保温瓶瓶胆检测:关键技术指标与流程解析
保温瓶作为日常生活中广泛使用的容器,其核心性能取决于瓶胆的制造质量。瓶胆通常由双层玻璃结构、真空层及镀银(或镀铜)反射层组成,通过阻断热传导、热对流和热辐射实现保温效果。然而,生产过程中可能因工艺偏差、材料缺陷或组装问题导致瓶胆性能下降。因此,严格的瓶胆检测是确保产品使用寿命、保温效率及安全性的关键环节。检测项目需覆盖物理性能、化学稳定性及结构完整性,以验证其是否符合国家标准(如GB/T 11416-2002)或行业规范。
1. 真空度检测
真空层是保温瓶胆的核心结构,其真空度直接影响隔热性能。检测时通常采用氦质谱检漏仪或热偶真空计,通过测量瓶胆夹层的残余气体压力来评估真空度。标准要求真空度≤1.0×10⁻²Pa,若数值超标会导致空气分子热传导加剧,保温时间显著缩短。需注意,长期存放后可能出现“慢漏气”现象,因此需结合加速老化试验验证真空维持能力。
2. 密封性测试
瓶胆的密封性关乎真空层稳定性与使用安全性。检测方法包括气压测试和水压试验:将瓶胆置于特定压力环境(通常≥0.6MPa),观察是否出现漏气或破裂。对于双层玻璃接口、尾管封接处等关键部位,还需借助显微镜检查焊缝均匀性,避免微裂纹导致慢性泄漏。
3. 镀层质量分析
