煤矿重要用途在用钢丝绳检测的重要性
煤矿生产中,提升机、运输机等设备使用的钢丝绳是保障矿井安全运行的核心部件。其长期承受高强度载荷、恶劣环境(如潮湿、腐蚀性气体)以及动态疲劳作用,易出现断丝、磨损、锈蚀等隐患。一旦钢丝绳失效,可能引发断绳坠罐、物料坠落等重大事故,直接威胁人员生命安全和矿井正常生产。因此,对煤矿重要用途在用钢丝绳开展系统性检测,既是国家《煤矿安全规程》的强制要求,也是企业落实安全生产主体责任的关键环节。
核心检测项目及技术要求
1. 外观与结构检查
采用目视、放大镜及卡尺对钢丝绳表面进行全长度检查,重点记录断丝数量(单捻距内断丝不得超过总丝数10%)、磨损量(直径减小率需≤10%)、锈蚀程度(锈蚀面积占比分级评定)及变形(如笼状畸变、绳股挤出)情况。检测需覆盖绳端固定装置和连接部位。
2. 直径测量与捻距分析
使用专用绳径卡规在无张力状态下分段测量,对比公称直径计算实际缩减率。同时测量捻距长度(相邻股峰间距),若偏差超过原始值±5%,则表明结构稳定性下降。检测数据需绘制趋势图以评估劣化速度。
3. 内部损伤无损检测
应用磁记忆检测(MMT)或漏磁检测(LF)技术,通过磁场变化识别内部断丝、锈坑及金属截面积损失。对于多层股钢丝绳,需采用旋转式探头确保100%覆盖率。检测系统应满足MT/T970标准要求,缺陷信号需经专业软件解析并生成三维损伤图谱。
