飞机地面加油和排油用橡胶软管及软管组合件检测的重要性
飞机地面加油和排油用橡胶软管及软管组合件是航空燃油输送系统的核心部件,其性能直接关系到飞行安全和运营效率。由于这些软管长期暴露于极端温度、化学腐蚀、机械应力等复杂环境中,任何结构缺陷或性能衰退都可能导致燃油泄漏、静电积聚甚至火灾风险。因此,定期开展全面、科学的检测项目至关重要,以确保软管满足国际航空标准(如FAA、ISO等)和行业规范(如SAE AS1339)。
关键检测项目及技术要点
1. 结构完整性检测
通过目视检查、尺寸测量和X射线成像技术,评估软管的内衬层、增强层和外覆层是否存在裂纹、磨损或变形。重点检测接头部位的密封性,确保无渗漏风险。
2. 耐液压性能测试
模拟实际工作压力(通常为3-10 MPa),在静态和脉冲压力下验证软管的抗压能力。检测内容包括压力保持性、膨胀率及爆破压力,确保软管在极端工况下的稳定性。
3. 导电性能验证
使用电阻测试仪测量软管整体电阻值(需≤10^4 Ω/m),确认静电导出能力符合MIL-DTL-25516等标准,避免燃油输送过程中静电积聚引发燃爆事故。
4. 材料老化与耐介质性分析
