工程机械 高温低压输油管检测
实验室拥有众多大型仪器及各类分析检测设备,研究所长期与各大企业、高校和科研院所保持合作伙伴关系,始终以科学研究为首任,以客户为中心,不断提高自身综合检测能力和水平,致力于成为全国科学材料研发领域服务平台。
立即咨询工程机械高温低压输油管检测的重要性
在工程机械领域,输油管道作为动力传输的核心部件,其运行状态直接影响设备性能与作业安全。高温低压输油管因其特殊工况,长期承受温度波动、介质腐蚀和机械振动等多重压力,容易产生裂纹、磨损、渗漏等隐患。据统计,工程机械故障中约35%与液压系统相关,而输油管问题占比高达60%以上。尤其在高温(80-120℃)与低压(0.3-0.8MPa)的复合工况下,管道材料易发生蠕变、氧化,密封件加速老化,这些问题若未及时检测,可能导致设备停机、油液污染甚至火灾事故。
核心检测项目与技术方法
1. 管道外观与结构完整性检测
采用高分辨率工业内窥镜对管道内壁进行可视化检测,结合激光扫描技术测量管壁厚度变化。同步使用红外热成像仪捕捉异常温区,定位潜在热点。针对法兰连接处,实施磁粉探伤以发现微裂纹,检测精度可达0.1mm级。
2. 密封性能与承压能力测试
通过动态压力循环试验系统模拟实际工况,以1.25倍工作压力进行保压测试,持续时间不少于30分钟。采用氦质谱检漏法检测密封性,灵敏度可达1×10⁻⁹Pa·m³/s。对低压段管道特别设计负压检测方案,验证其在真空状态下的结构稳定性。
