润滑剂及工业用油检测的重要性
润滑剂及工业用油是机械设备运行的“血液”,广泛应用于机械制造、汽车、航空、电力、冶金等领域。其性能直接影响设备的运行效率、寿命及安全性。随着工业技术发展,润滑油的功能已从基础润滑扩展到抗磨、冷却、防锈、密封等多重作用。然而,油品在长期使用或储存过程中可能因氧化、污染、添加剂失效等原因导致性能下降,进而引发设备磨损、能耗增加甚至故障。因此,通过科学检测手段对润滑剂及工业用油进行定期分析,是保障设备健康运行、优化维护周期和降低运营成本的关键措施。
润滑剂及工业用油核心检测项目
针对润滑剂和工业用油的检测通常涵盖理化指标、性能测试、污染物分析及使用状态评估四大类,具体包括以下关键项目:
一、基础理化指标检测
1. 粘度:作为润滑油最重要的参数之一,粘度直接影响润滑效果。检测方法包括运动粘度(GB/T 265/ISO 3104)和动力粘度(ASTM D445)。
2. 闪点:反映油品高温安全性,通过闭口杯法(GB/T 261)或开口杯法(ASTM D92)测定。
3. 酸值/碱值:表征油品氧化程度及添加剂消耗情况,常用电位滴定法(GB/T 7304)和中和法检测。
二、功能性性能测试
1. 极压抗磨性:通过四球试验机(GB/T 3142)测定最大无卡咬负荷(PB值)和烧结负荷(PD值)。
2. 抗氧化安定性:采用旋转氧弹法(ASTM D2272)评估油品抵抗氧化的能力。
3. 抗乳化性:测量油水分离速度(GB/T 7305),判断润滑油在含水环境中的稳定性。
