轮胎式装载机检测的重要性与核心内容
轮胎式装载机作为工程建设、矿山开采和物流运输领域的关键设备,其性能与安全性直接影响作业效率及人员安全。随着设备使用年限的增加或高强度作业的持续,机械故障风险显著上升,因此定期开展系统性检测尤为必要。通过对动力系统、传动装置、液压部件及安全防护装置的全面检查,可有效预防突发故障、延长设备寿命,并满足国家相关安全技术规范要求。科学的检测流程还能为企业节约维修成本,保障生产连续性。
主要检测项目及技术要求
1. 动力系统检测
重点检查发动机运行参数,包括怠速稳定性、最高转速、燃油消耗率及排放指标。需通过专业仪器测量气缸压力、机油油压和冷却系统效能,同时排查异响、漏油和冒黑烟等异常现象。
2. 传动系统检验
对变速箱、变矩器和传动轴进行振动分析及温度监测,验证各档位切换平顺性。检测传动齿轮磨损量是否超限,检查万向节润滑状态与密封件完整性,确保动力传递效率损失不超过额定值的15%。
3. 液压系统评估
采用压力测试仪验证工作装置液压泵输出压力是否达标,检测动臂升降、铲斗翻转的响应速度。排查液压油污染度(NAS等级)、管路泄漏点以及控制阀灵敏度,重点关注多路阀内泄和油缸爬行现象。
4. 制动性能测试
通过坡道驻车试验和动态制动距离测量,验证行车制动与驻车制动效能。检查制动摩擦片厚度(≥原厚度的1/3)、制动鼓圆度误差(≤0.15mm)及气压/液压管路密封性,确保紧急制动响应时间≤0.6秒。
