耐液压油和燃油丁腈橡胶胶料检测的重要性
丁腈橡胶(NBR)因其优异的耐油性、耐磨性和抗压缩变形能力,广泛用于制造液压系统密封件、燃油管路、油箱衬垫等关键部件。然而,在复杂工况下,液压油和燃油中的化学物质可能导致橡胶材料膨胀、硬化或强度下降,进而引发设备泄漏或失效。因此,对丁腈橡胶胶料进行耐液压油和燃油性能的系统化检测,是确保其长期稳定性和安全性的核心环节。通过科学评估材料的物理性能变化、耐介质侵蚀能力及环境适应性,可为材料选型、配方优化和质量控制提供数据支撑。
核心检测项目及方法
1. 物理性能测试
包括拉伸强度、断裂伸长率、硬度(邵氏A)和压缩永久变形等指标的测定。测试前需按GB/T 528-2009或ISO 37标准制备试样,通过万能材料试验机完成力学性能评估。压缩永久变形测试需模拟实际密封件受压状态,评估材料在长期压缩后的恢复能力。
2. 耐油性测试
依据GB/T 1690-2010或ASTM D471标准,将试样浸泡于目标介质(如46#液压油、柴油、汽油)中。测试条件通常设置为70℃×72h,测定体积变化率、质量变化率和硬度变化。耐燃油测试需特别关注芳香烃含量差异对溶胀率的影响。
3. 热老化性能
