在工程机械制造领域,专用零件及金属焊接件的质量直接关系到设备的安全性、可靠性和使用寿命。由于工程机械通常需要在高温、高压、高负荷或复杂工况下运行,任何微小缺陷都可能导致设备故障甚至引发安全事故。因此,建立科学、规范的检测流程,对零件及焊接件的关键指标进行全面检验,已成为制造企业质量控制的核心环节。
一、工程机械专用零件检测项目
1. 几何尺寸与形位公差检测:使用三坐标测量机(CMM)、激光扫描仪等设备,验证零件的尺寸精度和装配配合度。重点检查轴类零件的圆柱度、齿轮的齿形误差等对机械传动性能影响显著的参数。
2. 材料性能检测:通过光谱分析仪测定材料成分,结合拉伸试验、冲击试验评估材料的强度、韧性;利用金相显微镜观察微观组织,判断热处理工艺是否符合要求。
3. 表面缺陷检测:采用磁粉探伤(MT)检测铁磁性材料表面裂纹,荧光渗透探伤(PT)适用于非金属夹杂物检测,确保零件无铸造气孔、焊接夹渣等缺陷。
4. 疲劳强度测试:通过高频疲劳试验机模拟实际工况下的交变载荷,验证零件在长期循环应力下的耐久性。
二、金属焊接件关键检测内容
1. 焊缝质量检测:使用X射线探伤(RT)或超声波探伤(UT)检查焊缝内部缺陷,如未熔合、气孔、裂纹等;通过宏观腐蚀试验评估焊缝熔深和热影响区形态。