反射镀层的均匀性与附着力直接影响热辐射阻隔效率。检测时通过目视法检查镀层是否存在脱落、气泡或色差,并采用光谱仪分析镀层厚度(通常银层厚度≥0.15μm)。同时需进行附着力测试,用胶带粘贴后快速剥离,观察镀层是否脱落。劣质镀层会降低反射率,导致保温性能下降30%以上。
4. 耐温冲击试验
瓶胆需承受急剧温度变化而不破裂。检测时将瓶胆从100℃沸水立即浸入0-5℃冰水中,循环5次后检查是否出现裂纹。此测试模拟实际使用中倒入热水或冷饮的场景,若玻璃内应力分布不均或退火工艺不当,易发生爆裂风险。
5. 抗机械冲击性能
通过自由落体试验评估瓶胆抗冲击能力:将样品从1.2m高度(模拟日常跌落场景)以特定角度跌落到硬质地面,检测破损情况。优质瓶胆会采用钢化玻璃或增加外层防护涂层,破碎后应呈钝角颗粒,避免尖锐碎片造成伤害。
6. 化学稳定性检测
瓶胆内层玻璃需具备耐酸碱腐蚀特性。将4%醋酸溶液注入瓶胆,在80℃环境下静置24小时后,通过原子吸收光谱法检测铅、镉等重金属溶出量,确保符合GB 4806.5-2016食品接触材料安全标准。同时需验证长期使用后是否出现玻璃表面白化或剥落现象。
通过上述系统性检测,可全面评估保温瓶胆的性能指标。生产企业需建立从原材料筛选到成品抽检的全流程质控体系,而消费者在选购时亦可关注瓶胆底部的QS认证标识及检测报告,确保产品安全性与保温效能。
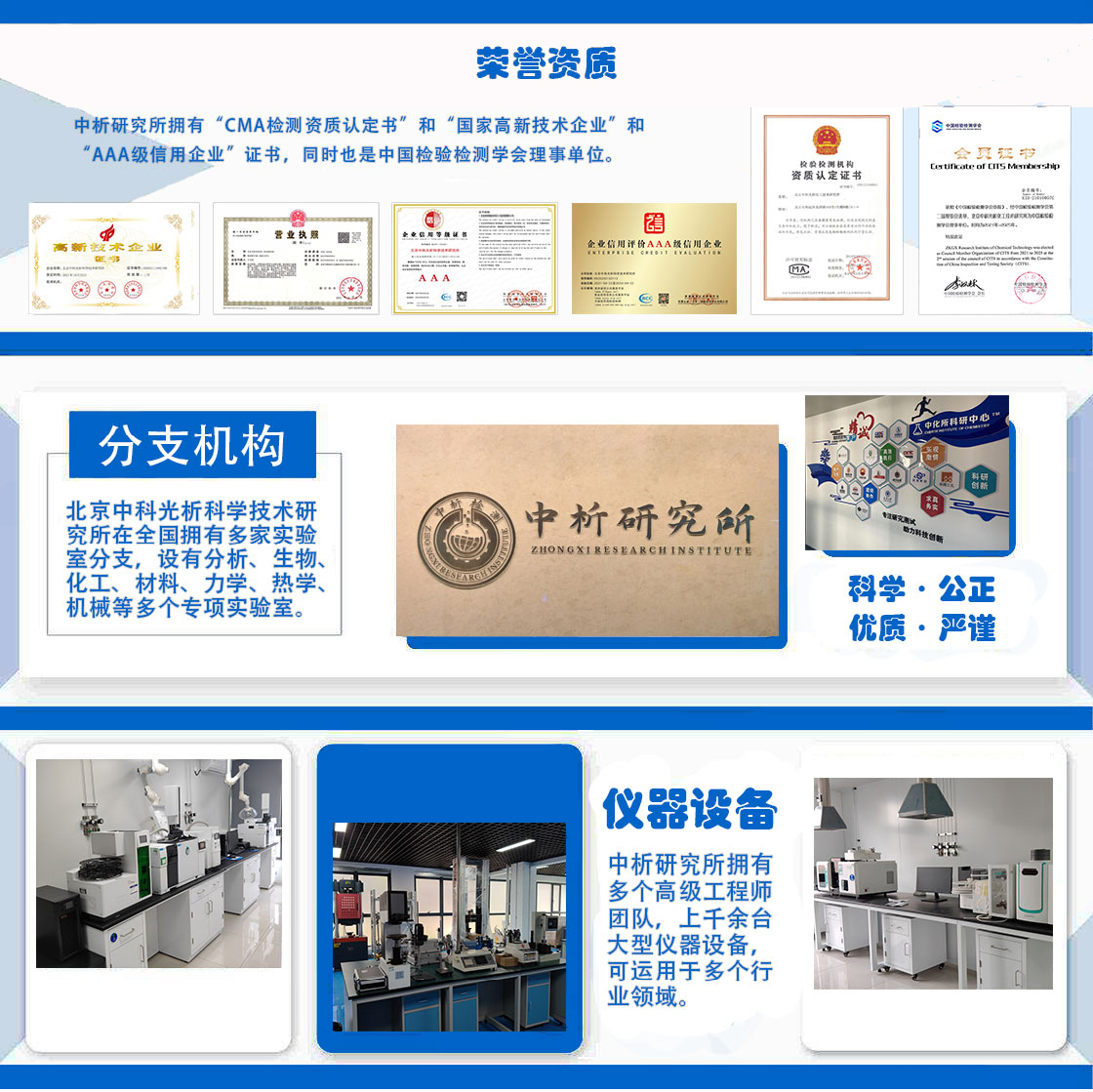
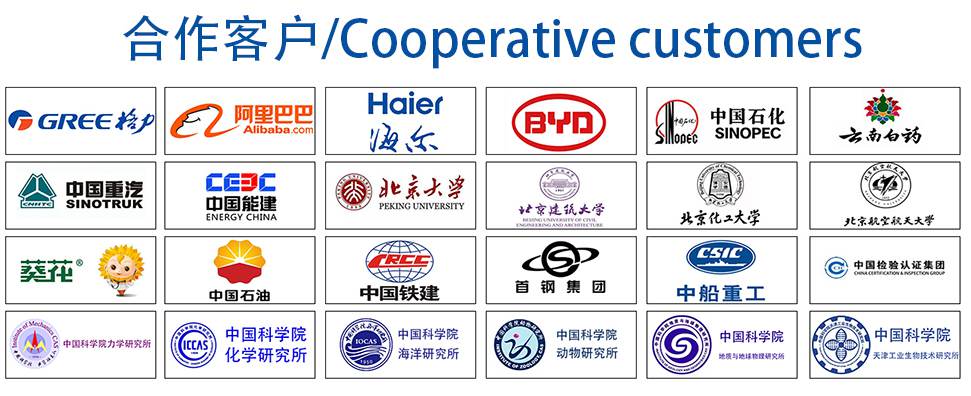