一般现场目视检查检测项目及实施要点
现场目视检查作为最基础、最直观的质量控制手段,在工业生产、工程施工、设备维护等领域具有不可替代的作用。该方法通过人眼观察结合辅助工具,对目标对象的外观、结构、装配状态进行系统性检查,具备成本低、反应快、操作灵活的特点。根据GB/T 2828.1-2012《计数抽样检验程序》和ISO 2859系列标准,目视检查需建立标准化流程,尤其需要重点关注以下检测项目:
1. 外观完整性检查
检查表面是否存在裂纹、凹陷、变形等物理损伤,重点关注焊接接头的完整性。使用5-10倍放大镜辅助观察细微缺陷,配合强光手电进行阴影检测。需特别注意转角、接缝等应力集中区域的异常形貌。
2. 尺寸与形位公差验证
采用标准量具(游标卡尺、千分尺)进行关键尺寸复核,检查法兰平面度、轴类零件直线度等形位公差。根据GB/T 1184-1996标准,重点测量易受外力影响的装配接口尺寸,偏差需控制在允许公差带的60%以内。
3. 表面缺陷检测
系统排查锈蚀、氧化、涂层脱落等表面异常现象。使用表面粗糙度比对样块(Ra值0.8-6.3μm)评估加工面质量,腐蚀深度需用超声测厚仪复核。特别注意隐蔽部位的积灰、油污等潜在污染源。
4. 焊接质量评估
依据NB/T 47013.5-2015标准,检查焊缝成形、焊脚高度、咬边等表观质量。使用焊接检验尺测量余高和错边量,发现气孔、夹渣等缺陷应立即标识。抽查比例不得低于焊缝总长度的20%。
5. 涂装与防腐检查
采用划格法(ASTM D3359)测试涂层附着力,使用磁性测厚仪检测干膜厚度。重点检查阴阳极保护系统的连接状态,沿海地区项目需额外关注盐雾腐蚀迹象。