2. 焊接残余应力测试:采用盲孔法或X射线衍射法测定焊接残余应力分布,避免因应力集中导致结构变形或开裂。
3. 硬度与耐腐蚀性检测:使用维氏硬度计测试焊缝及热影响区硬度梯度,通过盐雾试验评估焊接接头在恶劣环境中的抗腐蚀能力。
4. 焊接工艺评定:根据ISO 15614标准进行破坏性试验,验证焊接工艺参数(电流、电压、层间温度)的有效性和重复性。
三、综合检测与质量控制体系
现代化检测体系需融合数字化技术,例如通过工业CT扫描实现三维缺陷重构,或利用AI算法分析超声波探伤信号。企业应建立从原材料入库到成品出厂的闭环检测流程,同时定期进行第三方认证(如CE、API认证),确保产品符合GB/T 37400、ISO 5817等国内外标准要求。
通过系统性检测,工程机械制造企业不仅能有效规避质量风险,更能通过数据反馈优化工艺参数,提升产品竞争力。在行业向智能化、绿色化转型的背景下,检测技术的创新已成为推动产业升级的重要驱动力。
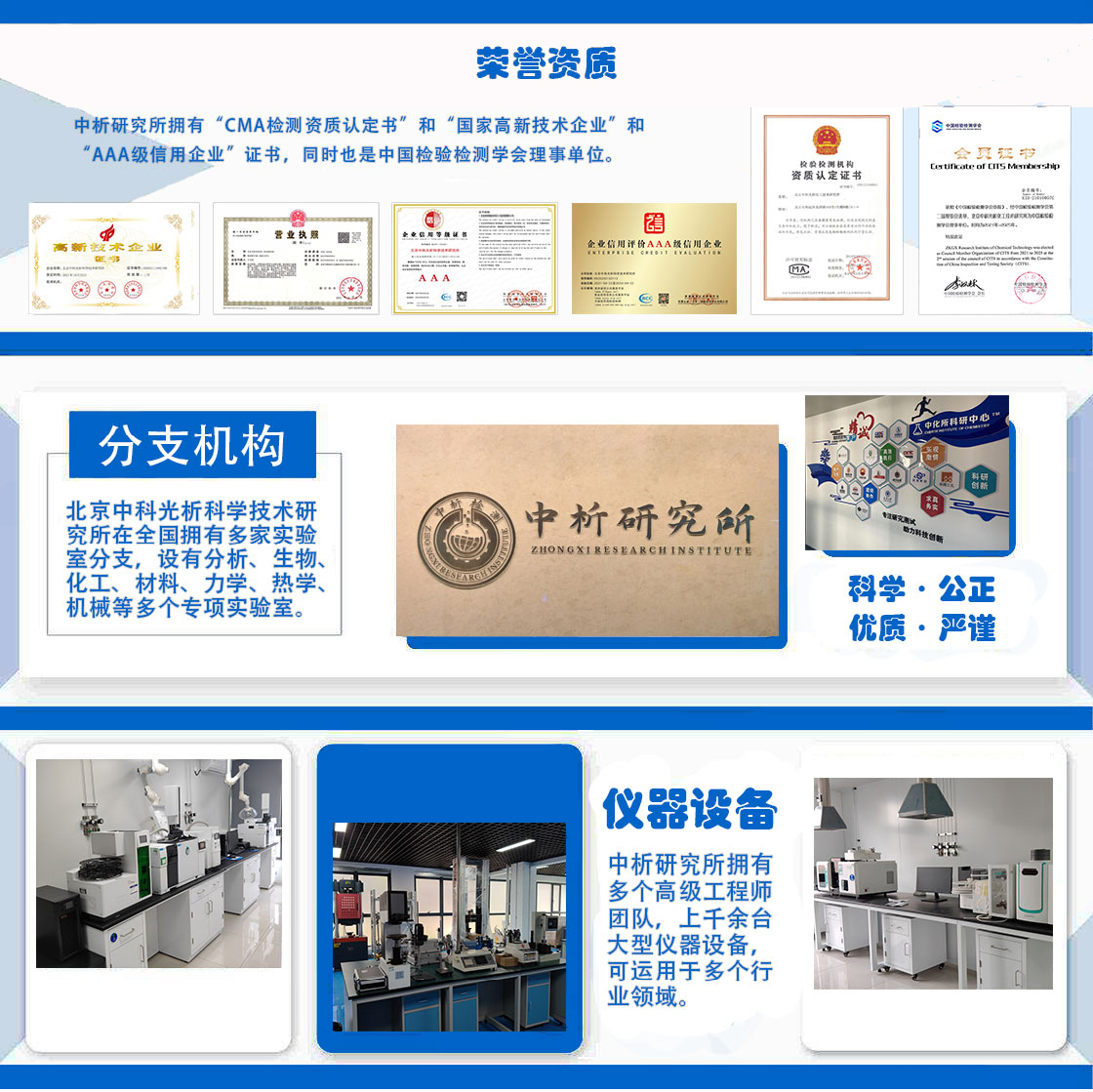
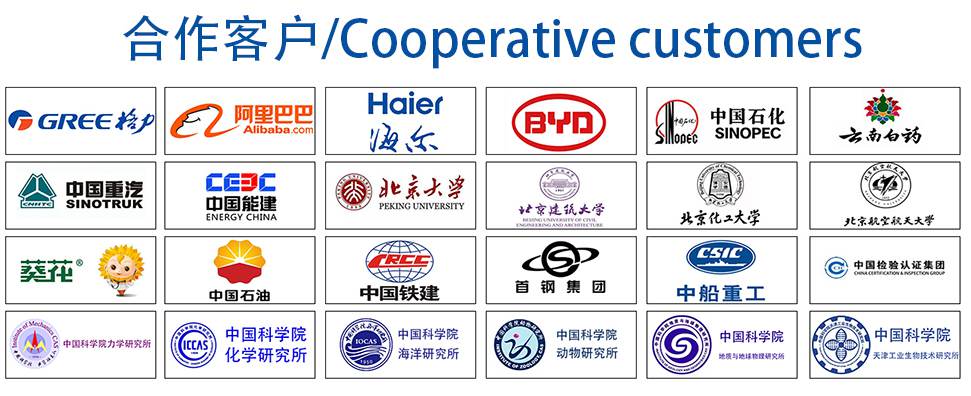