内部,防止外部爆炸性气体被引燃。由于使用环境的特殊性,隔爆型接线盒的检测直接关系到生产安全与人员生命保障。为确保其性能符合国家标准(如GB 3836.1-2021)和国际标准(如IEC 60079系列),需通过系统化的检测项目验证其结构完整性、密封性及电气安全性。
隔爆型接线盒核心检测项目
1. 结构完整性检测
重点检查外壳材质、厚度及加工精度,确保能承受内部爆炸压力。通过目视检查、量具测量及压力测试验证,例如对隔爆接合面间隙(≤0.15mm)和长度(需符合防爆等级要求)进行精密测量。
2. 防护等级(IP)测试
依据GB/T 4208标准,进行防尘防水测试:IP54及以上等级需验证外壳对尘埃和喷水的防护能力,确保内部元件在恶劣环境下正常运行。
3. 隔爆性能试验
通过静态超压试验(1.5倍参考压力)和动态爆炸试验,模拟内部可燃气体爆炸场景,检测外壳是否发生永久性变形或破裂,并验证火焰传播阻断能力。
4. 电气参数检测
包括绝缘电阻测试(≥500MΩ)、耐压试验(2U+1000V,1分钟无击穿)及接地连续性检验(接地电阻≤0.1Ω),确保电气安全性能达标。
5. 材料阻燃性测试
