自行车车把检测的重要性与核心内容
自行车车把作为操控车辆的核心部件,其质量直接关系到骑行者的安全性和舒适性。近年来,随着自行车运动普及和共享单车的快速发展,车把检测已成为生产制造和质量监管的关键环节。根据行业统计,约15%的自行车事故与车把结构缺陷或疲劳损伤相关。因此,通过科学系统的检测项目,精准评估车把的机械性能、耐久性和安全性,成为保障用户生命安全的重要技术手段。
关键检测项目详解
1. 材料强度测试
采用万能材料试验机对车把本体进行拉伸、压缩和扭转测试,检测铝合金/碳纤维复合材料的抗拉强度(需达到ISO 4210标准要求的≥350MPa)、屈服强度和延伸率。重点评估焊接部位的微观结构,通过金相分析检测是否存在气孔或夹渣缺陷。
2. 尺寸精度验证
使用三坐标测量仪进行三维尺寸检测,包括把横直径(标准值22.2±0.2mm)、把立安装孔间距(通常为40/31.8mm规格)及角度公差(±0.5°)。特别关注内走线车把的线管通道尺寸,确保直径≥5mm且内壁光滑度Ra≤3.2μm。
3. 表面处理检测
通过盐雾试验箱模拟恶劣环境,检测阳极氧化层或喷漆涂层的耐腐蚀性能(需通过96小时中性盐雾测试)。使用划格法测试涂层附着力,要求达到ASTM D3359标准B级以上的剥离强度。
4. 动态疲劳测试
