便携式锂离子电池和电池组检测的核心意义
随着移动设备、无人机、电动工具等产品的普及,便携式锂离子电池及电池组已成为现代生活的必需品。然而,其潜在的热失控、短路、过充等问题可能引发严重的安全事故。据国际安全认证机构统计,2022年因电池缺陷导致的火灾事故中,78%与未通过完整检测的劣质产品相关。为确保消费者安全和产品性能的可靠性,各国已建立严格的检测标准体系,涵盖电化学特性、机械强度、环境适应性等30余项关键指标。通过系统性检测,不仅能验证产品的合规性,更能推动电池技术的迭代升级。
安全性能检测项目
安全测试是锂离子电池检测的核心环节,包含过充/过放保护测试(模拟1.5倍额定电压持续充电)、外部短路测试(<5mΩ电阻下检测防爆性能)、高温冲击试验(150℃热箱中观察是否起火爆炸)等。其中针刺测试要求用φ3mm钢针穿透电池本体,30分钟内不得出现明火;挤压测试需施加13kN压力至电池变形量达50%,验证隔膜抗压强度。这些极端条件模拟了电池在滥用场景下的失效模式。
电化学性能检测
容量测试需在20±5℃环境中,以0.2C倍率充放电3次取均值;循环寿命测试要求500次循环后容量保持率≥80%。倍率放电测试需验证3C大电流下的电压稳定性,能量密度检测则通过三维扫描测算实际值。其中荷电保持能力测试需将电池在40℃环境存储28天,容量衰减应小于15%。
环境适应性测试
