橡胶软管及软管组合件钢丝编织增强液压型检测项目解析
橡胶软管及软管组合件作为液压系统中的核心传输元件,其性能直接关系到设备的安全性、稳定性和使用寿命。针对油基或水基流体适用的钢丝编织增强液压型软管,需通过严格的检测确保其满足耐压性、耐介质腐蚀性、抗疲劳性等关键指标。此类软管广泛应用于工程机械、矿山设备、船舶液压系统等领域,检测过程需依据国家标准(如GB/T 3683、GB/T 5563)或国际标准(如ISO 1436、SAE J517),结合实际工况制定全面测试方案。
关键检测项目及测试方法
1. **耐压性能测试**:通过静压试验验证软管在额定工作压力下的密封性和抗变形能力,通常需施加1.5倍额定压力并保压5分钟,观察是否出现渗漏或鼓包。
2. **脉冲疲劳试验**:模拟实际液压系统压力波动场景,采用高频交变压力(最高可达爆破压力的70%)进行百万次循环测试,评估软管抗疲劳老化能力。
3. **耐流体兼容性测试**:将软管分别浸泡于油基(如HLP46液压油)和水基(HFC乳化液)介质中,在70℃环境下持续168小时,检测体积变化率、硬度变化及表面龟裂情况。
4. **爆破压力测试**:逐步加压至软管爆破,验证其极限承压能力是否达到标准规定的爆破压力系数(通常为4倍工作压力)。
