含气饮料瓶检测:守护产品安全与消费体验的核心环节
含气饮料瓶作为碳酸饮料、气泡水等产品的关键包装容器,其质量直接影响产品保质期、安全性及消费者体验。由于瓶内饮料在灌装后持续产生二氧化碳压力,对瓶体的密封性、耐压性、材料稳定性提出更高要求。近年来,国内外频繁出现的饮料瓶爆炸事故及泄漏问题,进一步突显了系统化检测的重要性。从生产原料到成品包装,含气饮料瓶需经过十余项专业检测,确保其在不同环境下的性能可靠性。
核心检测项目解析
1. 密封性检测
通过气密性测试仪模拟运输振动、温度变化等场景,检测瓶盖与瓶口的密封配合度。采用差压法或水浸法识别微米级泄漏,确保二氧化碳留存率符合GB/T 10792标准要求。不合格产品会导致气体逸散,直接影响饮料口感与保质期。
2. 压力耐受测试
利用爆破压力试验机进行极限压力测试,检测瓶体在3-6倍工作压力下的形变情况。依据ASTM D3078标准,PET材质碳酸饮料瓶爆破压需≥1.6MPa。同时开展周期性压力疲劳测试,模拟多次开合后的抗压能力衰减曲线。
3. 材料成分分析
采用红外光谱仪检测PET树脂的分子结构完整性,防止回收料混入导致的强度下降。针对瓶口螺纹等重点部位,通过X射线荧光光谱仪(XRF)检测重金属迁移量,确保符合FDA 21 CFR及欧盟EU 10/2011食品接触材料法规。
精细化质量控制体系
4. 容量精度校验