对外壳非金属部件进行灼热丝试验(850℃条件下无明火燃烧)和耐电弧测试,防止材料引发二次燃烧。
6. 机械强度验证
对电缆引入装置进行拉力测试(施加20倍电缆重量的拉力持续6小时),并检查紧固件扭矩值(按标准力矩的±10%验收),确保长期使用稳定性。
7. 环境适应性试验
通过高低温循环(-20℃~+60℃)、湿热交变(湿度95%RH)及盐雾腐蚀(5%NaCl溶液,连续喷雾96小时)等测试,验证产品在极端环境下的可靠性。
检测流程与质量控制要点
检测需贯穿产品全生命周期:出厂前进行型式试验,安装时核查防爆标志与认证一致性(如Ex d IIB T4 Gb),运行中定期进行密封件老化检查(建议周期≤3年)。同时需建立检测数据档案,对隔爆面粗糙度(Ra≤6.3μm)、螺纹啮合扣数(≥5扣)等关键参数实施动态监控。
结语
隔爆型接线盒的检测是保障防爆设备安全运行的最后防线。通过科学严谨的检测体系和数字化的质量追溯机制,可最大限度降低爆炸风险,为高危行业筑起坚实的安全屏障。
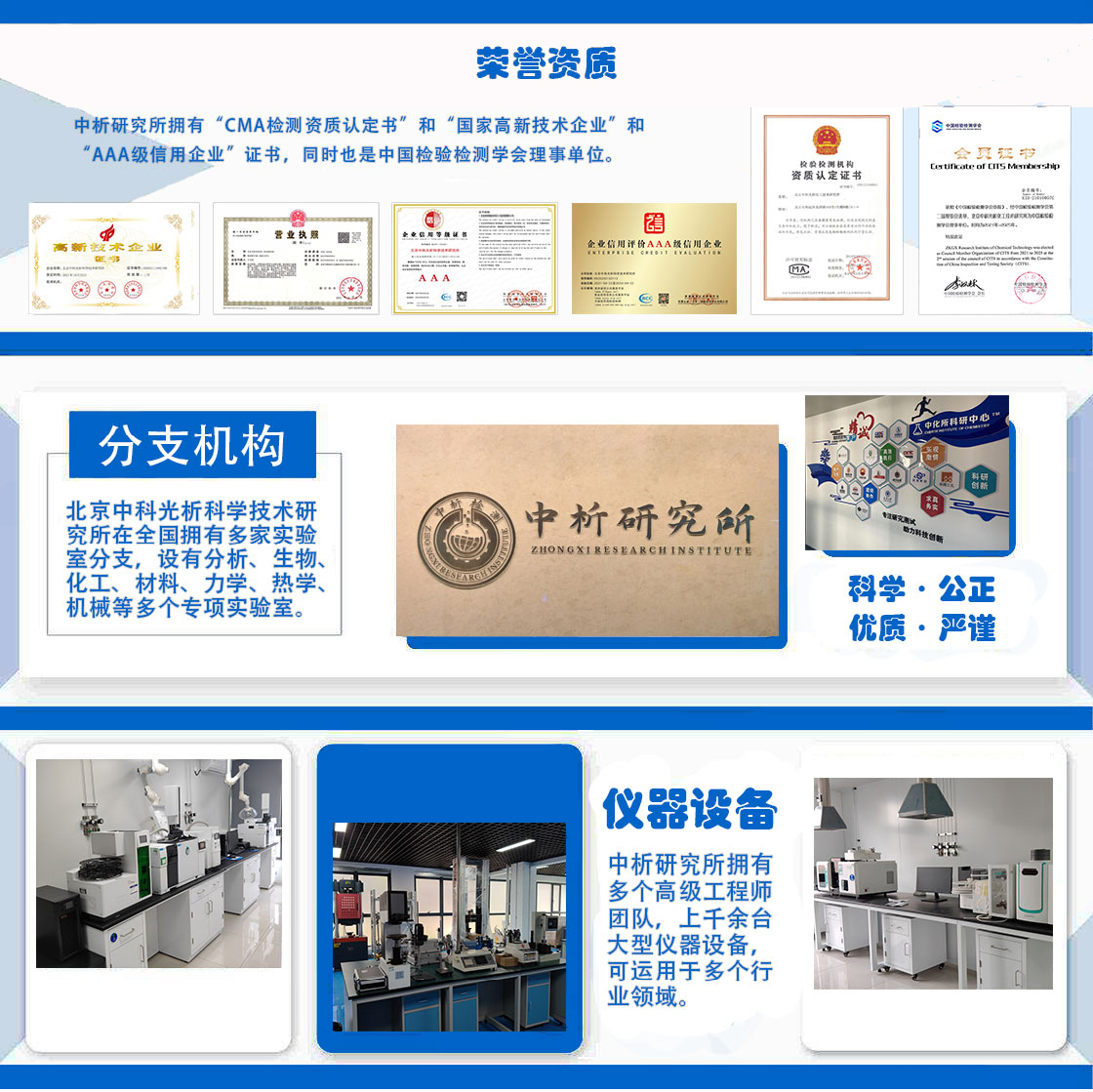
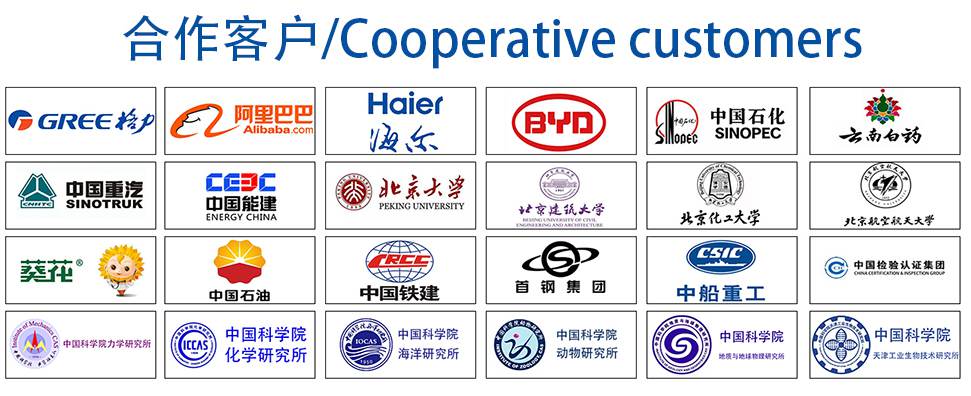