自行车钢球检测的重要性与核心项目解析
在自行车制造与维修领域,钢球作为轴承系统的核心组件,直接关系到车轮、中轴、脚踏等关键部位的运转性能。一颗直径仅3-6mm的钢球若存在缺陷,可能导致轴承异响、卡顿甚至早期失效,严重影响骑行安全与体验。行业数据显示,约23%的自行车故障可追溯至轴承质量问题,而钢球则是轴承故障链的起始环节。因此,通过系统化检测确保钢球符合ISO 3290、GB/T 308等国际国内标准,已成为整车厂与配件供应商质量控制的重中之重。
核心检测项目与技术规范
1. 尺寸精度检测
采用高精度光学投影仪(分辨率0.1μm)或三坐标测量机,对钢球直径公差(通常要求±0.001mm)、真球度(Roundness≤0.08μm)进行全数检验。特殊应用场景需额外检测表面波纹度(Waviness),避免高频振动引发异响。
2. 表面缺陷筛查
通过60倍工业显微镜或自动视觉检测系统,识别划痕、凹坑、锈斑等表面异常。依据JIS B 1501标准,允许的单个缺陷面积不超过总表面积的0.05%,且深度不大于0.002mm。磁性探伤法可同步检测内部微裂纹。
3. 硬度与韧性测试
使用洛氏硬度计(HRC标尺)多点检测,确保硬度值稳定在58-64HRC区间。通过落锤冲击试验(100g砝码/0.5m高度)验证抗碎裂性能,连续冲击10次无破损方为合格。
