旋转钻探和减震用橡胶软管及软管组合件检测的重要性
在石油勘探、矿山开采及重型机械作业领域,旋转钻探和减震用橡胶软管及软管组合件作为核心传输与缓冲元件,其性能直接影响设备运行效率和作业安全。这类软管长期承受高压流体冲击、剧烈振动及复杂环境侵蚀,一旦发生破裂或老化,可能引发设备故障甚至安全事故。因此,建立系统的检测流程并严格把控质量标准,是保障工业设备稳定运行、延长软管使用寿命的核心措施。
核心检测项目及技术规范
1. 物理性能检测
包括软管内外径尺寸公差测量、壁厚均匀性分析、表面缺陷(裂纹/气泡/杂质)目视检查。通过拉伸试验机测试扯断强度(≥16MPa)和伸长率(≥400%),验证橡胶基材的机械性能是否符合GB/T 5563标准要求。
2. 耐压性能测试
采用脉冲试验台进行动态压力循环测试(最高压力35MPa,频率0.5Hz),模拟实际工况下的压力波动。静压测试需保持2倍工作压力1小时后无渗漏,爆破压力需达到额定值的4倍以上,符合API 7K规范对钻探软管的特殊要求。
3. 环境耐受性评估
通过高低温交变箱(-40℃~120℃)验证软管耐温性能,模拟极寒/高温环境下橡胶的柔韧性变化。耐油性测试需浸泡在IRM903标准油液72小时,体积膨胀率需≤50%。臭氧老化箱测试(50pphm浓度)168小时后不得出现龟裂现象。
4. 接头连接可靠性验证
