高速动车组作为现代轨道交通的核心运载工具,其安全性、稳定性和运行效率直接关系到旅客生命财产安全和铁路运输秩序。为确保列车在时速350公里及以上的复杂运行环境中可靠工作,需要建立一套科学、系统的检测体系。从车体结构到核心部件,从动态性能到网络控制,高速动车组的检测项目覆盖了全生命周期管理,涉及机械、电气、材料、信息等多个领域。这些检测不仅是日常维护的基础,更是预防重大事故、延长设备寿命的关键环节。
一、转向架系统检测
转向架作为高速列车的"行走机构",承受着轨道冲击、空气动力、制动载荷等多重应力。检测重点包括:轮对踏面损伤检测(使用激光轮缘测量仪)、轴箱轴承温升监测(红外热成像技术)、悬挂系统参数校准(六分力传感器测试)。每运行40万公里需进行轮对镟修,通过车载振动监测系统实时捕捉异常频谱,预防蛇行运动等失稳现象。
二、受电弓-接触网动态检测
在300km/h速度下,受电弓与接触线的接触力波动直接影响电能传输质量。检测列车配备的接触力测量装置可实时监测动态接触压力(标准值70-250N),同步采集硬点冲击(加速度≤500m/s²)、离线电弧等数据。弓网高清摄像系统以每秒4000帧高速拍摄滑板磨损情况,结合紫外成像仪检测电弧放电,确保25kV高压供电系统稳定。
三、制动系统性能验证
