链轮参数检测的重要性及核心项目解析
链轮作为机械传动系统的核心部件,其几何精度、材料性能和动态特性直接影响传动效率和设备寿命。据行业统计数据显示,35%的链条传动故障源于链轮参数超差。在工程机械、矿山设备、自动化生产线等场景中,通过系统化的链轮检测可有效预防断齿、跳齿、异常磨损等问题,保障传动系统连续稳定运行。
关键检测项目与技术规范
1. 齿形精度检测
使用三坐标测量机或专用齿形轮廓仪,依据GB/T 1243标准对齿槽形状进行全尺寸扫描。重点检测渐开线齿形误差、齿面粗糙度(Ra≤3.2μm)及压力角偏差(±1°以内)。新型激光扫描技术可实现0.005mm级测量精度,特别适用于高速链轮的精密检测。
2. 节距累积误差检测
采用精密分度头配合电子测微仪,沿分度圆连续测量相邻齿距偏差。累积误差应控制在P×0.0025(P为链条节距)范围内。对于φ500mm以上大型链轮,推荐使用激光跟踪仪进行动态测量,消除传统方法的热变形误差。
3. 径向跳动与端面跳动检测
在V型铁支撑下,使用百分表检测齿顶圆径向跳动量(≤0.1mm/100mm直径)。端面跳动采用双表法测量,端跳公差应不大于0.08mm。该指标直接影响传动平稳性,特别是高速工况下异常振动的主要诱因。
4. 齿根圆直径检测
使用三爪内径千分尺或气动量仪,在多个截面测量齿根圆实际尺寸。允许偏差范围根据链号确定,如08B链轮控制在φ77.85±0.15mm。该参数异常会导致链条滚子卡滞,加速链板疲劳断裂。
5. 表面硬化层检测