使用扭矩测试仪检测软管与金属接头的装配质量,测试压力交变下的抗拉脱性能(≥80%爆破压力)。采用氦质谱检漏法检测连接处密封性,泄漏率需<1×10⁻⁶ Pa·m³/s,满足ISO 18752对高压软管组合件的严苛要求。
5. 动态减震效能分析
配备振动试验台模拟10~200Hz振动频谱,通过加速度传感器记录振动传递衰减率。要求安装软管组合件后,设备基座振动幅度降低60%以上,符合JB/T 8732对减震软管的性能指标。
检测方法与标准体系
检测过程需严格参照API Spec 7K(旋转钻探设备规范)、ISO 6803(橡胶软管脉冲试验方法)及GB/T 3683(橡胶软管及软管组合件试验方法)等标准。对于海洋平台等特殊应用场景,还需增加盐雾腐蚀试验(2000小时)和阻燃性能测试(氧指数≥28%)。
质量控制的关键节点
从原材料进厂检验(橡胶硫化程度、帘线拉伸强度)到成品出厂前100%气密性检测,需建立全过程质量追溯体系。特别关注软管屈挠部位的老化痕迹,运用工业内窥镜进行内部结构检测,确保无帘线断裂或橡胶分层现象。
结语
通过系统化的检测流程,可有效识别旋转钻探和减震软管的潜在失效风险。建议企业建立基于大数据分析的寿命预测模型,结合定期检测数据动态调整维护周期,实现从被动维修到主动预防的转型升级,为重型装备安全运行提供可靠保障。
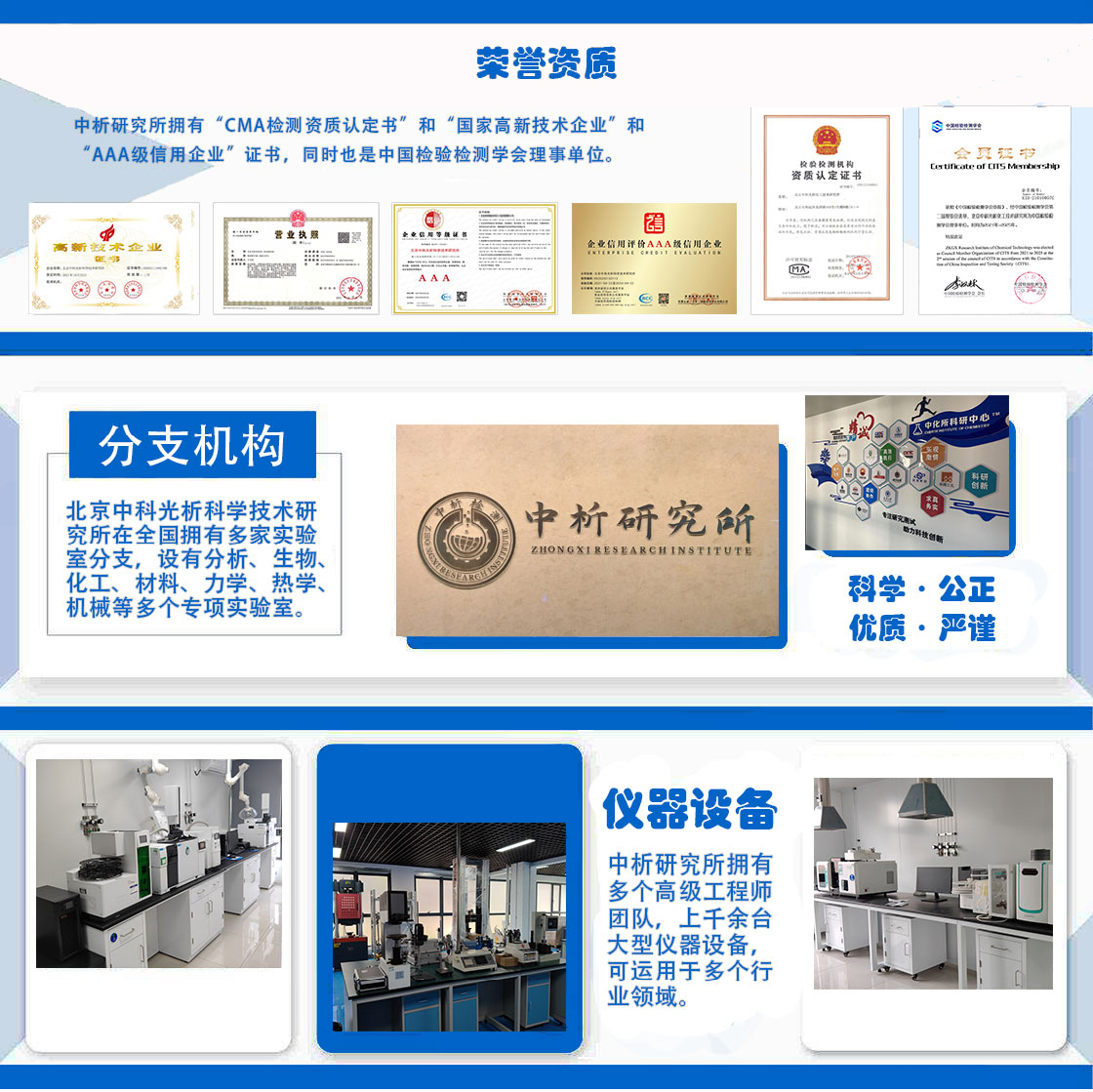
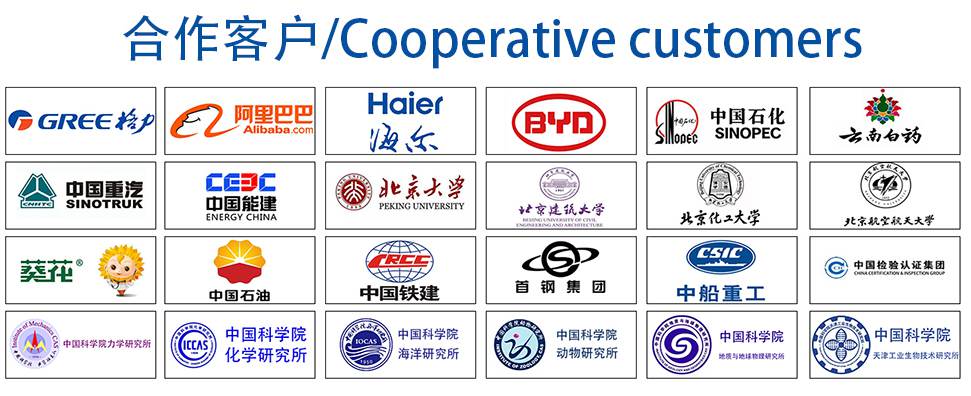