4. 力学性能测试
截取代表性绳段进行破断拉力试验(保留系数应≥1.2倍最大静载荷),同步测试弯曲疲劳寿命。对于已使用2年以上的钢丝绳,还需通过金相分析评估材料晶界腐蚀情况,确保抗拉强度保留率≥90%。
5. 润滑状态评估
检测周期与结果处理
根据《煤矿安全规程》第413条规定,提升钢丝绳必须每日由专职人员检查1次,每月进行1次全面检测,新投用或经大修的钢丝绳需在初始24小时内完成首次张力测试。检测发现单捻距断丝数超标、直径减小率>10%或剩余强度系数<5.0时,必须立即停止使用并更换。所有检测数据应录入智能化管理系统,实现寿命预测与预防性维护决策。
技术发展动态
当前行业正推进基于物联网的在线监测系统应用,通过集成光纤传感、声发射检测等技术,实现钢丝绳应力分布、损伤演化的实时监控。同时,人工智能算法开始用于缺陷模式识别,检测准确率可达98%以上,大幅提升了安全隐患的早期预警能力。
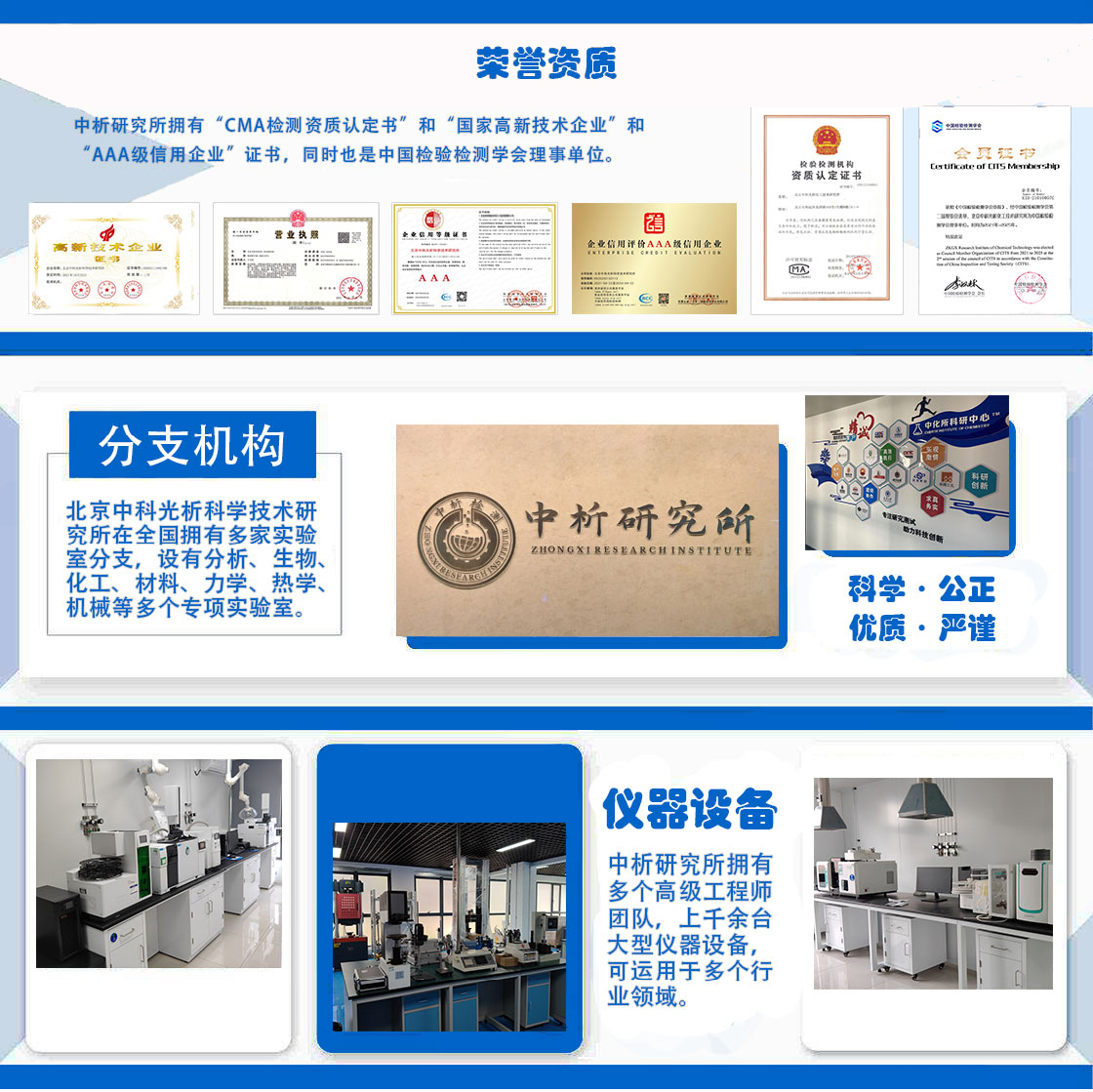
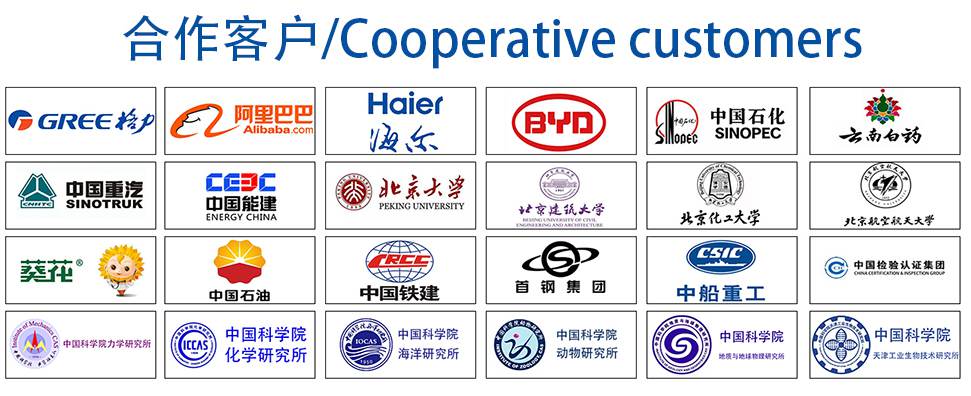