软油囊检测的重要性与技术要点
软油囊作为柔性容器,广泛应用于航空燃料存储、船舶油料运输、工业润滑系统等领域,其安全性与可靠性直接关系到设备运行效率及作业安全。由于软油囊长期处于高压、腐蚀或温度变化环境中,可能因材质老化、结构损伤或密封失效引发泄漏风险。因此,系统化的软油囊检测项目成为保障其性能的核心环节。本文将从外观检验到功能性测试,详细解析软油囊检测的关键内容。
一、外观与结构完整性检测
检测人员需对软油囊表面进行目视检查,重点关注划痕、鼓包、褶皱及接缝处异常。使用高精度测厚仪测量囊体厚度,确保材质均匀性;通过紫外灯或荧光渗透剂排查微观裂纹。对于多层复合结构软油囊,需借助超声探伤技术检测夹层是否出现分层或气泡。
二、密封性能测试
采用气压法或水压法模拟实际工况压力,观察压力表数值变化并记录保压时间。对于高风险应用场景(如航空燃油囊),需使用氦质谱检漏仪进行微量泄漏检测,灵敏度可达1×10⁻⁶ Pa·m³/s。动态密封测试需结合振动台模拟运输状态下的密封维持能力。
三、材料性能验证
通过取样测试确认橡胶或高分子材料的理化指标:
- 拉伸强度测试(ASTM D412标准)