5. 轮胎与行走机构检测
测量轮胎花纹深度(前轮≥3mm,后轮≥2mm),检查轮辋变形量(径向跳动≤5mm)。分析前后桥差速器的工作状态,检测轮边减速器齿轮油清洁度,并对转向机构的间隙和灵敏度进行标定。
6. 电气系统诊断
使用万用表检测蓄电池充放电性能(容量不低于标称值的80%),检验照明系统、仪表盘及传感器的功能完整性。重点排查线路绝缘电阻(≥0.5MΩ)和控制器模块的故障代码记录。
7. 安全防护装置核查
验证ROPS(防滚翻保护结构)和FOPS(防落物保护结构)的认证有效性,检查灭火器、倒车警报器、后视镜等安全附件的配置情况。测试紧急停机按钮的响应可靠性和操作手柄的防误触设计。
8. 整机性能综合测试
通过载荷试验验证额定铲装能力(±5%误差范围),测量最大牵引力与爬坡能力。记录单位油耗下的作业效率指标,结合GPS定位数据评估设备运动轨迹的稳定性。
检测周期与标准依据
新设备首次检测应在运行500小时后进行,后续常规检测间隔不超过2000小时或12个月。检测过程需严格参照GB/T 25684《土方机械安全要求》、JB/T 3698《轮胎式装载机技术条件》等标准,同时结合设备制造商提供的维护手册执行专项检查。
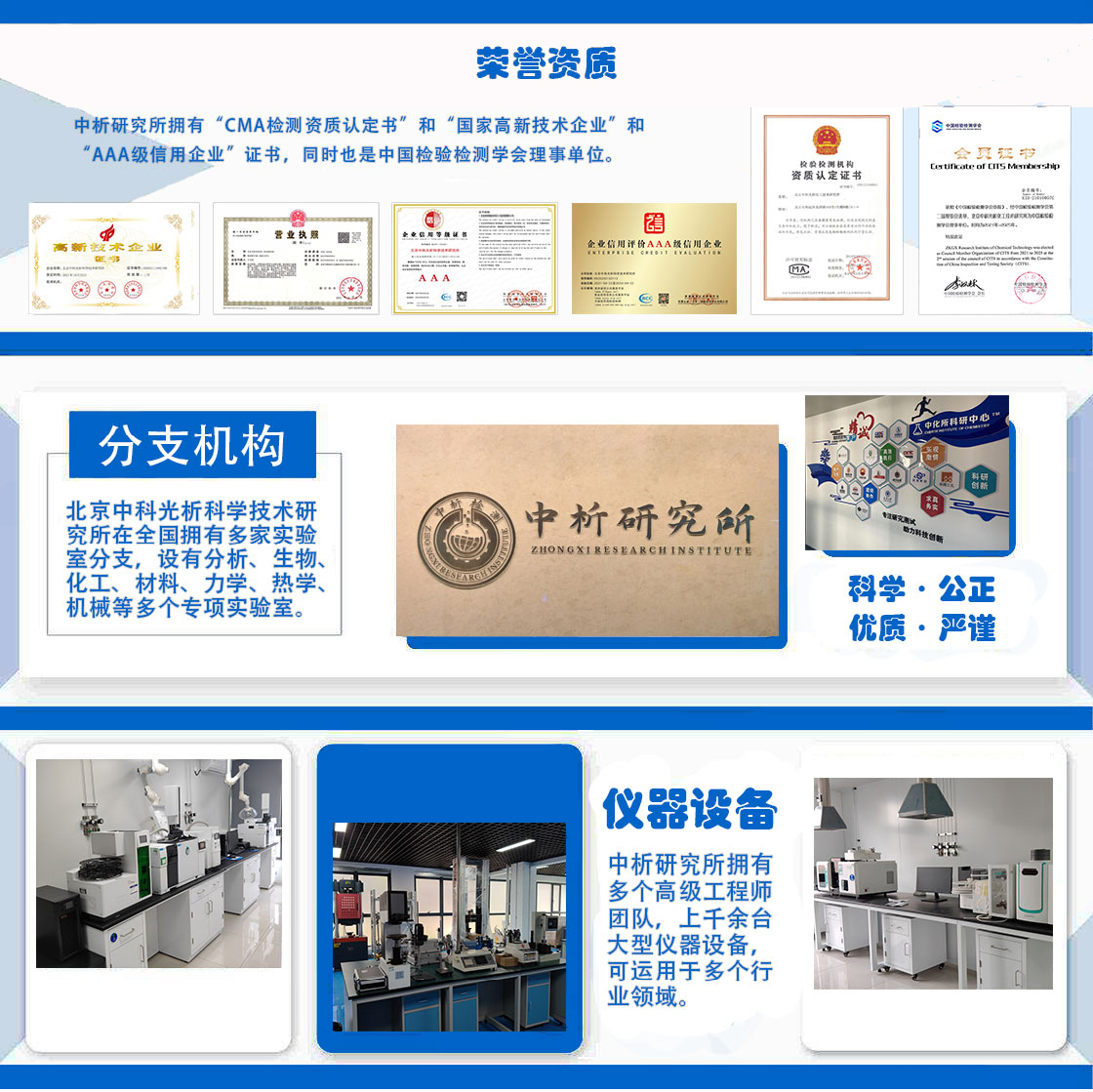
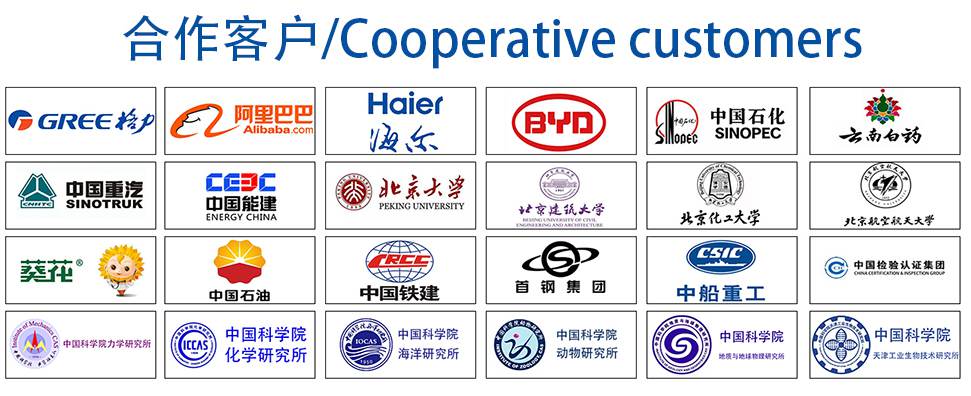