6. 装配状态确认
核对零部件的安装方向、紧固件扭矩标记、密封件压紧量。使用力矩扳手抽检10%以上高强度螺栓,检查弹性垫圈是否失效。旋转部件需手动盘车确认无卡涩现象。
7. 标识与标签核查
系统检查设备铭牌、流向箭头、警示标识的完整性和清晰度。压力容器需确认检验钢印的有效期,电气设备应核对防爆等级标识。所有标识的材质需符合使用环境要求。
8. 安全防护设施检查
评估防护罩、联锁装置、急停按钮的功能有效性。检查护栏高度是否符合GB 4053.3-2009要求,电气设备接地电阻应使用兆欧表抽测。特别关注移动部件的防护间隙是否超标。
9. 环境适应性检查
针对特殊工况(高温、潮湿、腐蚀性环境),检查材料表面是否有异常变色、脆化现象。使用红外测温仪监测发热部位温度分布,户外设备需确认排水孔通畅性。
10. 文档记录核对
现场检查需同步完成检测记录表填写,包含缺陷位置示意图、测量数据、判定。重要缺陷应拍摄带标尺的数码照片,所有记录需经双人复核并签署检查日期。
值得注意的是,目视检查的有效性高度依赖检查人员的专业素养。根据ASNT SNT-TC-1A标准,检查人员每年应接受不少于16小时的继续教育,并定期进行视力矫正和色觉测试。对于关键设备,建议采用目视检查与无损检测相结合的方式,形成多维度的质量控制体系。
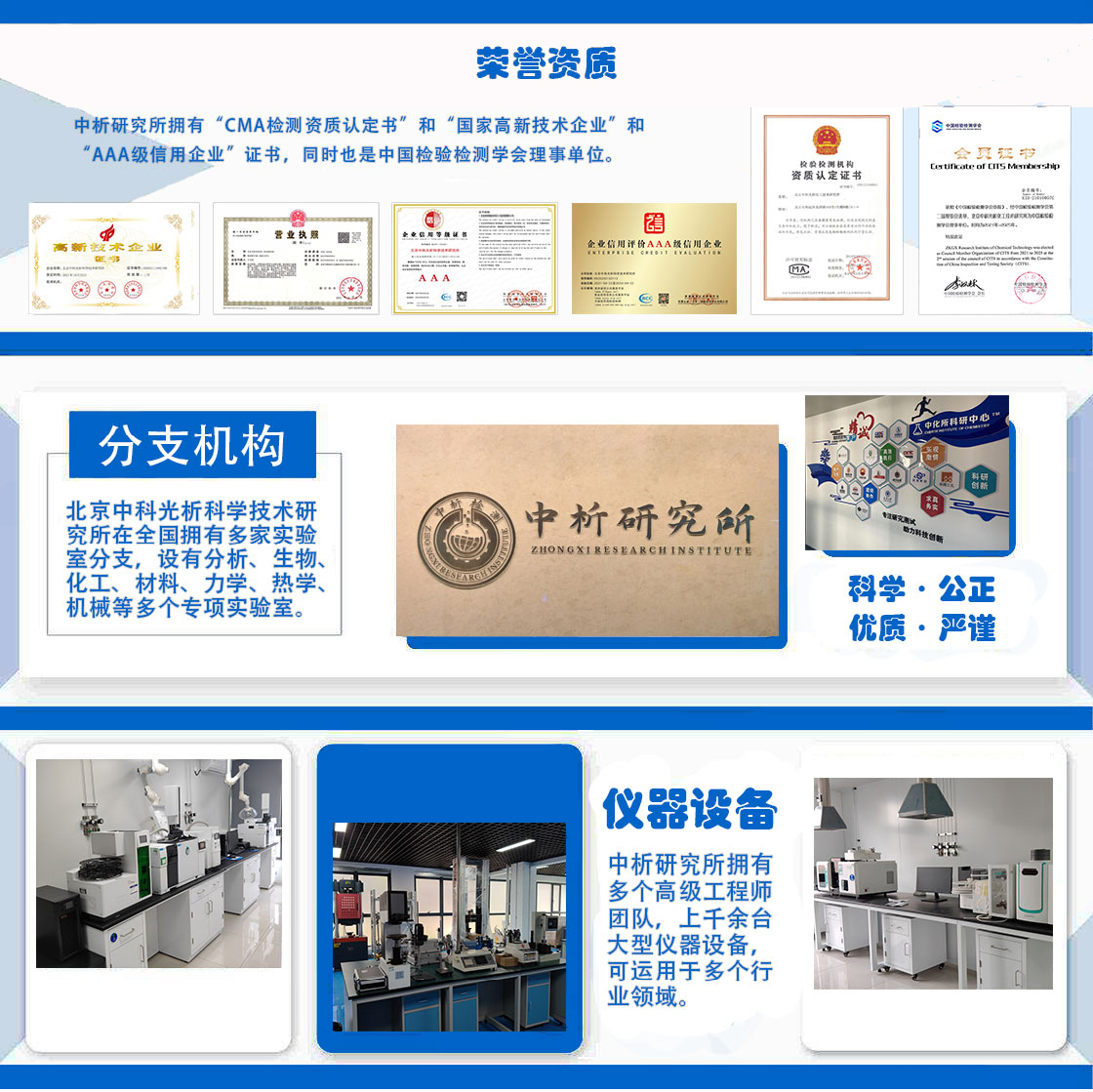
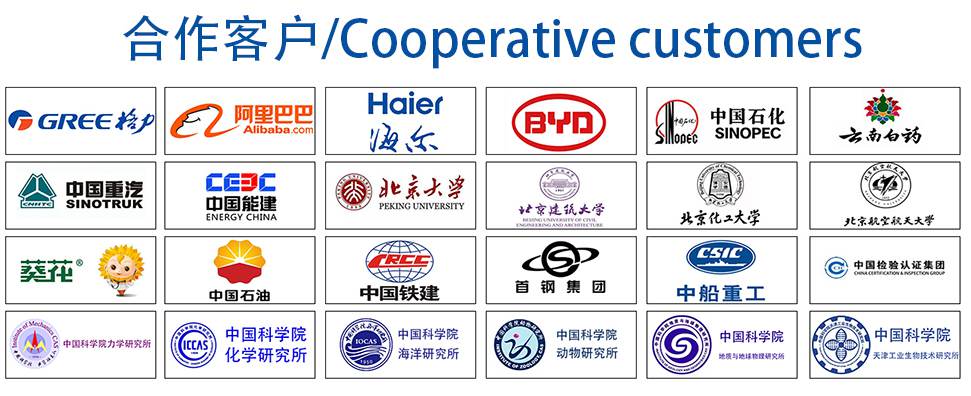