金属波纹管检测的重要性与应用领域
金属波纹管凭借其优异的柔韧性、抗压能力和密封性能,广泛应用于石油化工、航空航天、核电设备及城市供热管网等领域。作为管道系统中补偿位移、吸收振动和降低应力的关键组件,其质量直接影响设备运行的安全性与使用寿命。然而,长期处于复杂工况下的金属波纹管易因疲劳、腐蚀或加工缺陷导致失效,可能引发泄漏甚至安全事故。因此,系统化的检测项目是确保其性能达标的重要手段。
核心检测项目与技术要求
1. 外观与尺寸检测
通过目视检查、卡尺测量及三维扫描技术,验证波纹管表面是否存在裂纹、褶皱或焊接缺陷,同时检测波距、波高、壁厚等尺寸是否符合GB/T 12777标准要求。超过±5%的公差需判定为不合格产品。
2. 环刚度与抗压强度测试
使用万能材料试验机模拟轴向压缩载荷,测量波纹管在标准速率下的变形量及破坏压力值。工业级波纹管需满足≥2.5MPa的环刚度要求,核电用产品则需达到5MPa以上。
3. 疲劳寿命评估
通过高频液压脉冲试验台进行循环加载,记录波纹管在交变应力下的失效次数。根据GB/T 17888规范,常规工况产品需通过≥5000次循环,石化高温高压环境要求≥10000次。
4. 密封性能验证
采用氦质谱检漏仪或气压浸水法检测,在1.5倍工作压力下保压30分钟,泄漏率应≤1×10⁻⁸ Pa·m³/s。对于真空环境应用产品,需额外进行真空保压测试。
5. 材料成分与金相分析
通过光谱仪、金相显微镜等设备检验不锈钢(如304/316L)或高温合金的化学成分、晶粒度及热处理效果,确保材料抗腐蚀性与高温强度满足ASTM A240标准。
检测流程优化与技术创新
随着数字孪生技术的应用,新型检测方案已实现波纹管全生命周期监测。通过植入光纤传感器实时采集应力应变数据,结合有限元仿真模型预测剩余寿命,检测效率提升40%以上。建议企业建立基于AI算法的智能检测平台,实现检测数据自动分析与质量预警。
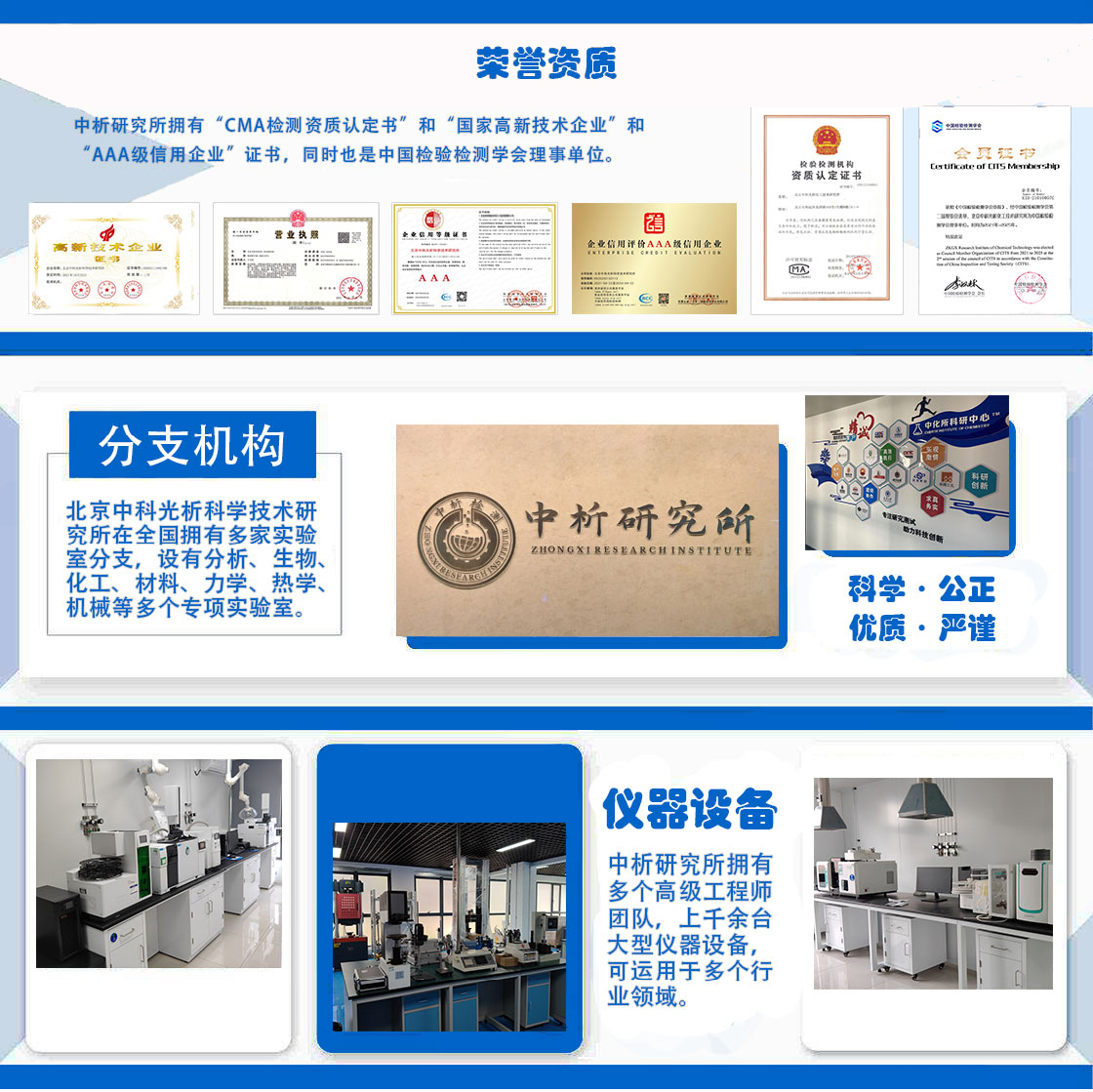
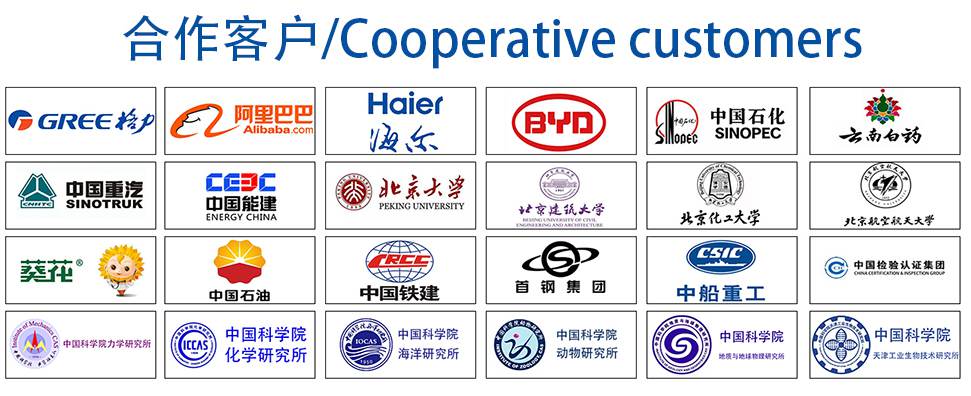