实验室用自动化电气设备检测的重要性与核心要素
随着工业4.0和智能制造的快速发展,实验室用自动化电气设备已成为科研、生产及质量控制中不可或缺的工具。这类设备通过集成传感器、控制器和执行机构,显著提升了实验效率与数据精度。然而,其复杂性和高集成度也带来了潜在风险,例如电气安全、功能稳定性以及环境适应性等问题。为确保设备长期可靠运行并满足行业标准,系统化的检测项目成为实验室管理体系的核心环节。通过科学的检测流程,不仅能验证设备性能,还能预防因硬件故障或软件异常导致的实验偏差,从而保障科研数据的准确性与可重复性。
自动化电气设备的核心检测项目
自动化电气设备的检测需覆盖硬件、软件及环境适配性等多维度。以下是实验室场景中常见的核心检测项目:
1. 电气安全性能检测
包括绝缘电阻测试、接地连续性验证及漏电流检测,确保设备符合IEC 61010-1或GB 4793.1等安全标准。通过高压测试仪和接地电阻仪量化评估风险,预防触电或短路事故。
2. 功能与性能验证
针对设备预设功能进行全流程测试,例如运动控制精度(重复定位误差≤0.01mm)、信号采集速率(如1MS/s采样率达标验证)以及通信协议兼容性测试(MODBUS、Profinet等)。需结合标准样件或模拟负载完成动态性能标定。
3. 环境适应性评估
