S型和C型钢制滚子链条及附件检测的重要性
在工业传动系统中,S型和C型钢制滚子链条作为动力传输的核心组件,其质量直接关系到机械设备的运行效率和安全性。随着自动化生产线和重型机械的广泛应用,链条及附件的检测已成为制造业质量控制的重要环节。根据ISO 606国际标准和GB/T 1243国家标准,这类链条需具备高强度、耐磨损、抗疲劳等特性,而附件的焊接质量、尺寸配合度等更直接影响链条的装配性能。通过科学的检测手段,可以有效预防因链条断裂、变形或附件失效引发的设备故障,同时延长传动系统寿命,降低维护成本。
核心检测项目及方法
1. 尺寸精度检测
使用三坐标测量仪和精密卡尺对链板厚度、销轴直径、滚子外径等关键尺寸进行抽样检测。重点验证内节距公差(±0.15%)、外节宽误差(不超过±1.0mm)等参数是否符合GB/T 8350规范要求,确保链条与链轮啮合的准确性。
2. 机械性能测试
通过万能材料试验机开展拉伸强度试验,检测最小抗拉载荷是否达到S型(≥22.2kN)和C型(≥31.1kN)的标称值。同时进行洛氏硬度测试(HRC 40-50范围),并利用金相显微镜观察材料晶相结构,判断热处理工艺的合格性。
