不锈钢焊接检测的重要性及主要检测项目
不锈钢因其优异的耐腐蚀性、高温强度和美观性,广泛应用于化工、食品加工、医疗设备及建筑领域。焊接作为不锈钢加工的核心工艺之一,其质量直接关系到产品的安全性、寿命和功能性。然而,焊接过程中易出现气孔、裂纹、未熔合、变形等缺陷,需要通过系统化的检测手段进行质量控制。不锈钢焊接检测需结合材料特性、工艺参数及使用环境,综合运用多种技术方法,确保焊缝满足强度、密封性和耐腐蚀性要求。
1. 焊缝外观检测
作为基础检测项目,外观检测通过目视或放大镜观察焊缝表面是否存在咬边、凹陷、飞溅、裂纹等缺陷。依据ISO 5817标准,需检查焊缝余高、宽度及均匀性,确认无氧化变色(需符合特定不锈钢耐温要求)。对于薄板焊接件,还需重点评估变形量。
2. 无损检测(NDT)
无损检测技术在不破坏焊缝的前提下精准定位内部缺陷:
射线检测(RT):通过X射线或γ射线获取焊缝内部影像,可检测气孔、夹渣等体积型缺陷,符合ASTM E94标准;
超声波检测(UT):利用高频声波反射原理定位裂纹、未熔合等面状缺陷,适用于厚板检测;
渗透检测(PT):通过显色剂凸显表面开口缺陷,适用于奥氏体不锈钢表面微裂纹检测;
磁粉检测(MT):仅适用于马氏体不锈钢焊缝的表面及近表面缺陷排查。
3. 力学性能测试
通过破坏性试验评估焊缝力学指标:
• 拉伸试验:测定焊缝抗拉强度及断裂位置(母材/焊缝)
• 弯曲试验:评估焊缝塑性变形能力和结合强度
• 冲击试验:检测低温环境下焊缝韧性