三、污染物分析
1. 水分检测:采用卡尔费休法(GB/T 11133)或蒸馏法(ASTM D95)量化游离水和溶解水含量。
2. 颗粒物计数:利用自动颗粒计数器(ISO 4406)评估油液清洁度等级。
3. 金属元素分析:通过光谱检测(ASTM D6595)铁、铜、铝等磨损金属,辅助判断设备磨损部位。
四、使用状态评估
1. 粘度指数变化率:对比新油与在用油粘度,判断油品劣化程度。
2. 酸值增长趋势:监控氧化产物的累积速度,预测换油周期。
3. 添加剂残留量:通过红外光谱(FTIR)分析抗氧剂、极压剂等有效成分的衰减情况。
检测标准与实施规范
检测需遵循国际标准(ISO、ASTM)、国家强制标准(GB)及行业规范。例如:工业齿轮油检测依据GB 5903,液压油参照GB 11118.1,涡轮机油检测执行GB 11120。第三方实验室还需通过CMA/ 认证,确保检测数据的权威性和可比性。
结语
综合运用物理化学分析、光谱检测和性能模拟测试,可全面评估润滑剂及工业用油的品质状态。建立定期检测机制不仅能预防设备突发故障,还能通过油液分析数据优化润滑管理策略,最终实现降本增效的工业运维目标。企业应根据设备工况、油品类型和使用环境,制定针对性的检测方案并选择专业检测机构合作。
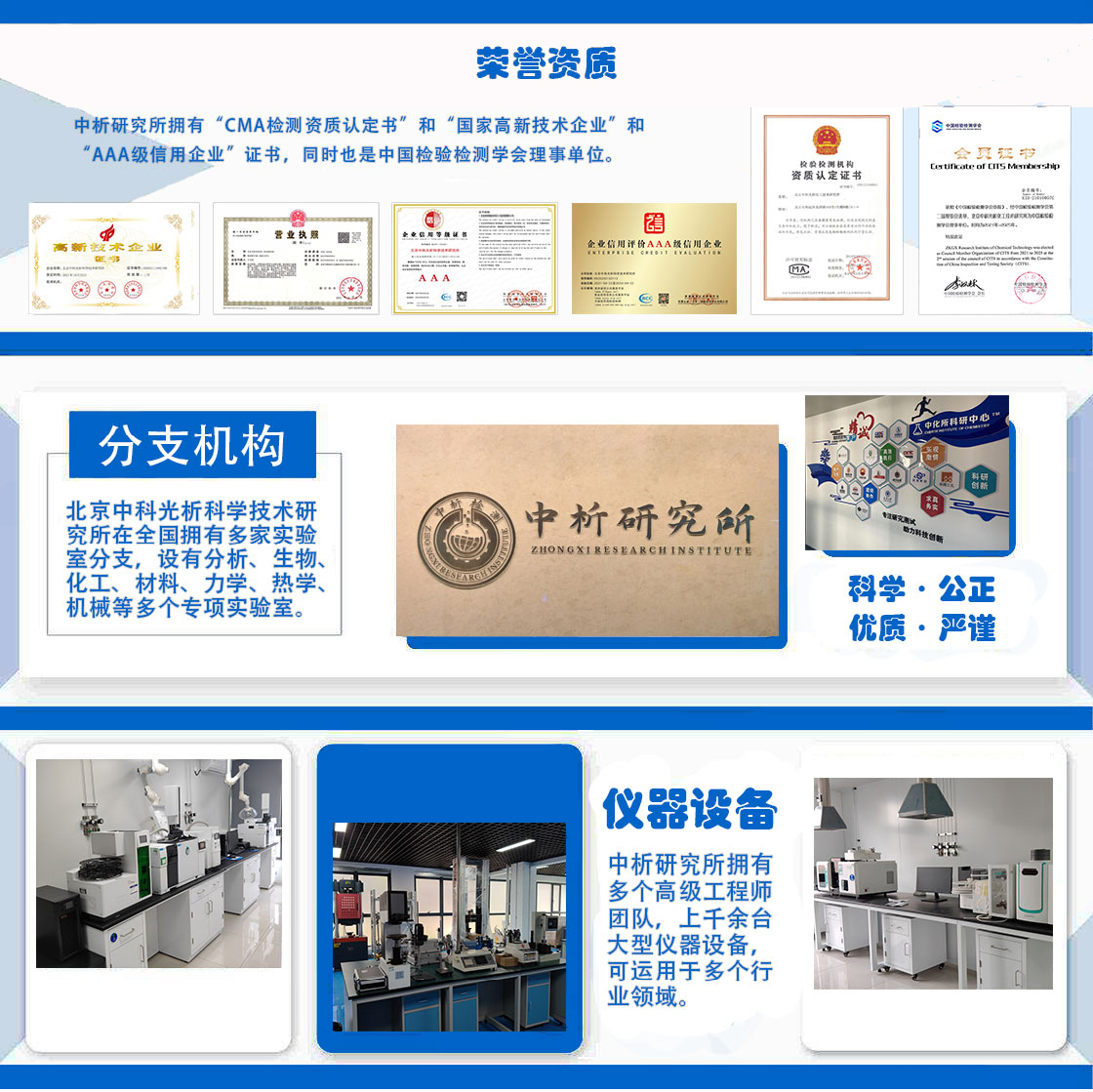
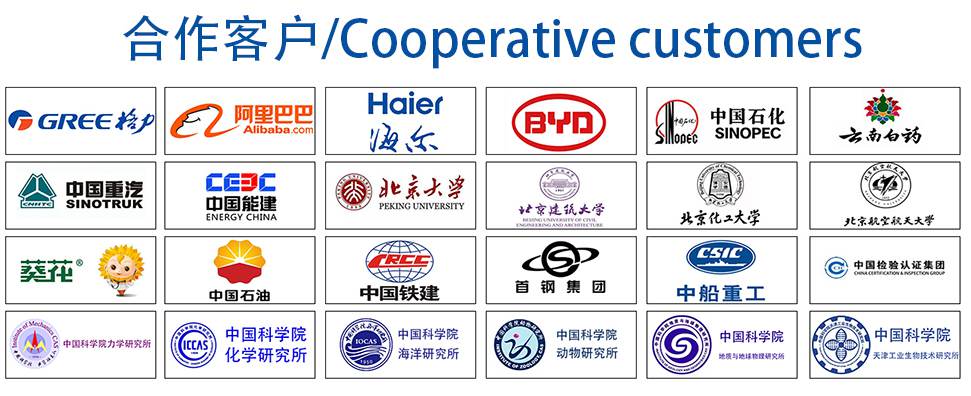