制动性能检测包含静态试验和动态验证两个维度。在检修基地使用制动试验台模拟不同载荷下的闸片夹紧力(误差≤±5%),检测单元制动的响应时间(≤1.2秒)。线路试验时通过GPS测速装置记录制动距离,350km/h紧急制动距离需≤6500米。同时监测制动盘温度场分布,确保摩擦材料在600℃高温下仍能保持稳定摩擦系数。
四、网络控制系统诊断
基于TCN标准的列车控制网络需进行三级检测:单板级(PCB电路板自动测试)、设备级(MVB总线通信测试)、系统级(整列列车重联功能验证)。使用协议分析仪捕捉网络传输延时(≤50ms),通过故障注入测试验证控制系统的冗余切换能力。车载诊断系统每天生成超过2GB的运行日志,结合大数据分析预测潜在故障。
五、车体气密性及结构健康监测
通过压力波试验验证车体密封性,在4秒内车厢压力从4000Pa降至1000Pa视为合格。采用分布式光纤传感技术监测车体关键部位应力变化,超过设计载荷20%时触发预警。铝合金车体定期进行涡流探伤,检测蒙皮裂纹长度超过5mm即需修复。车顶导流罩使用相控阵超声检测复合材料分层缺陷,确保空气动力学性能。
随着检测技术向智能化方向发展,高速动车组已实现80%以上检测项目的自动判读。基于数字孪生的预测性维护系统,将检测数据与运营工况深度耦合,使关键部件故障识别准确率达到98%以上。未来5G+AI技术的融合应用,将推动高速列车检测进入实时动态评估的新阶段,为世界高铁安全运营树立技术标杆。
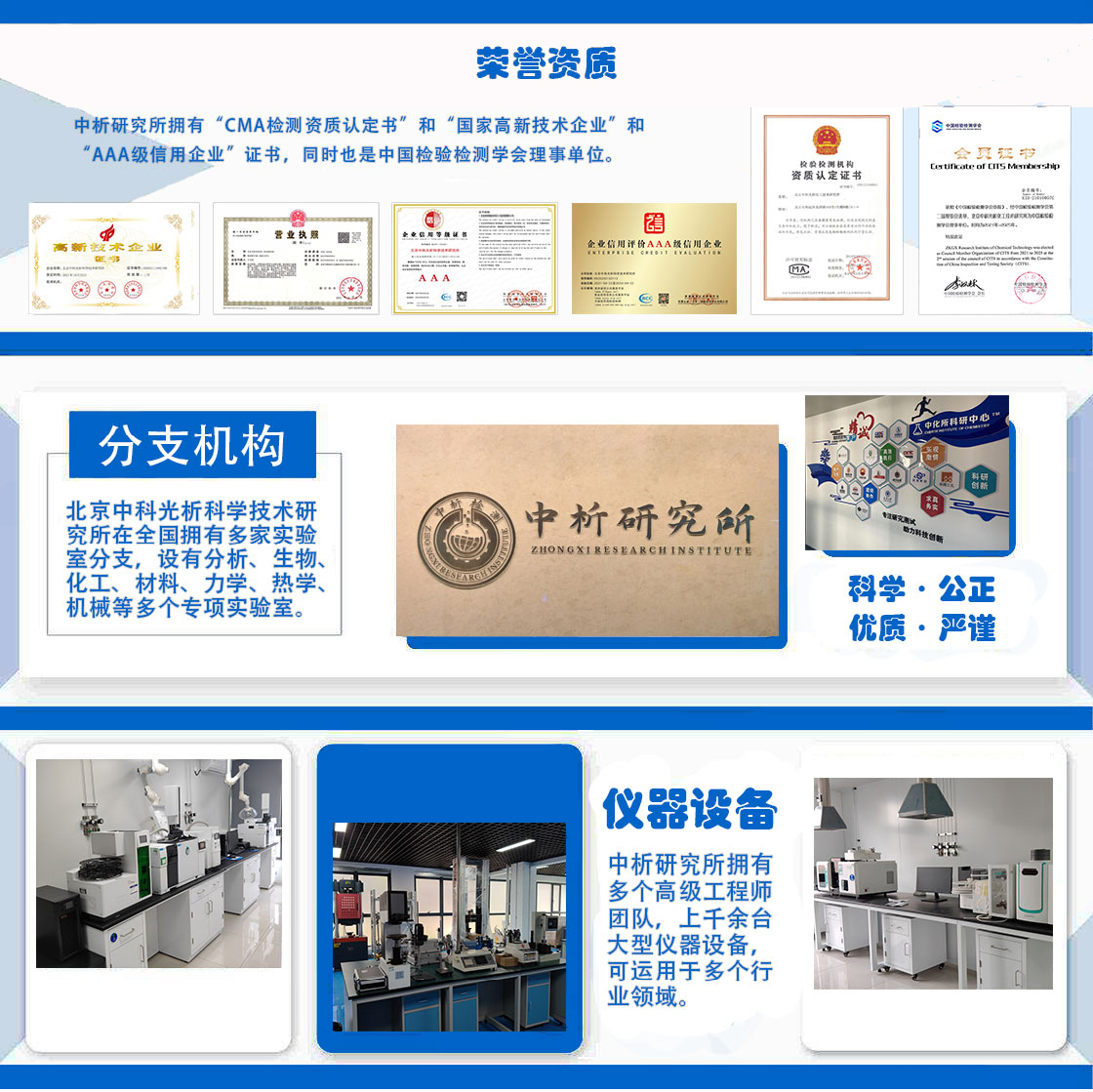
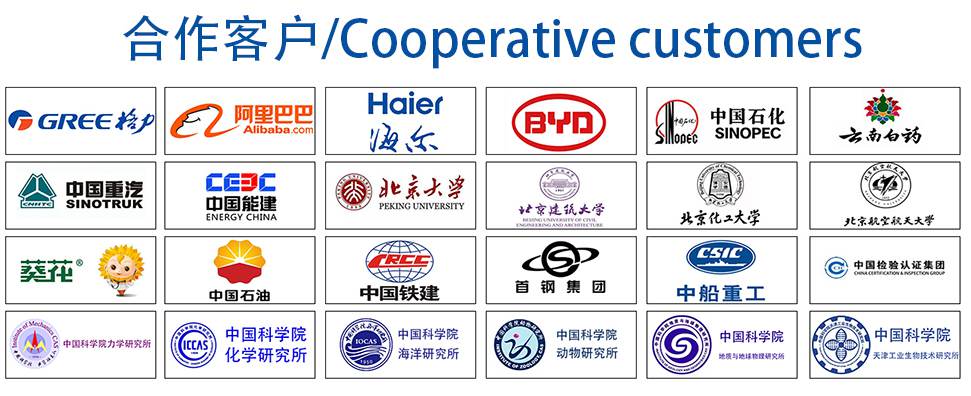