4. 材料成分分析
采用光谱仪对GCr15轴承钢进行元素检测,重点控制碳含量(0.95-1.05%)、铬含量(1.30-1.65%),硫、磷杂质需低于0.025%。X射线衍射法可验证热处理后奥氏体残留量是否≤3%。
5. 耐腐蚀性能验证
盐雾试验箱模拟海洋气候环境(5%NaCl溶液/35℃),持续96小时测试后表面锈蚀面积需<0.5%。对于高端车型,需通过200小时循环腐蚀试验(CCT)验证长效防护能力。
6. 动态载荷测试
专用疲劳试验机模拟实际工况,以2000rpm转速、5kN动态载荷进行100万次循环测试,磨损量应<0.003mm,且无剥落、点蚀现象。测试后需复测尺寸精度与表面粗糙度(Ra≤0.05μm)。
综合质量控制的意义
通过上述6大维度20余项指标的严格检测,可将钢球失效概率降低至0.003%以下。结合SPC统计过程控制,不仅能提升轴承组件10万公里使用寿命,更可减少整车厂30%的售后索赔成本。随着电动自行车、公路赛车等细分市场对精度要求的提升,智能化检测设备与AI缺陷识别技术的应用正成为行业新趋势。
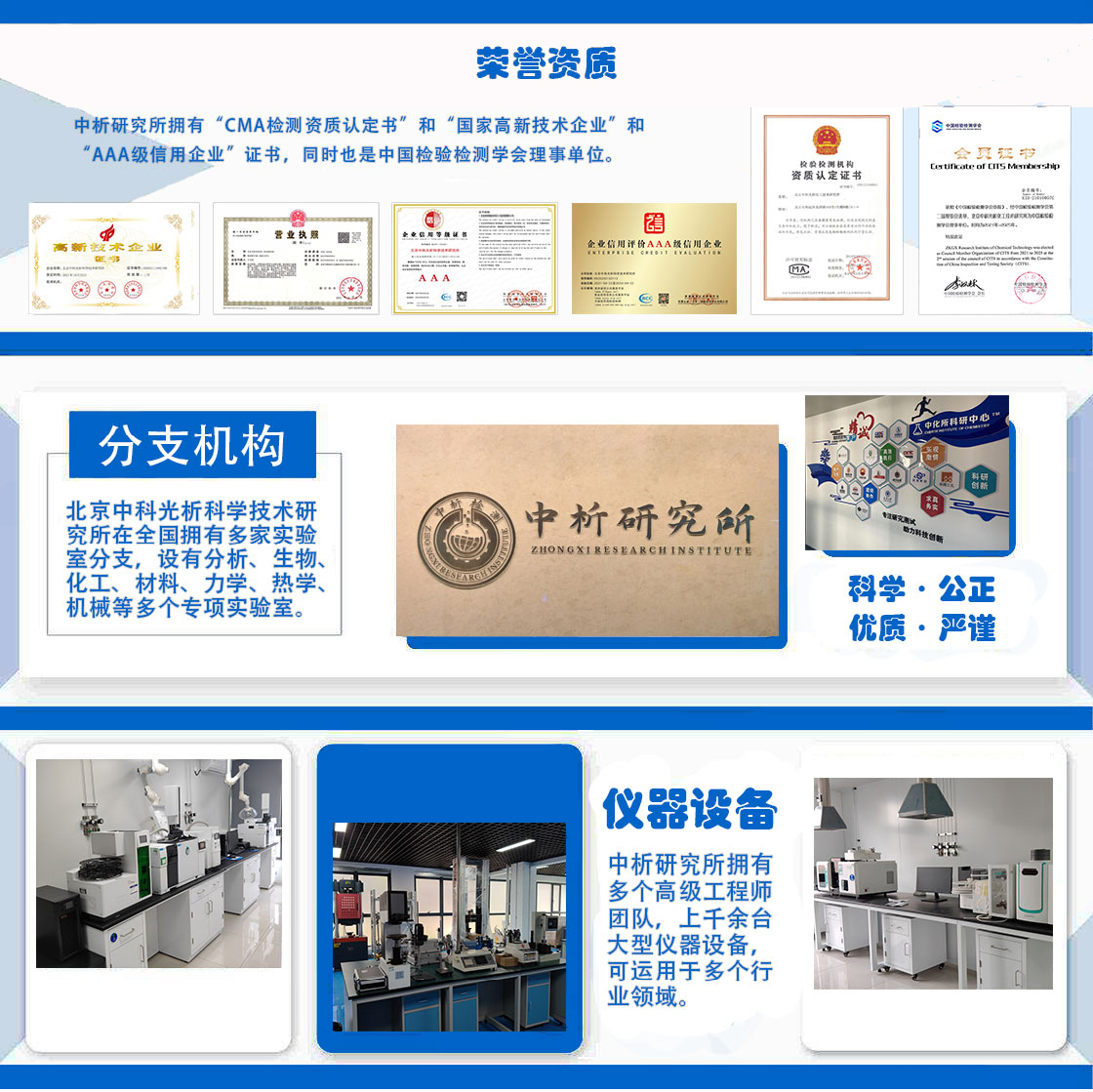
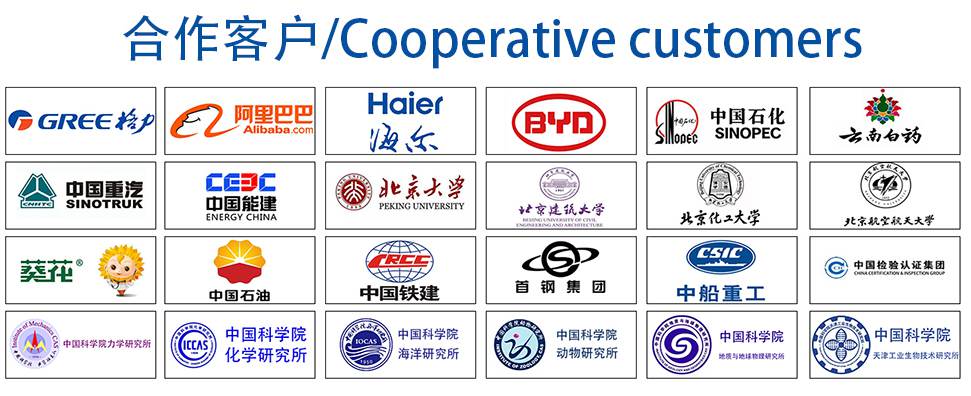