真空保温瓶检测的重要性与标准
真空保温瓶作为现代生活中常见的日用品,凭借其优异的保温性能广泛应用于家庭、办公、户外等场景。随着消费者对产品品质和安全性的关注度不断提升,真空保温瓶的检测标准也日益严格。无论是生产过程中的质量控制,还是消费者购买后的性能验证,都需要通过科学的检测项目来确保产品符合国家标准和用户需求。目前,国内外对真空保温瓶的检测主要围绕保温性能、密封性、材质安全性以及结构耐久性等方面展开,这些检测项目不仅关系到用户体验,更直接影响产品的市场竞争力。
核心检测项目解析
1. 保温性能测试
保温性能是真空保温瓶的核心指标。检测时需在标准条件下(如22℃±5℃室温)将95℃±1℃热水注入瓶内,记录6小时、12小时、24小时后的温度变化。优质产品需满足国家标准(如GB/T 29606-2013)要求:6小时水温不低于68℃,24小时不低于42℃。测试需排除环境湿度、气压等因素的干扰,采用精密温度记录仪进行数据采集。
2. 密封性检测
通过加压测试和倾斜振动试验验证瓶体密封性。将真空保温瓶注满水后倒置,在50kPa压力下保持1分钟观察是否渗漏;模拟日常使用场景进行多次倾斜、摇晃测试,确保瓶盖与瓶口的配合度符合标准。部分检测机构还会使用氦质谱检漏仪进行微泄漏检测,精度可达10^-9 Pa·m³/s。
3. 材质安全检测