通过显微硬度计进行梯度测试,渗碳层深度应达到0.8-1.2mm(重型链轮)。表面硬度要求HRC58-62,芯部保持HRC25-35韧性。采用金相分析法确认硬化层组织形态,避免出现网状碳化物等缺陷。
6. 动态平衡测试
对于转速超过1500rpm的高速链轮,必须在动平衡机上完成G6.3级平衡校正。残余不平衡量计算式:U=9549×G×m/(n×r),其中G为平衡等级,m为质量(kg),n为转速(rpm)。超标的不平衡量会产生周期性冲击载荷。
7. 材料成分光谱分析
采用直读光谱仪对20CrMnTi、40Cr等合金钢材料进行元素定量分析,碳含量偏差需控制在±0.03%以内。重点监控硫、磷杂质含量(≤0.035%),避免冷脆性倾向。同步进行超声波探伤,检出内部缩孔、夹渣等铸造缺陷。
检测技术发展趋势
当前链轮检测正向智能化方向发展,五轴联动测量机集成AI算法,可自动生成SPC分析报告。工业CT技术实现非破坏性内部结构检测,X射线衍射法用于残余应力精准测量。结合数字孪生技术,建立检测数据与服役性能的预测模型,推动质量控制从合规性检测转向预测性维护。
通过上述系统性检测,可确保链轮参数满足ISO606、ANSI B29.1等国际标准要求,典型传动效率可提升至98%以上,平均无故障工作时间延长3-5倍。建议制造企业建立全尺寸数据库,将检测数据与加工工艺参数联动优化,实现质量闭环控制。
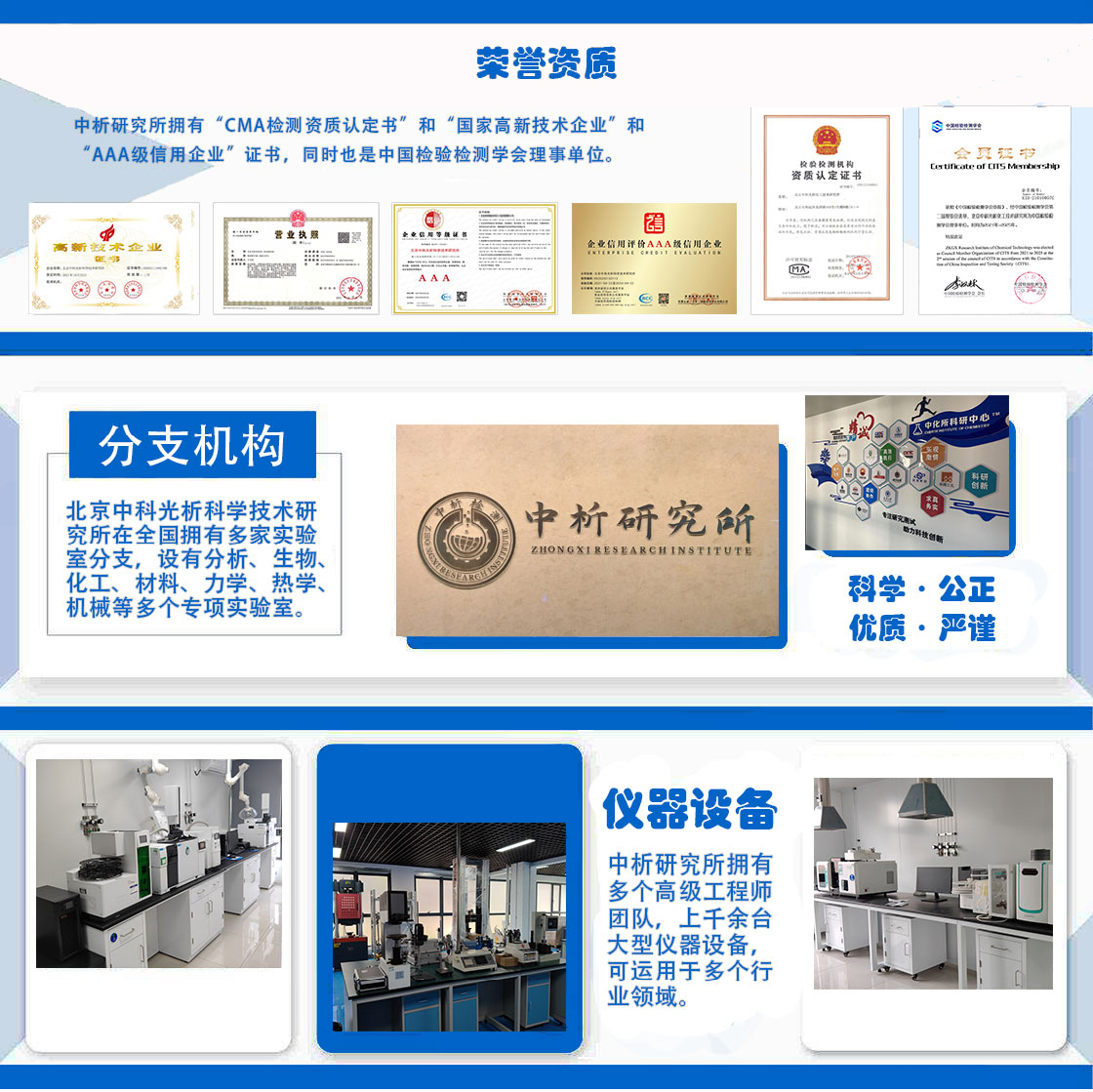
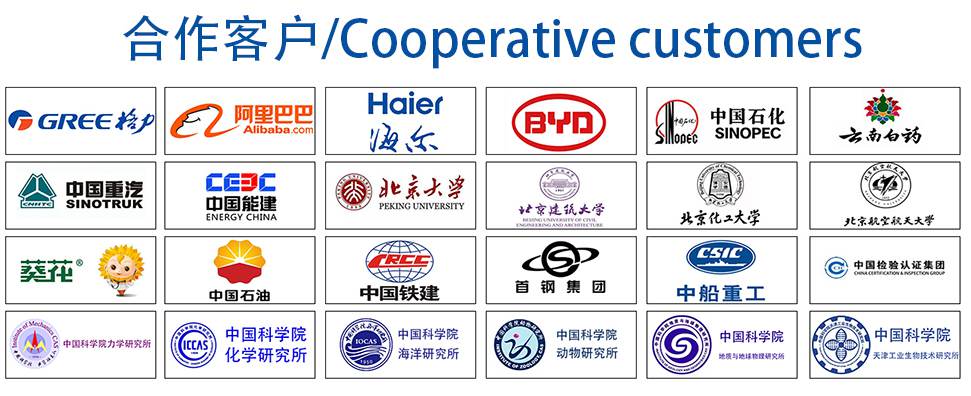