- 耐油溶胀实验(浸泡72小时后体积变化率)
- 低温脆性测试(-40℃环境下弯曲性能)
- 抗臭氧老化试验(50pphm浓度下500小时暴露)
四、功能性验证测试
搭建模拟系统测试软油囊的实际工作性能:
- 循环充放测试(≥1000次充放循环)
- 快速泄压测试(验证防爆裂设计有效性)
- 介质相容性测试(接触燃油/润滑油后的材料稳定性)
- 环境适应性测试(-50℃至+80℃温度交变试验)
五、检测新技术应用
随着技术进步,工业CT扫描可实现三维结构重建,精准定位内部缺陷;红外热成像技术可实时监测油囊工作时的温度分布;基于机器视觉的自动化检测系统可提升表面异常识别效率。这些技术大幅提高了检测精度,将平均故障检出率提升至99.7%以上。
通过上述多维度的检测项目,不仅能有效预防软油囊失效事故,还可建立全生命周期数据库,为优化产品设计提供数据支撑。建议使用单位建立定期检测制度,结合在线监测系统,构建完整的油囊健康管理体系。
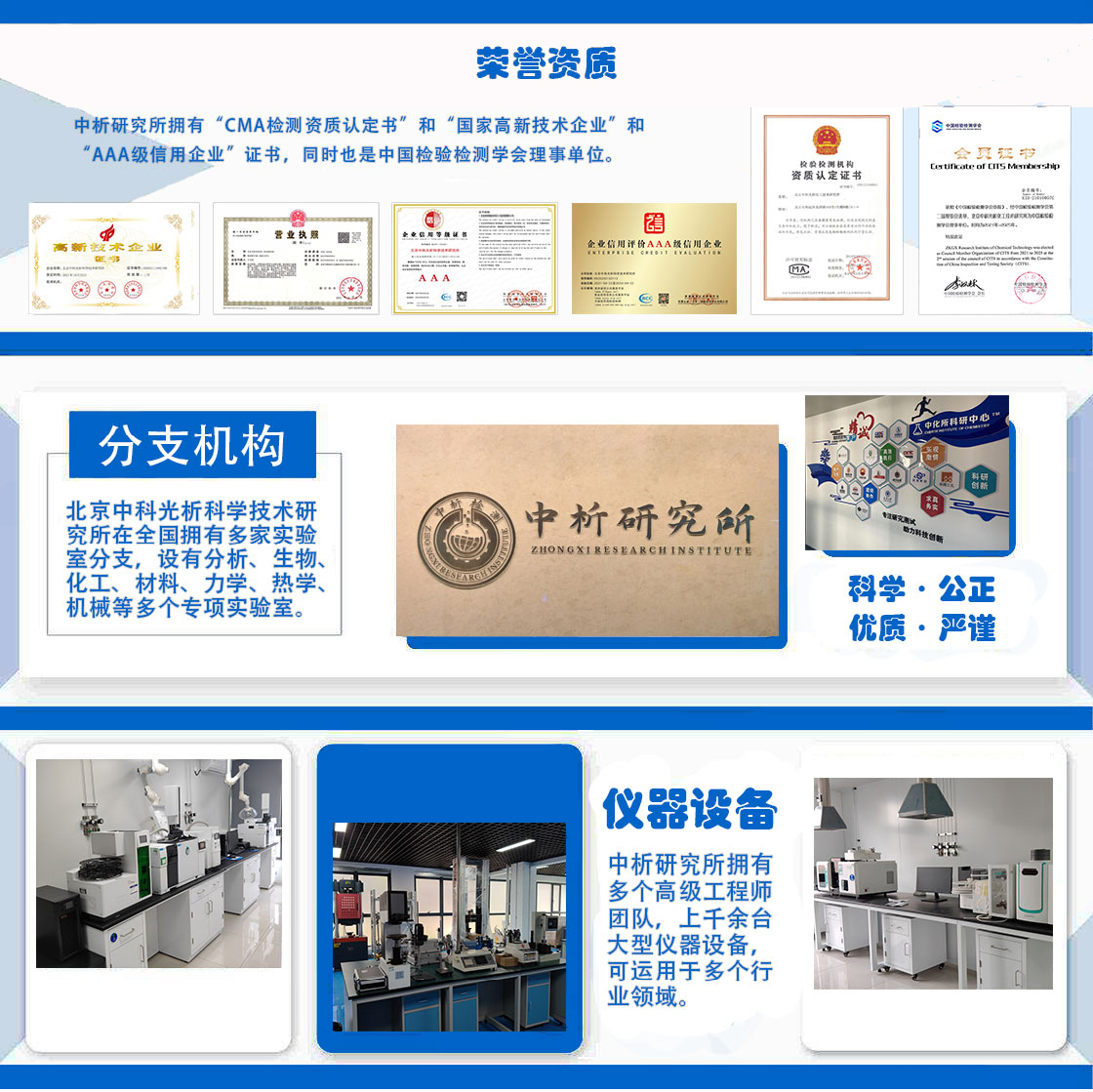
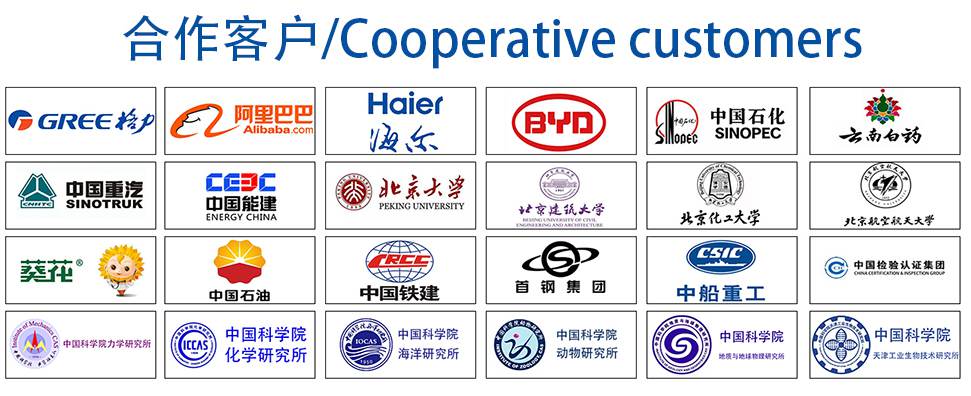