3. 耐磨与耐腐蚀检测
采用链条磨损试验机模拟2000小时连续运转,测量伸长率变化(≤3%为合格)。盐雾试验箱进行72小时中性盐雾测试,评估镀锌层或达克罗涂层的防腐性能,表面锈蚀面积需控制在5%以内。
4. 附件专项检测
针对链条连接片、导板等附件,利用磁粉探伤检测焊接缺陷,X射线检测内部气孔率(≤0.5mm²)。同时使用扭矩测试仪验证连接销的装配预紧力,确保其满足设计要求±10%的公差范围。
5. 动态性能验证
在封闭式试验台上进行200rpm连续冲击试验,通过振动传感器监测链条的异常波动。红外热像仪实时监测运行温升,控制链节间温差不超过15℃,验证链条的动平衡性能。
检测技术的发展趋势
随着工业4.0的推进,机器视觉检测系统已实现链条外观缺陷的自动识别,检测效率提升300%。三维激光扫描技术可生成链条数字化模型,配合AI算法预测疲劳寿命。未来,基于物联网的在线监测系统将实现传动链条的全生命周期管理,推动检测技术向智能化、数据化方向持续发展。
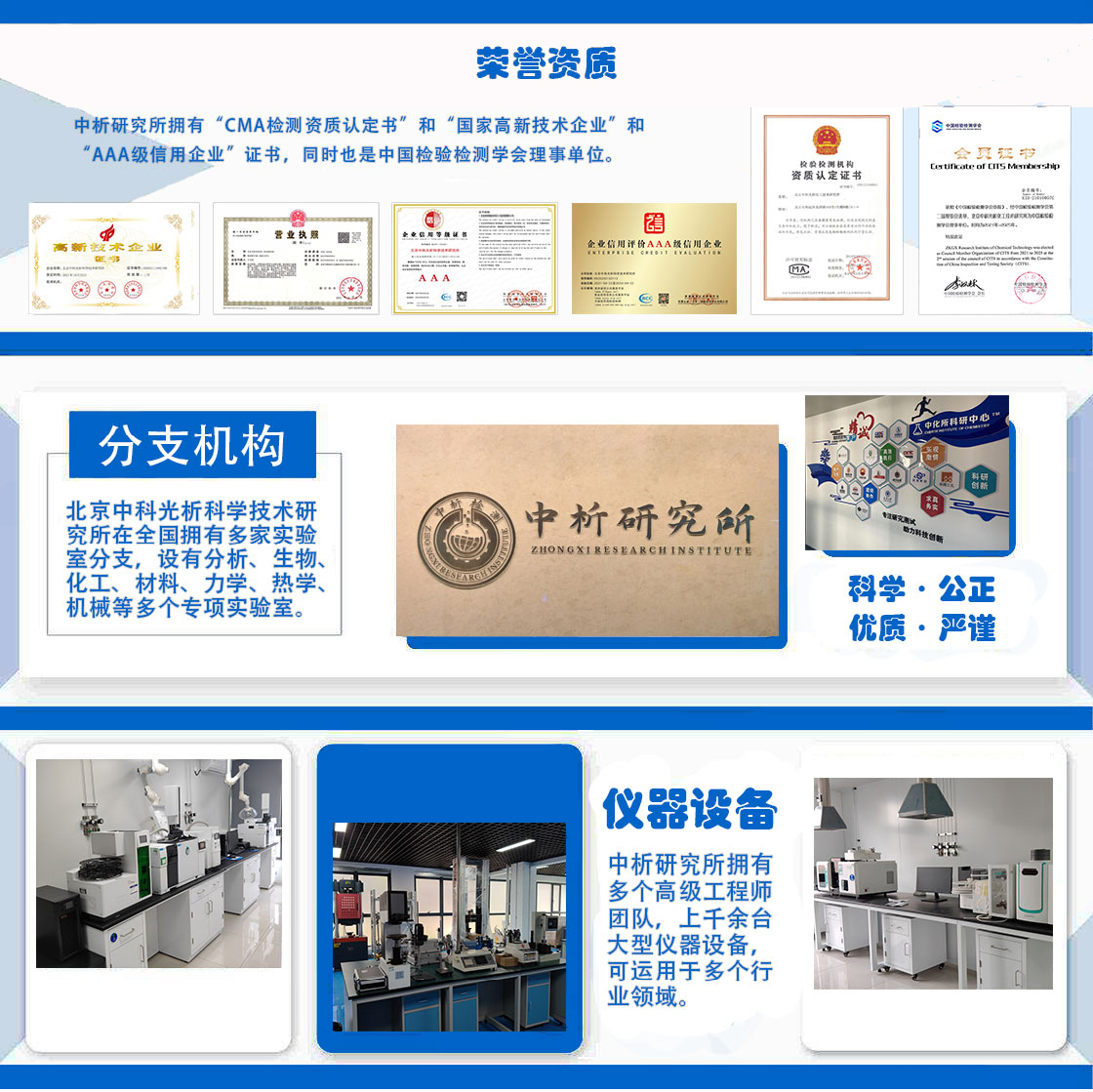
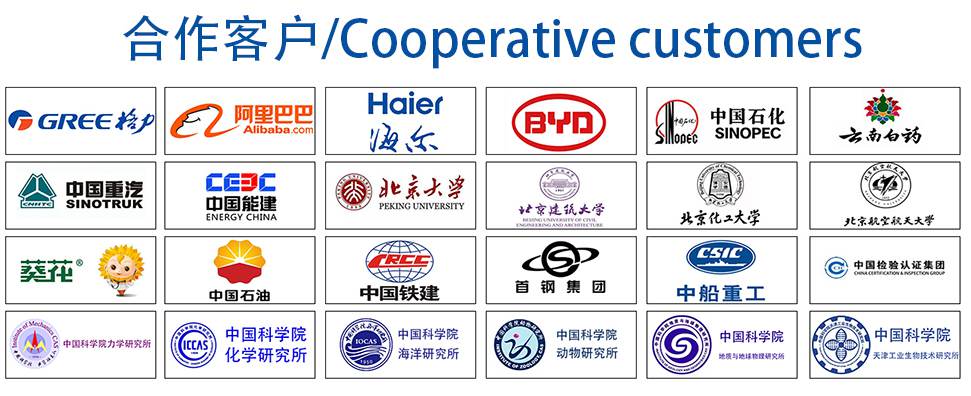