5. **钢丝编织层强度检测**:通过金相分析、拉伸试验等手段评估钢丝层覆盖率、编织角度及单丝抗拉强度,确保增强层对橡胶主体的有效支撑。
辅助检测与质量控制
1. **尺寸公差检测**:使用激光测径仪精确测量内径、外径及壁厚偏差,控制公差在±0.3mm范围内。
2. **低温弯曲试验**:将软管置于-40℃环境中冷冻24小时后,在直径2倍于软管外径的芯轴上弯曲180°,检验低温脆化风险。
3. **臭氧老化试验**:在50pphm臭氧浓度、40℃环境下暴露96小时,评估橡胶层抗臭氧龟裂能力。
4. **接头附着力测试**:采用专用夹具对软管与金属接头进行轴向拉力测试,确保附着力不低于标准规定值(通常≥4kN)。
检测结果分析与应用
所有检测数据需形成完整的测试报告,重点关注压力-形变曲线、介质兼容性参数及疲劳寿命曲线。对于油基流体工况,需额外关注橡胶溶胀率(应≤10%);水基环境则需强化耐水解性能检测。通过多维数据交叉验证,可准确评估软管在复杂工况下的适用性,为液压系统选型提供科学依据。
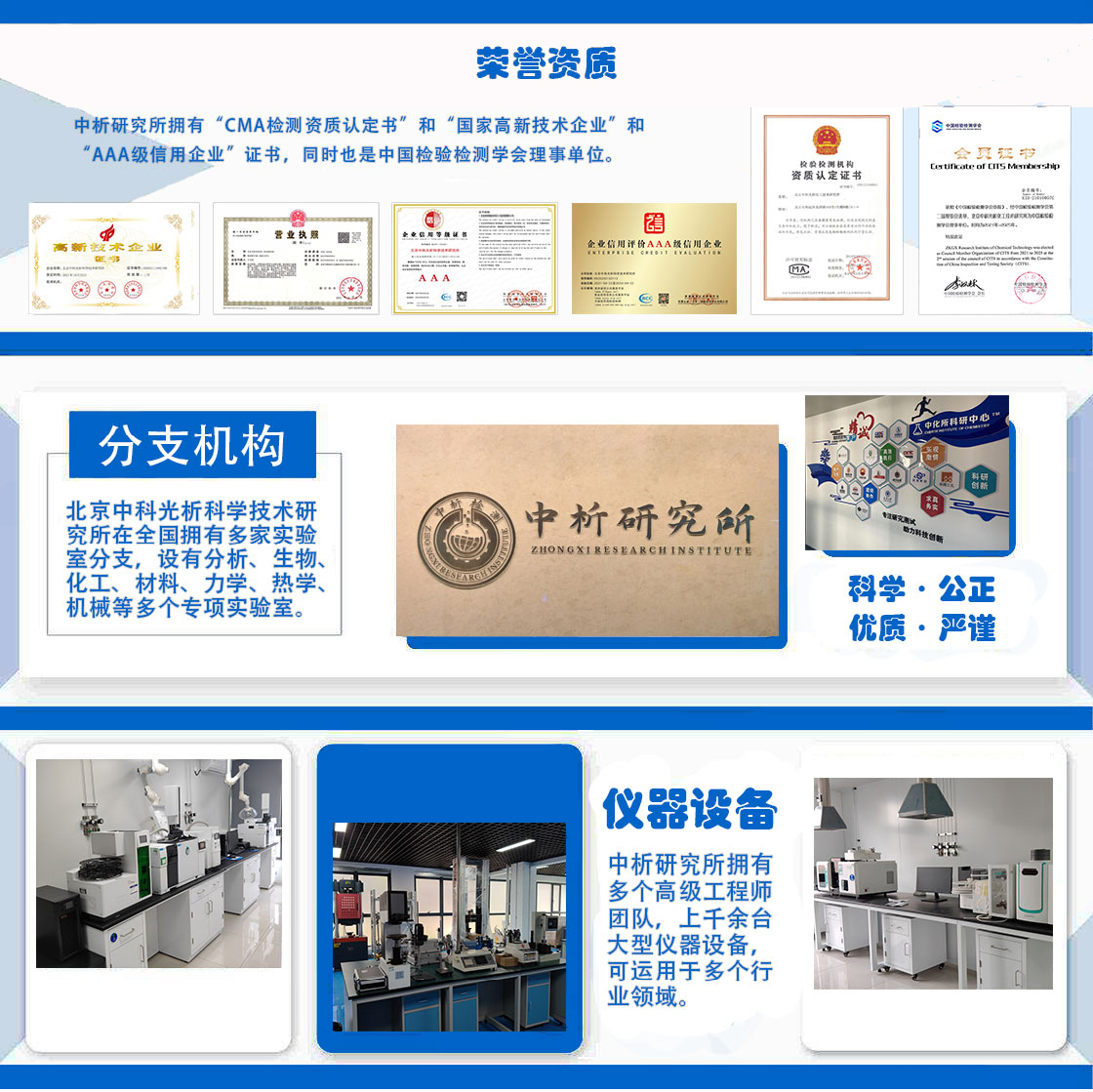
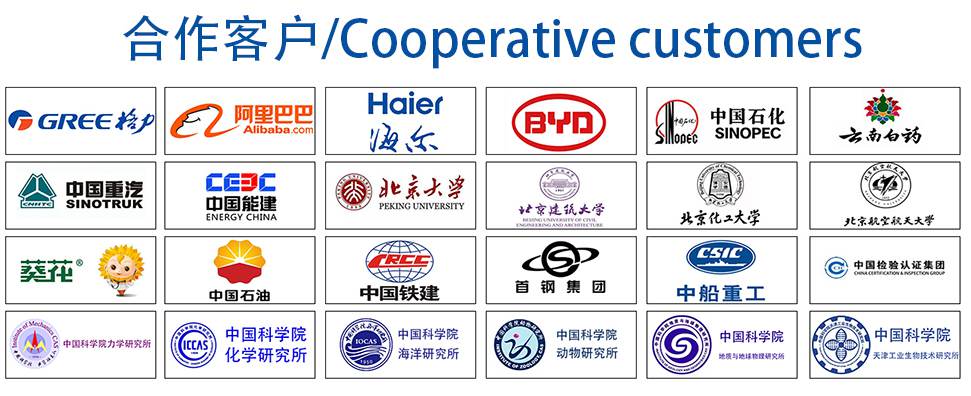