温度冲击测试要求电池在-40℃~+85℃间快速转换10次,每次保持30分钟;湿热测试需在40℃/93%RH环境中存储48小时。振动测试模拟运输环境,按ISTA 3A标准进行3轴6小时随机振动;低气压测试需在11.6kPa压力下存储6小时,验证密封件可靠性。
标签与标识规范
除性能测试外,标识检测同样关键。必须包含额定容量(mAh)、标称电压(V)、生产日期(年月)、警告标识(禁止拆卸图标)等要素。电池组还需标注串并联方式(如2P4S),防火等级标识(UL94 V-0以上),以及符合UN38.3、IEC62133等标准的认证标志。二维码追溯系统需能完整显示生产批次和检测报告编号。
机械可靠性验证
跌落测试要求电池从1.2m高度26次自由跌落(6面+12棱+8角),外壳不得破裂;振动测试需承受10Hz-55Hz扫频振动3小时。滚筒测试针对小型电池,需在直径200mm滚筒内以5r/min转速跌落100次,验证结构完整性。对于动力电池组,还需进行IP67防水测试和盐雾腐蚀试验。
通过上述多维度的系统化检测,可有效识别电池设计缺陷,推动企业改进电极材料选择、BMS保护策略和结构封装工艺。当前头部电池厂商的检测项目已拓展至50余项,覆盖从原材料到终端产品的全生命周期质量管控体系。
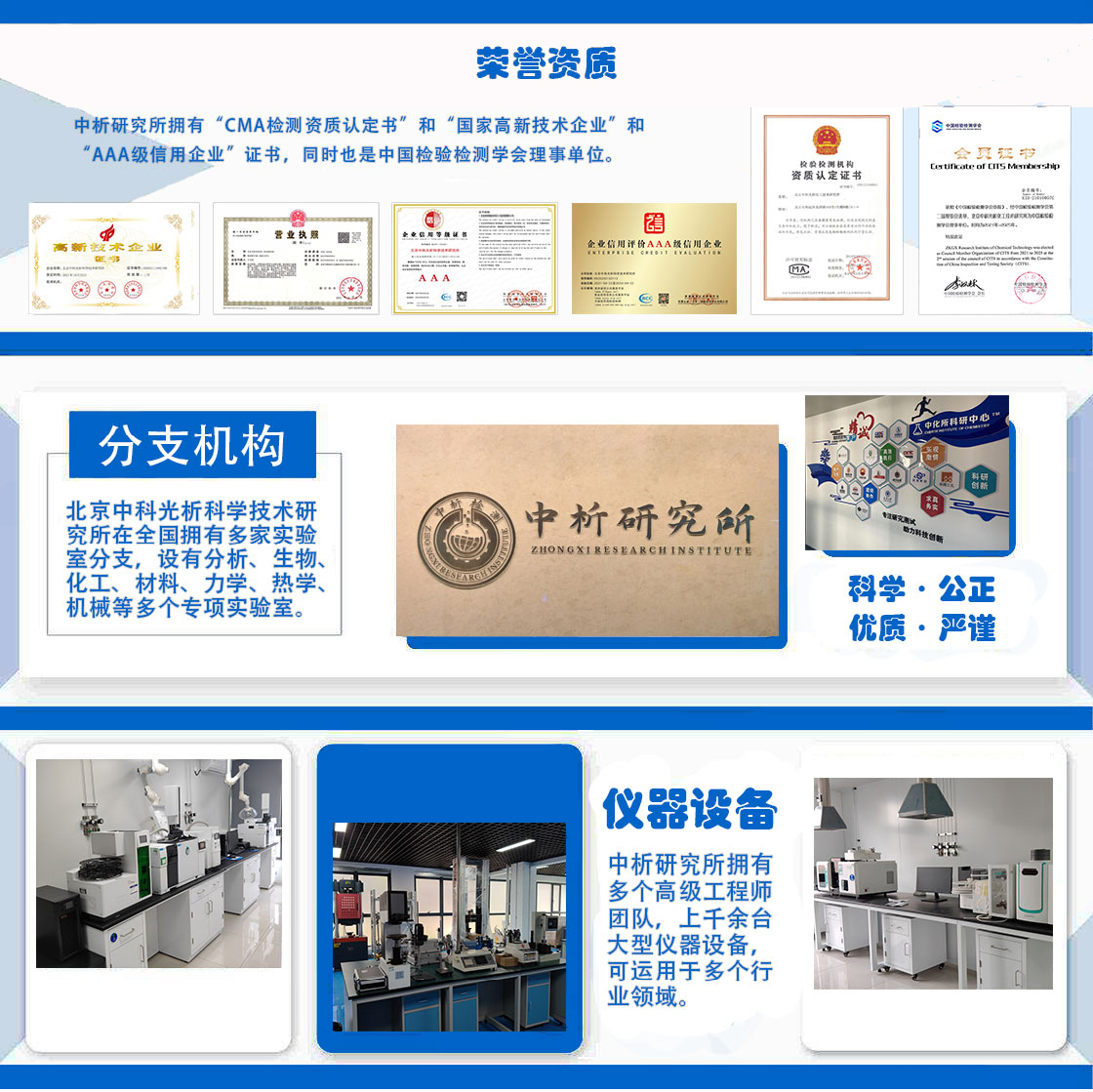
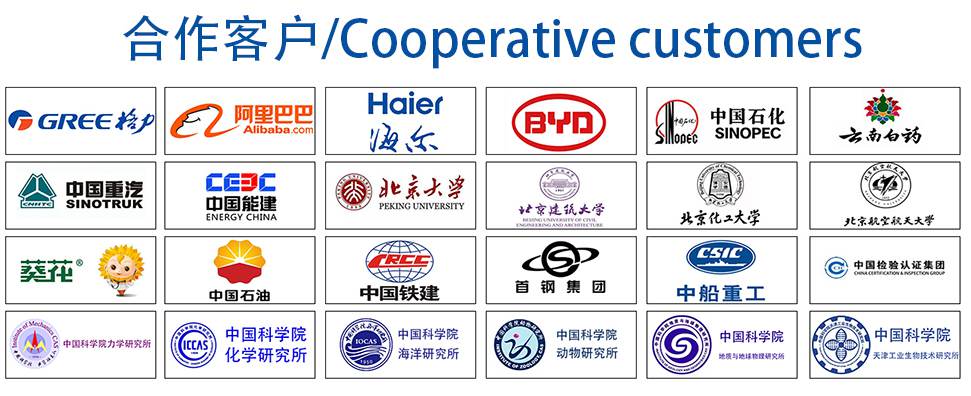