通过热空气老化试验(GB/T 3512-2014)评估材料在高温下的性能衰减。典型测试条件为100℃×72h,对比老化前后拉伸强度、断裂伸长率的变化率,判断材料耐热氧化稳定性。
4. 低温性能评价
采用低温脆性试验(GB/T 15256-2014)和压缩耐寒系数测试,验证材料在-40℃至-20℃环境下的柔韧性,防止低温脆裂导致的密封失效。
5. 耐化学介质扩展测试
除标准液压油/燃油外,需根据实际接触介质(如齿轮油、刹车液、酸碱溶液)进行针对性测试,评估材料在复杂工况下的耐受极限。
质量控制的关键点
企业应建立从原料到成品的全流程检测体系,重点关注胶料配方中丙烯腈含量(影响耐油性)、硫化体系(决定交联密度)及补强填料的选择。建议每批次产品进行抽检,并定期开展加速老化试验验证长期性能。检测数据需与历史记录对比分析,及时优化生产工艺。
通过系统的耐液压油和燃油丁腈橡胶检测,可有效预判材料在实际应用中的性能表现,降低设备故障风险。检测机构及生产企业需严格遵循国际/国家规范,结合具体工况设计检测方案,确保检测结果的科学性和可比性。
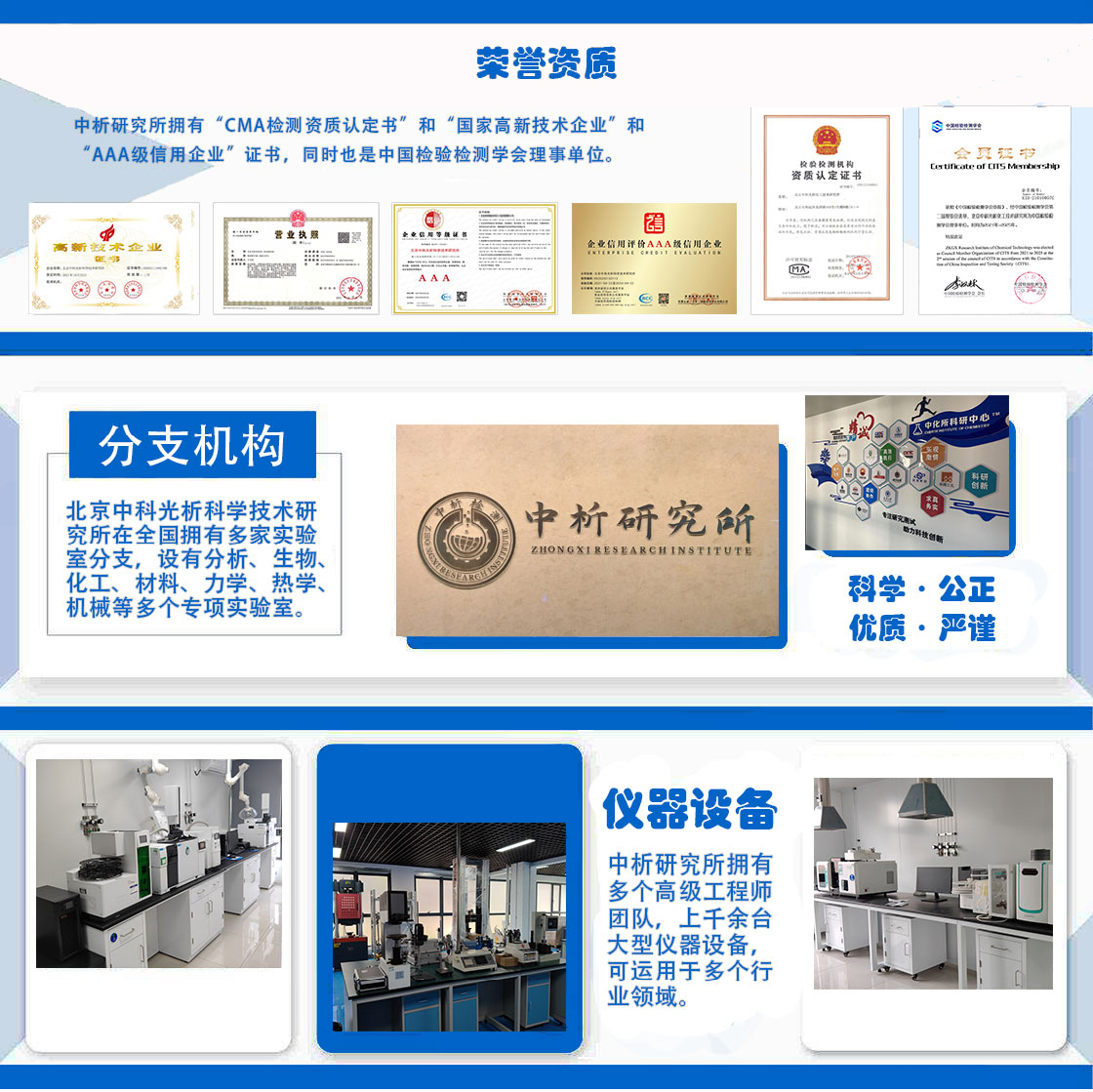
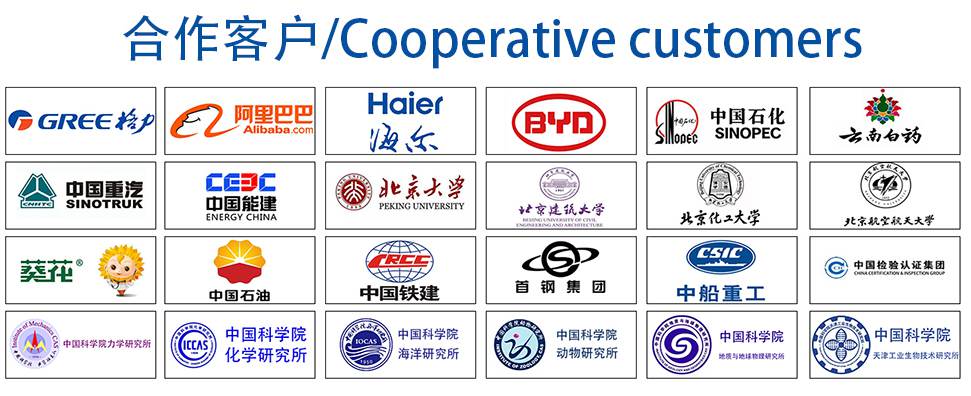