使用激光三维扫描系统测量瓶体容积偏差,配合灌装线动态称重检测,将误差控制在±1.5%以内。尤其关注瓶底加强筋对实际容量的影响,避免因设计缺陷导致货架期内容量波动。
5. 瓶口尺寸检测
采用光学坐标测量仪对瓶口外径、螺纹角度等18项参数进行微米级测量,确保与瓶盖的精确匹配。重点监控螺纹根部应力集中区域,防止旋盖过程中产生微裂纹。
环境模拟与终端验证
6. 极端条件测试
在温湿度交变试验箱中模拟-20℃至55℃的储运环境,测试瓶体抗结晶化能力。通过跌落试验机进行1.8m高度多角度跌落测试,评估瓶体抗冲击性能,防止冷链运输中的脆性破裂。
7. 消费者使用模拟
采用机器人手臂模拟2000次开盖动作,检测瓶盖旋紧扭矩衰减情况。通过高速摄像机记录开瓶瞬间的泡沫溢出量,优化瓶口流体力学设计,确保开启安全性与饮用舒适度。
结语
完善的含气饮料瓶检测体系需要整合材料科学、机械工程、流体力学等多学科技术,通过40余项检测数据的动态分析,构建从原料粒子到成品包装的全生命周期质量模型。随着智能传感器和AI视觉检测技术的应用,行业正逐步实现检测精度从毫米级向微米级的跨越,为碳酸饮料市场筑起坚实的安全防线。
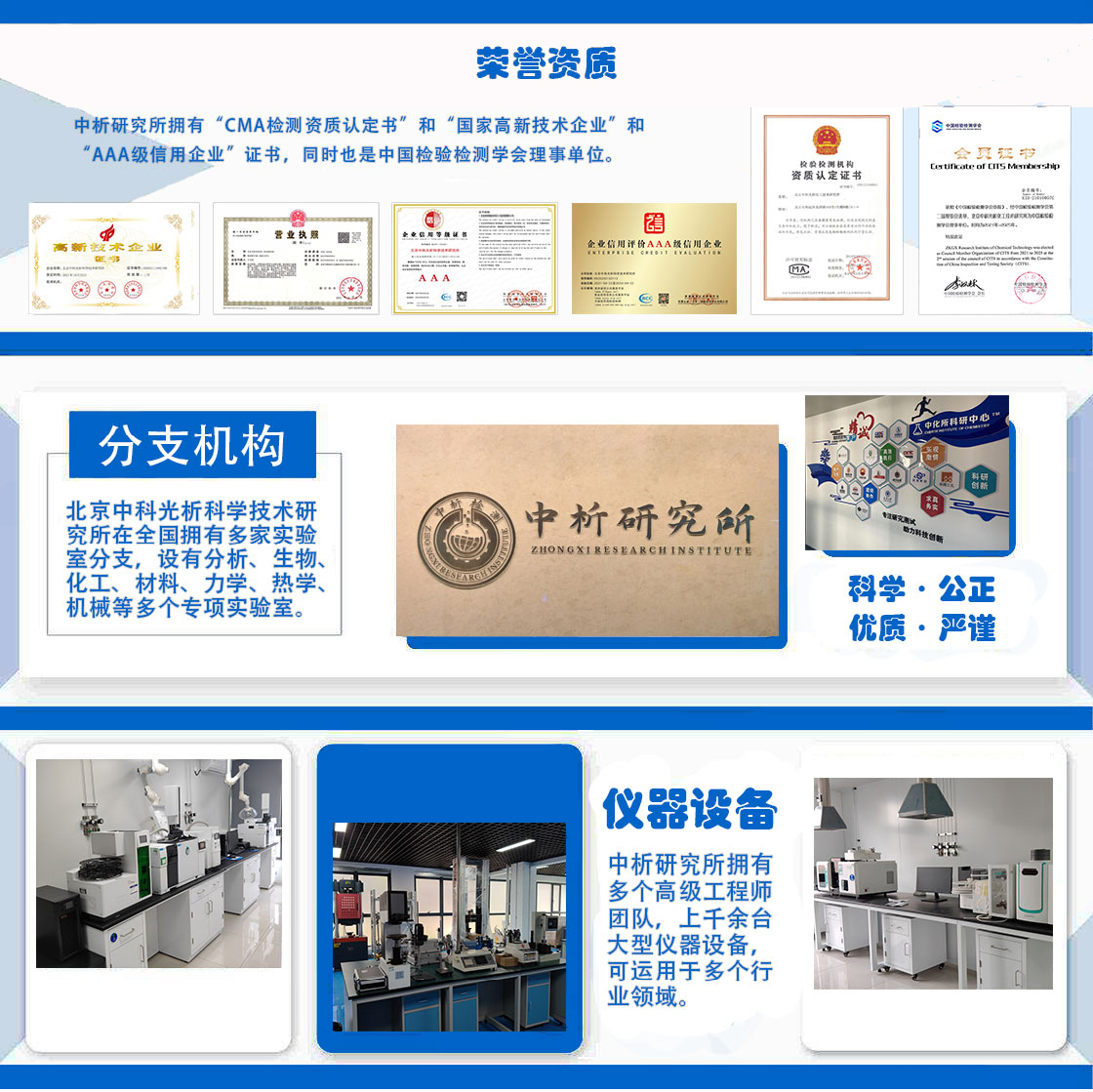
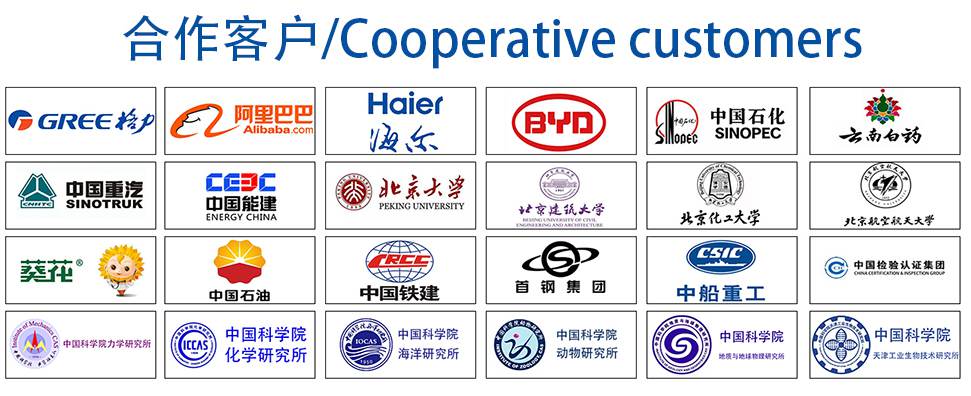