• 硬度测试:对比焊缝/热影响区/母材硬度差异,判断热处理效果
4. 化学成分分析
使用光谱仪(OES)或EDX能谱分析检测焊缝金属成分,重点控制铬当量(Creq)和镍当量(Nieq),防止σ相析出导致耐蚀性下降。对于双相不锈钢,需确保铁素体/奥氏体相比例符合要求(通常40-60%)。
5. 腐蚀试验
针对使用环境选择检测方法:
• 盐雾试验(ASTM B117):评估海洋环境下的耐点蚀能力
• 晶间腐蚀试验(ASTM A262):通过草酸侵蚀法检测敏化现象
• 电化学测试:测定点蚀电位(Epit)和再钝化电位
6. 金相分析
采用显微组织观察(100-1000倍)评估:
- 焊缝区柱状晶生长形态
- 热影响区晶粒尺寸变化
- 碳化物析出情况
- δ铁素体含量(对奥氏体不锈钢尤为关键)
7. 密封性检测
对于压力容器或管道系统,需进行:
• 气密性试验:注入压缩空气检测泄漏
• 水压试验:1.25-1.5倍工作压力保压测试
• 氦质谱检漏:检测微米级泄漏通道
结论
不锈钢焊接检测需建立从宏观到微观、从表面到内部的全方位质量评价体系。应根据具体材质(304、316L、双相钢等)、焊接工艺(TIG、激光焊等)及使用工况,制定分级的检测方案。通过多维度数据交叉验证,可有效预防焊接缺陷导致的设备失效风险,保障不锈钢焊接结构的长期可靠性。
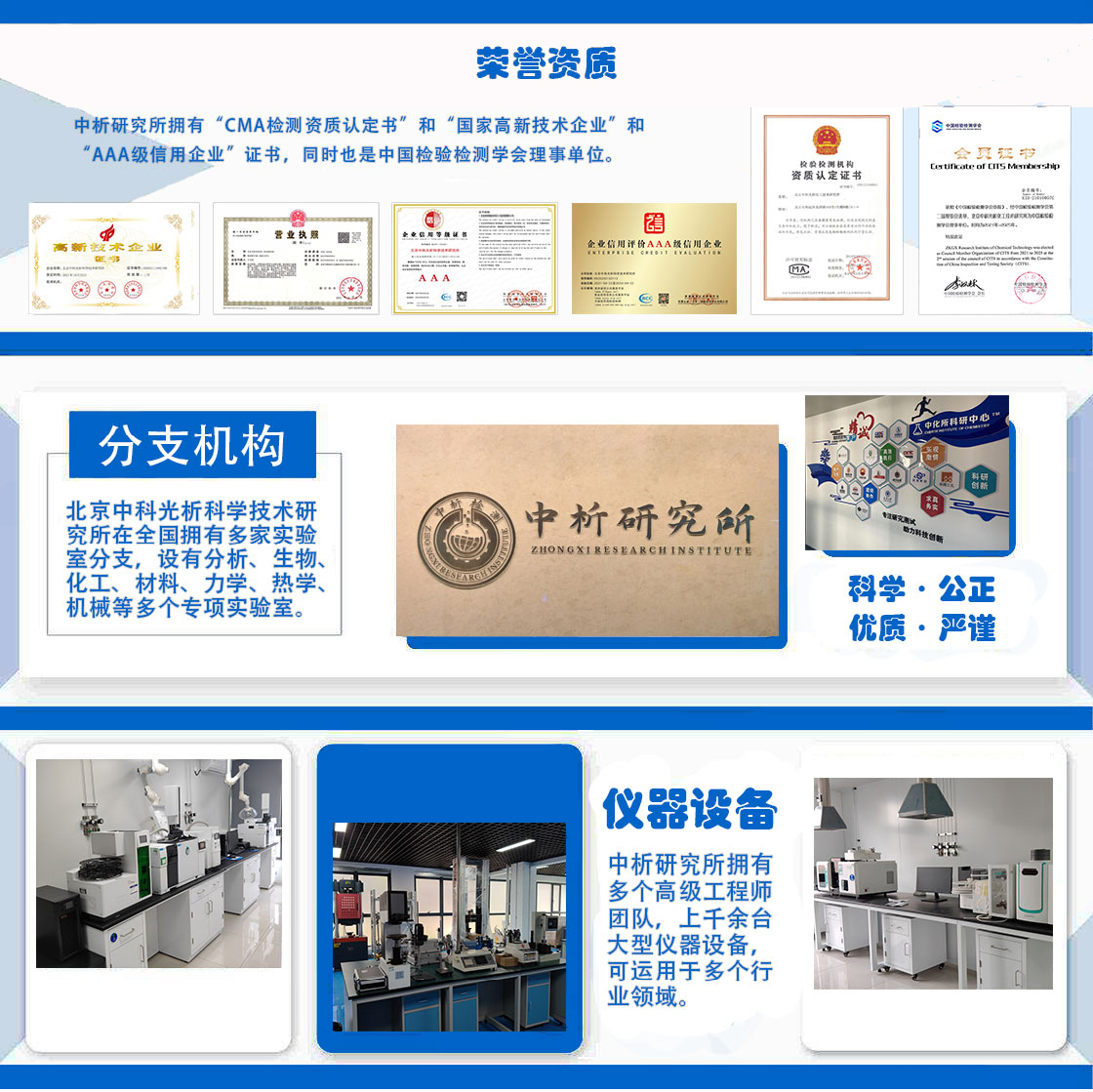
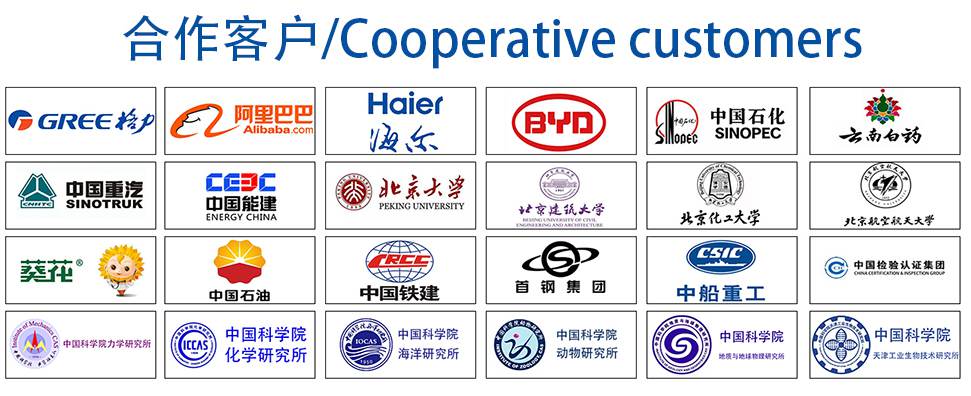