机器人设备检测的关键技术与应用场景
随着工业4.0和智能制造的快速发展,机器人设备已成为生产制造、医疗健康、仓储物流等领域的核心工具。机器人设备检测作为保障其安全性和可靠性的关键环节,涉及从硬件性能到软件算法的全方位验证。通过系统化的检测流程,不仅能有效预防设备故障,还能优化工作效率,降低维护成本。根据国际标准化组织(ISO)及行业规范要求,机器人检测需覆盖机械结构、电气系统、运动控制、环境适应性等20余项核心指标,确保其在复杂工况下的稳定运行。
硬件系统检测项目
机器人硬件检测包含机械结构强度测试、关节传动效率分析和传感器精度校准三大模块。采用三维激光扫描技术对机械臂进行形变测量,误差需控制在0.05mm以内;通过扭矩传感器实时采集各关节输出数据,验证传动系统是否达到设计标准。核心传感器(如视觉相机、力觉反馈装置)需经历超过200小时的连续工作测试,确保其在电磁干扰、温湿度变化等环境下的稳定性。
软件控制系统检测
在软件层面,重点检测运动控制算法的响应速度和轨迹规划精度。基于ROS(机器人操作系统)搭建模拟测试平台,通过注入故障信号验证异常处理机制的有效性。针对协作型机器人,需特别测试人机交互系统的安全防护功能,包括接触力监测阈值设定(通常≤150N)和急停反应时间(要求<0.3秒)。采用代码静态分析和动态仿真相结合的方式,可发现98%以上的逻辑漏洞和潜在风险。