依据GB/T 2423系列标准,开展温度循环(-20℃~70℃)、湿度(95%RH)、振动(5Hz~500Hz)及EMC抗扰度测试,验证设备在极端工况下的可靠性。重点监测温漂对传感器精度的影响及结构件的疲劳寿命。
4. 软件与控制系统检测
对PLC程序、HMI界面及数据管理软件进行黑盒/白盒测试,包括逻辑正确性验证、异常处理机制测试及网络安全防护评估(如IEC 62443合规性)。需模拟断网、数据溢出等故障场景检验系统鲁棒性。
5. 数据记录与追溯能力测试
通过注入模拟信号验证设备的数据采集完整性,并检查时间戳同步精度(≤1ms)、存储格式兼容性(CSV/TDMS)及审计追踪功能是否符合21 CFR Part 11等法规要求。
检测流程的质量控制
实验室需建立三级检测体系:设备入场初检、周期性维护检测及故障后专项检测。所有检测数据应录入LIMS系统并生成趋势分析报告,结合SPC工具实现预防性维护。检测人员需通过ISO/IEC 17025资质认证,且检测设备需定期溯源至国家计量基准。
典型应用场景与案例分析
以某生物制药实验室的自动化培养箱检测为例,通过温度均匀性测试(±0.5℃)、CO2浓度控制精度(±1%)及灭菌程序验证,成功将细胞培养污染率从2.3%降至0.15%。此案例凸显了系统化检测对实验成功率的提升作用。
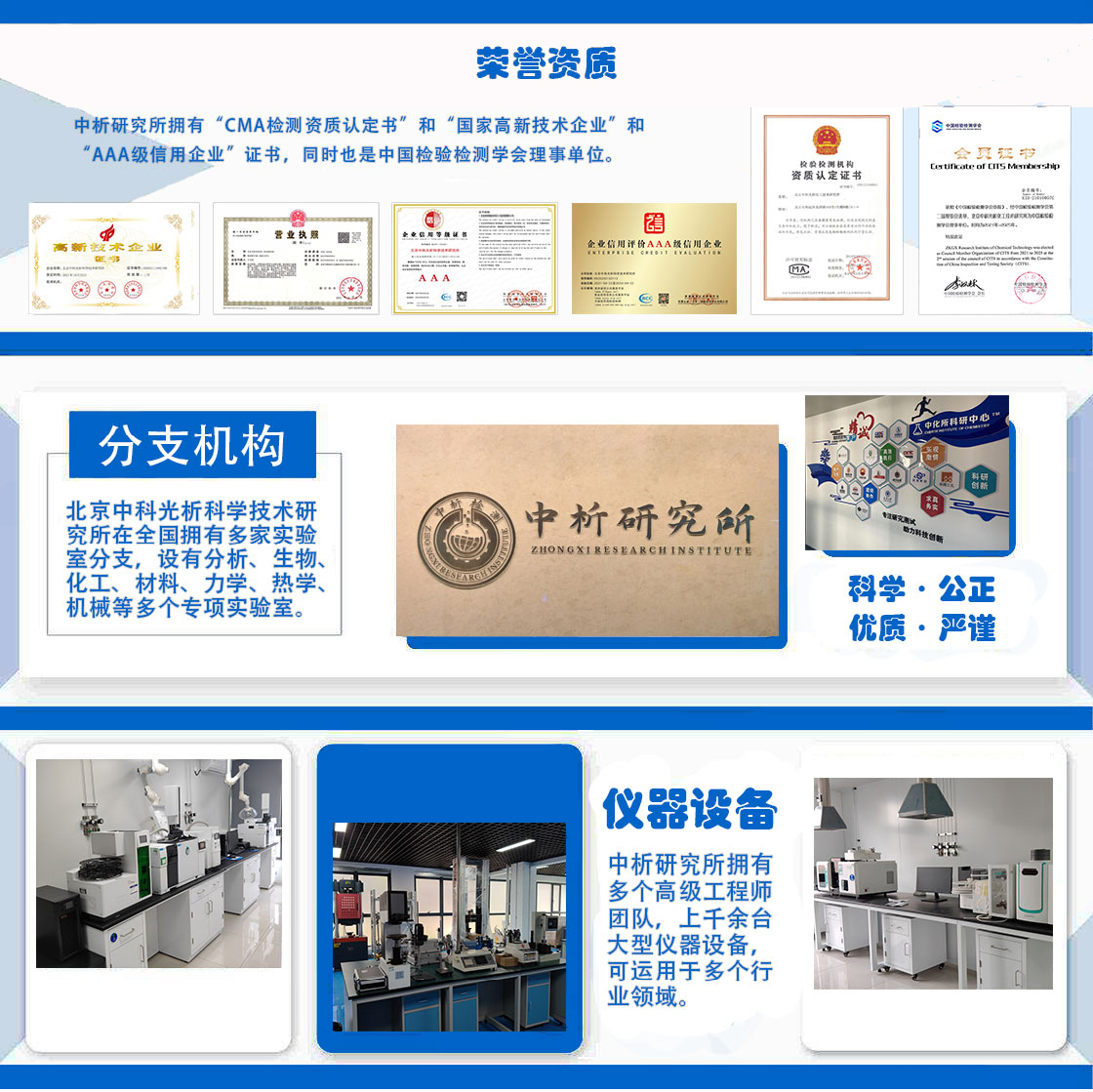
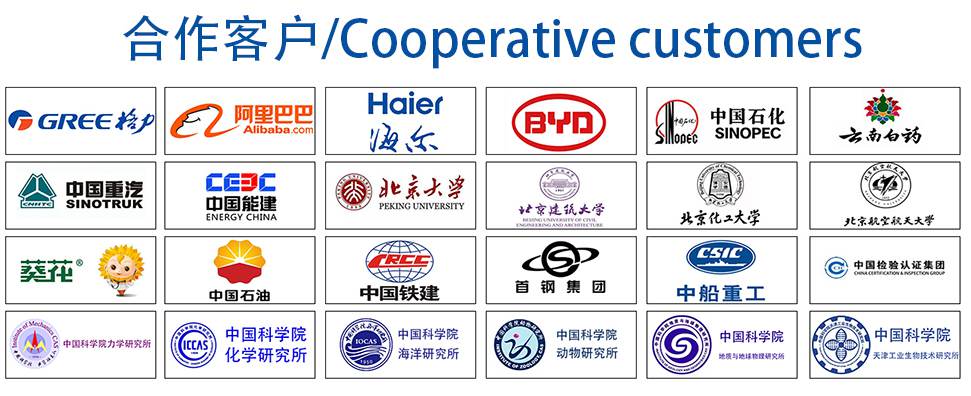