在伺服液压疲劳试验机上模拟10万次以上骑行负载(垂直载荷500N±20%,水平扭矩50Nm)。检测过程中持续监测应力集中区域的裂纹扩展情况,确保疲劳寿命符合EN 14764标准要求。
5. 安全性能检测
包括把套防滑测试(扭转力矩≥15Nm)、边缘锐度检查(R角≥0.5mm)以及极端负载测试(施加3倍额定载荷保持60秒无永久变形)。对折叠车把还需进行5000次开合循环测试,检测铰链机构的磨损情况。
6. 环境适应性验证
在-20℃至60℃温度箱中进行热循环试验,检测不同温湿度条件下车把的尺寸稳定性。针对电动助力车把,额外进行电磁兼容性测试(EMC)和振动耐久性试验(频率10-500Hz,加速度5g)。
检测技术发展趋势
当前行业正逐步引入X射线断层扫描(CT)检测内部缺陷,采用光纤光栅传感器实时监测应力分布。部分实验室开始建立数字孪生模型,通过有限元分析预测车把的疲劳寿命。随着ISO 20957新版标准的实施,对车把的检测项目已新增5项数字化评价指标。
完善的自行车车把检测体系,不仅需要齐全的设备支持,更依赖专业工程师对检测数据的深度解读。建议生产商建立全流程质量追溯系统,将原材料检测、过程检验和成品测试数据进行关联分析,从根本上提升产品可靠性。
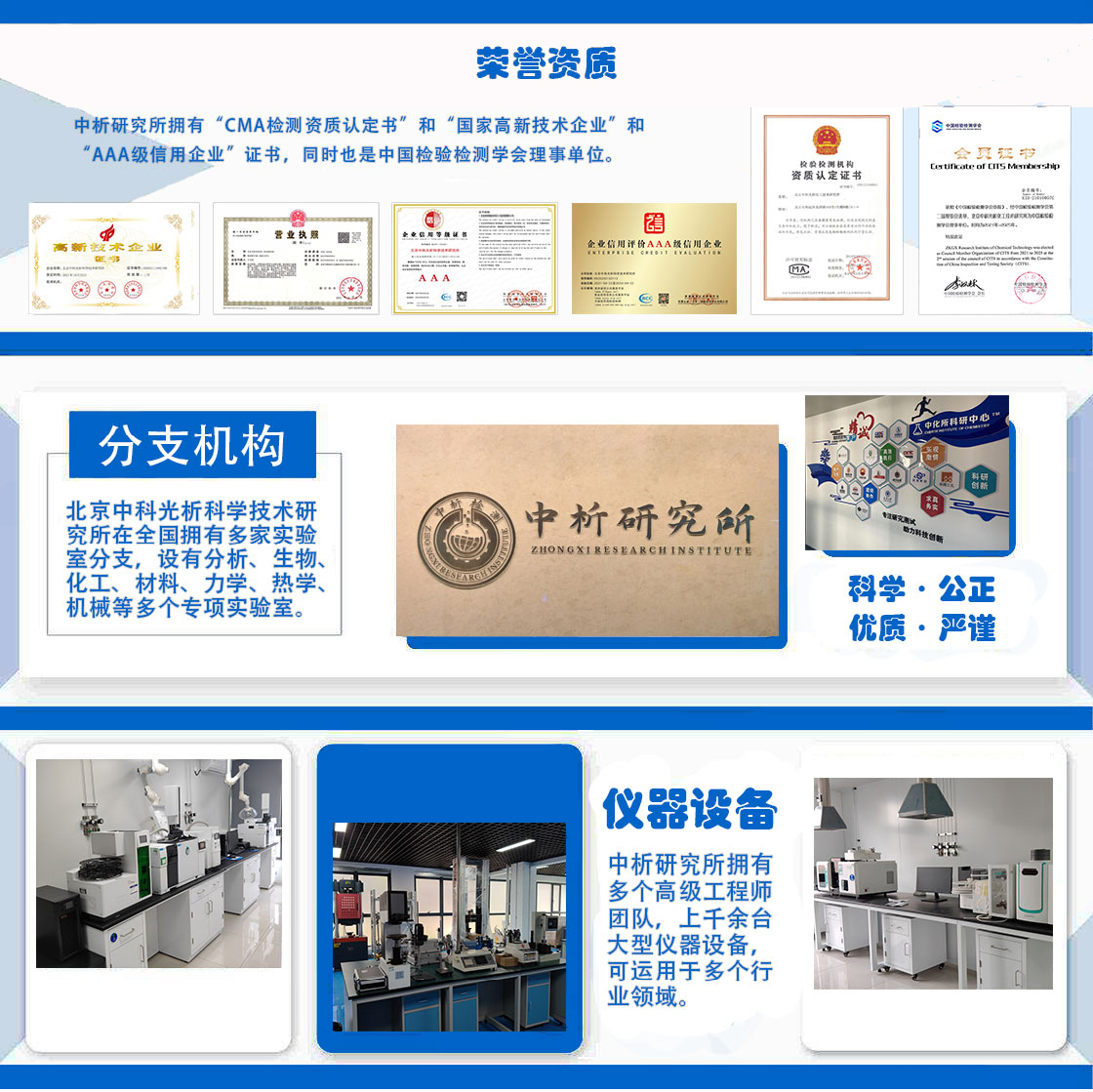
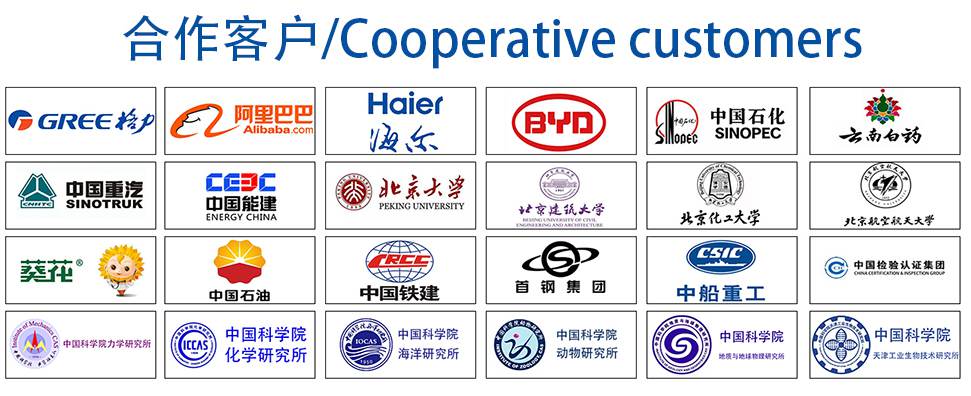