通过热氧老化试验、耐油性测试(ASTM D471)和臭氧暴露试验,评估橡胶材料在长期接触航空燃油、润滑油及环境因素下的劣化程度,确保材料寿命≥5年。
5. 低温柔韧性与高温耐受性测试
在-40℃低温环境中进行弯曲试验,验证软管在寒冷条件下的抗脆裂能力;同时进行150℃高温曝露测试,检测材料软化或变形情况。
6. 动态弯曲疲劳试验
模拟地面加油车的频繁移动场景,通过机械臂进行万次以上弯曲循环测试,监测外层橡胶龟裂、增强层断裂等疲劳失效现象。
检测周期与注意事项
建议每6个月进行一次全面检测,高频使用场景需缩短至3个月。检测时需注意清洁管腔残留燃油、避免机械损伤,并严格记录批次编号和检测数据。对于已发现局部损伤的软管,禁止采用修补方式复用,必须按照适航要求强制报废。
通过上述系统化检测,可有效预防因软管失效导致的航空事故,同时降低燃油污染和运营成本。航空公司及地勤单位应建立完善的检测档案,并优先选择通过NADCAP认证的第三方检测机构合作。
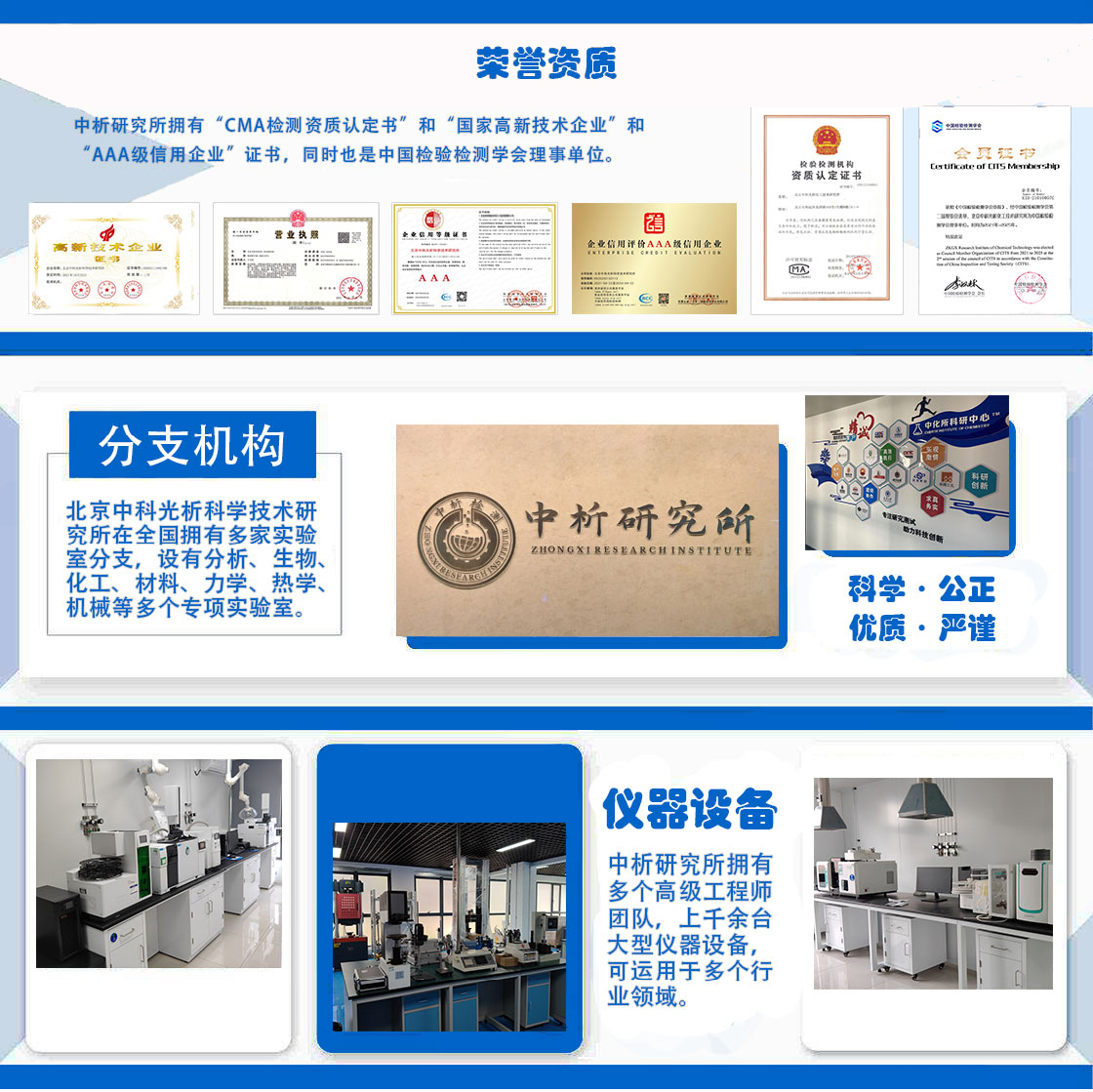
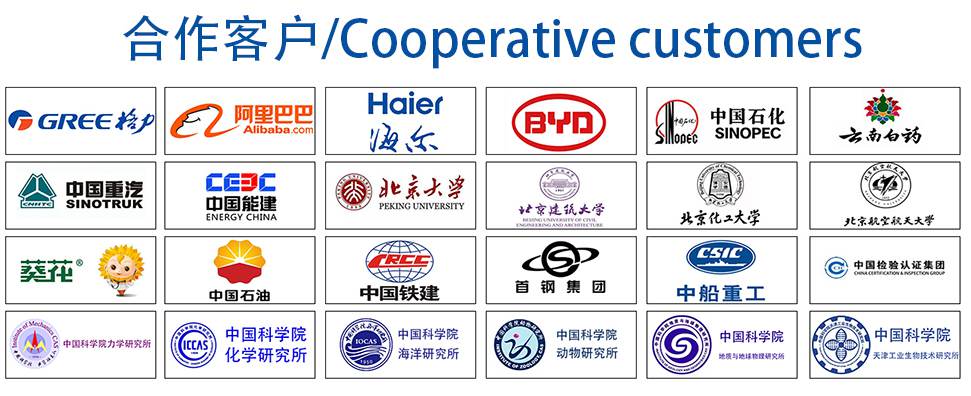