3. 材料性能退化分析
运用金属光谱仪对管材成分进行无损检测,对比原始材质数据。通过显微硬度计测试材料硬度变化,结合金相分析判断晶间腐蚀程度。针对高温导致的橡胶密封件老化问题,实施邵氏硬度测试与压缩永久变形率测定。
4. 智能监测系统集成
部署分布式光纤传感网络,实时监测管道应变与温度分布。采用无线振动传感器采集机械振动频谱,通过AI算法识别异常频率特征。开发数字孪生模型,实现剩余寿命预测与预防性维护决策支持。
创新检测技术应用趋势
当前行业内正加速推进无人机搭载多光谱相机的空中巡检系统,配合5G传输实现大范围管线快速筛查。纳米磁性标记技术的应用可将检测灵敏度提升3个数量级,而太赫兹波检测设备则能穿透多层包覆层精准识别内部缺陷。这些技术的融合应用正在重构工程机械管道的检测范式。
检测后的维护策略建议
基于检测数据建立分级预警机制:对于轻度腐蚀(壁厚损失<10%)管道实施防腐涂层修复;中度损伤(10%-30%)采用复合材料缠绕补强;重度缺陷(>30%)必须立即更换。建议每500工作小时进行常规检测,极端工况下检测周期缩短至200小时,并建立全生命周期电子档案实现可追溯管理。
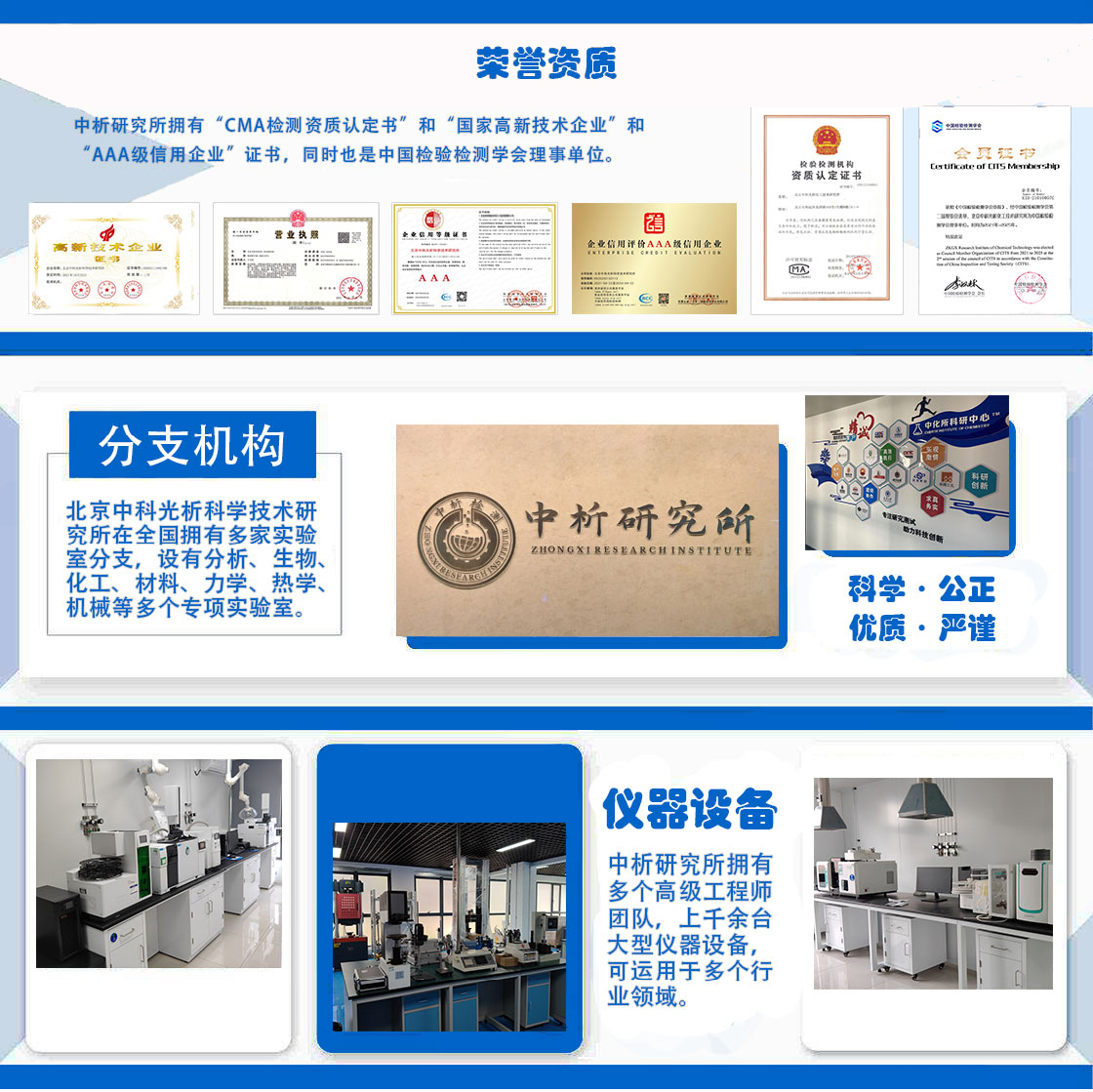
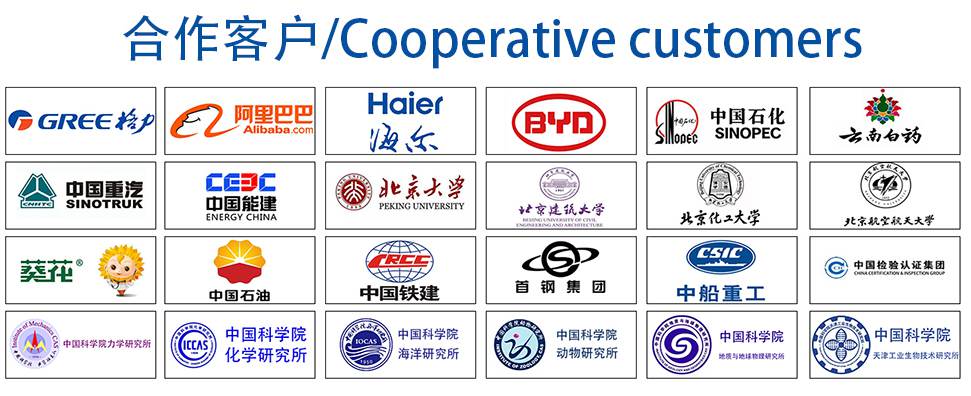