针对食品接触材料进行严格筛查:不锈钢内胆需通过GB 4806.9-2016测试,包括铅、镉、砷等重金属迁移量检测;塑料部件需符合GB 4806.7-2016对双酚A、塑化剂的限量要求。国际认证产品还需满足FDA或LFGB标准,部分高端型号会额外进行RoHS指令中的有害物质检测。
4. 结构强度测试
通过跌落试验(1.2米高度自由落体至水泥地面)验证瓶体抗冲击性;对瓶口螺纹进行500次开合耐久性测试;手柄、按键等配件需承受50N拉力保持1分钟无脱落。近年新增的极端温度循环测试(-20℃至100℃交替冲击)可有效验证真空层的热稳定性。
检测技术与设备升级
随着技术进步,真空保温瓶检测逐步向智能化发展。红外热成像仪可快速定位真空层缺陷部位,X射线检测设备能无损分析双层结构完整性。部分实验室引入恒温恒湿箱模拟高原、极寒等特殊环境,配合物联网传感器实现检测数据的实时上传与分析。
选购建议与质量识别
消费者可通过简单方法初步验证保温性能:将沸水注入瓶体静置2分钟后触摸外壁,优质产品应无明显温升;检查瓶口密封圈是否平整无毛边;查看产品是否标注执行标准并通过、等第三方检测认证。建议选择瓶身一体成型、真空排气口可见的正规品牌产品。
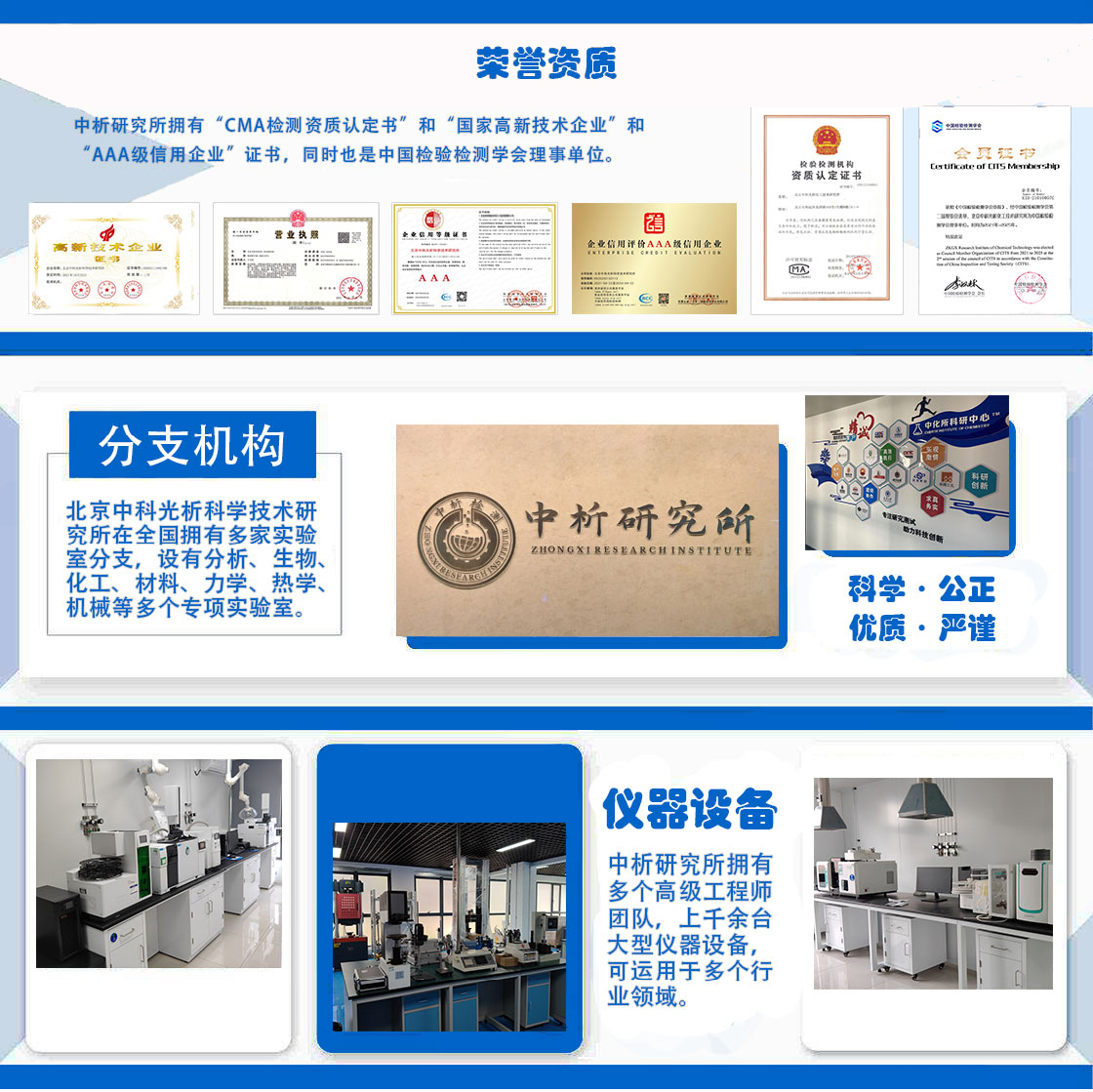
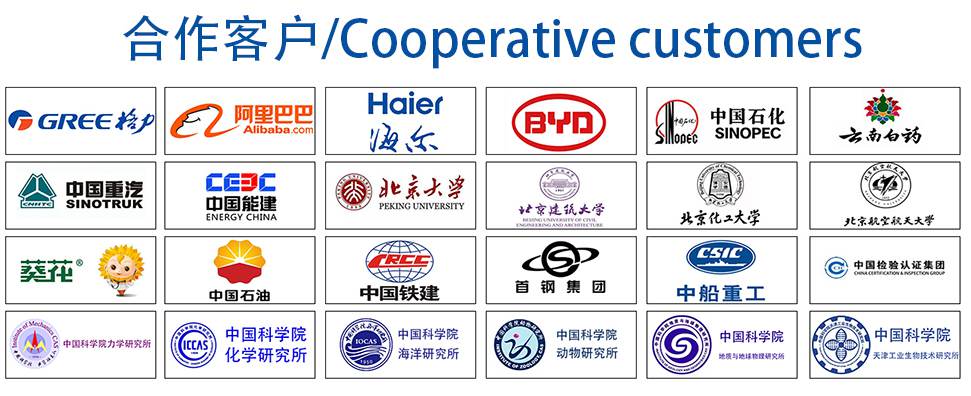