环境适应性测试体系
依据GB/T 2423系列标准,机器人需经受极端环境考验:在-20℃至60℃温箱中循环测试48小时,验证热管理系统的可靠性;通过振动频率5-2000Hz的随机振动试验,模拟运输和使用过程中的机械冲击。针对特殊应用场景(如防爆场所),还需通过IP68防护等级认证和Ex防爆认证,确保设备在粉尘、油污、可燃气体环境中的安全运行。
安全性能综合评估
安全检测涵盖电气安全、功能安全、网络安全三个维度。使用绝缘电阻测试仪(500V DC)测量带电部件与外壳间阻值(要求>100MΩ),通过接地连续性测试验证漏电防护能力。针对工业通信协议(如PROFINET、EtherCAT),需进行网络渗透测试和数据加密验证,预防恶意攻击导致的系统瘫痪。最终检测报告需包含12类安全参数,其中9项为强制性认证指标。
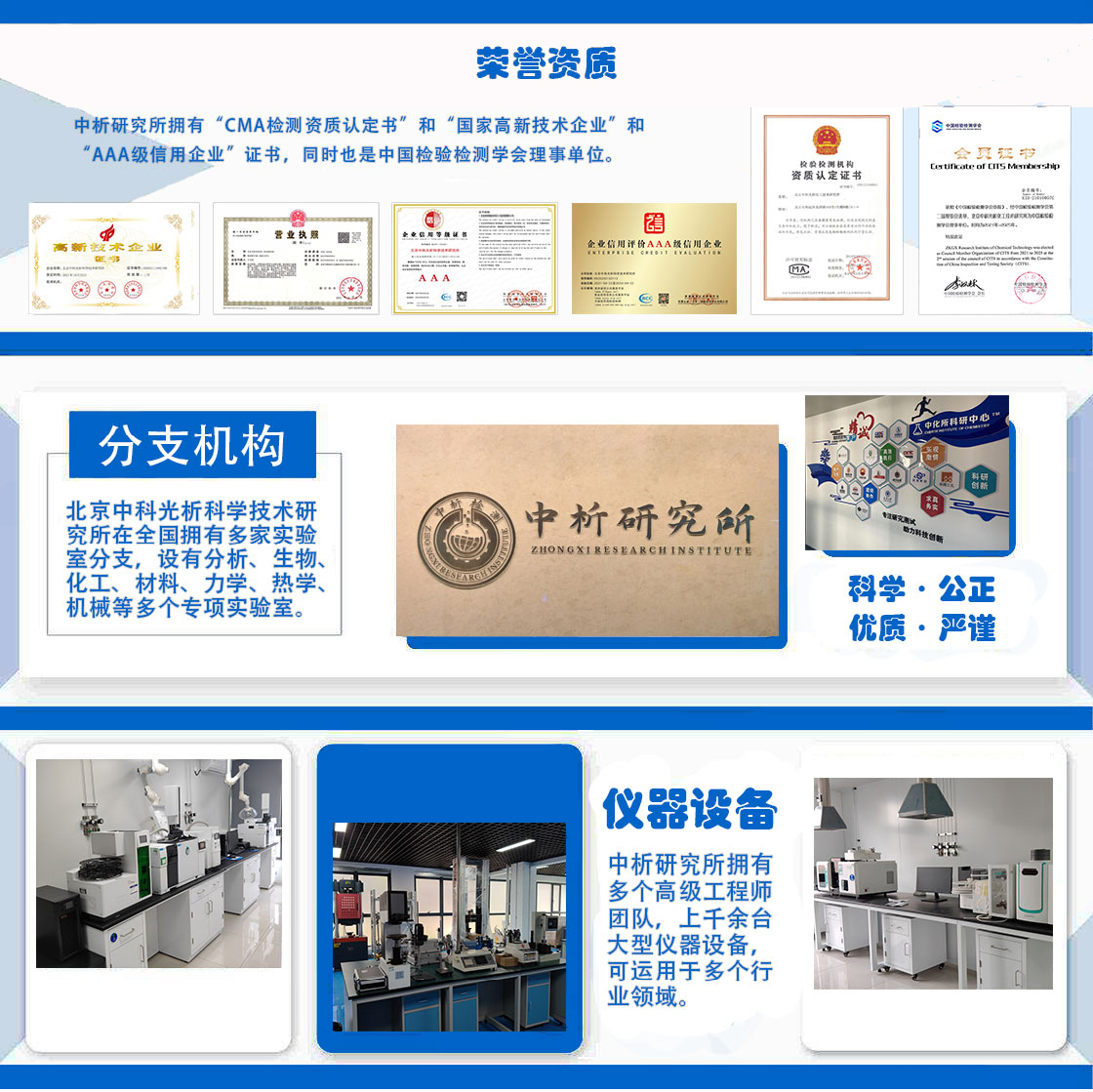
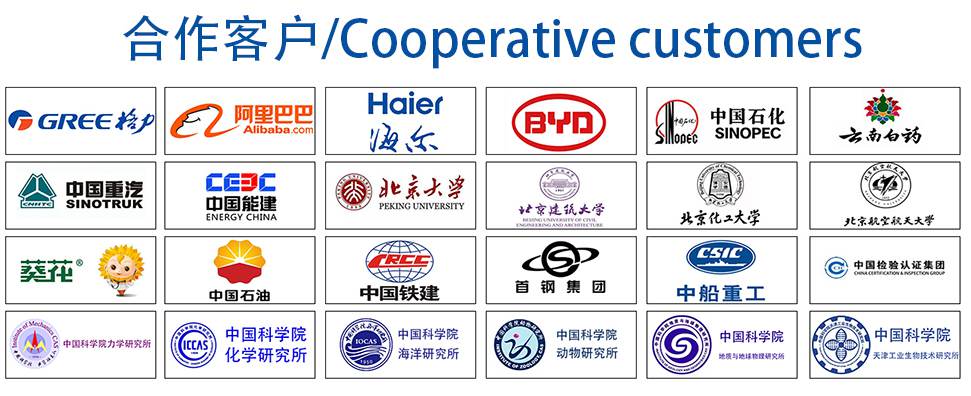