金属配件检测的重要性与应用领域
金属配件作为工业制造中的基础元件,广泛应用于机械、汽车、航空航天、电子设备及建筑等领域。其性能与质量直接关系到产品的安全性、可靠性和使用寿命。在复杂的工况环境中,金属配件需承受高温、高压、腐蚀、磨损等多种考验,因此必须通过科学严谨的检测手段确保其符合设计要求和行业标准。金属配件检测不仅涉及材料成分分析,还包括物理性能测试、尺寸精度检验、表面缺陷筛查等多个维度,是保障产业链质量安全的重要环节。
核心检测项目与技术要求
1. 物理性能检测
物理性能检测是金属配件质量控制的核心环节,主要包括拉伸试验、硬度测试、冲击韧性试验等。通过拉伸试验可获取材料的抗拉强度、屈服强度和延伸率等关键指标;硬度测试(如布氏、洛氏、维氏硬度)可评估材料的耐磨性与抗变形能力;冲击韧性试验则用于模拟配件在极端条件下的抗断裂性能。这些数据为材料选型和工艺优化提供科学依据。
2. 化学成分分析
采用光谱分析仪(如直读光谱仪)、X射线荧光光谱仪(XRF)等设备对金属配件进行元素定量检测,确保材料成分符合GB/T、ASTM、ISO等标准要求。尤其需关注碳、硫、磷等元素的含量,这些元素直接影响材料的焊接性、耐腐蚀性和机械强度。
3. 尺寸与形位公差检测
通过三坐标测量机、光学投影仪、专用量具等对配件的关键尺寸、平面度、圆度、同轴度等进行精密测量。例如螺纹件的螺距精度、齿轮件的模数偏差等,需满足±0.01mm级的高精度要求,确保装配兼容性。
4. 表面质量与缺陷检测
结合目视检查、磁粉探伤、渗透探伤和涡流检测技术,识别表面裂纹、气孔、夹杂等缺陷。对于重要承力部件,需采用X射线或超声波探伤进行内部缺陷检测,缺陷深度超过标准允许值(如0.1mm)的配件必须剔除。
5. 耐腐蚀性能测试
通过盐雾试验、湿热循环试验等方法模拟不同环境下的腐蚀情况,评估镀层厚度(如锌层≥8μm)、氧化膜致密性等指标。特殊行业配件还需进行应力腐蚀开裂(SCC)敏感性测试。
智能化检测技术的发展趋势
随着工业4.0技术的普及,金属配件检测逐步向自动化、数字化方向升级。机器视觉系统可实现每分钟数百件的表面缺陷快速筛查;基于大数据的质量分析平台能实时监控生产波动;而3D扫描技术结合AI算法,可对复杂曲面配件进行全尺寸逆向验证,检测效率提升60%以上。这些技术创新正在重构金属制造行业的质量管理体系。
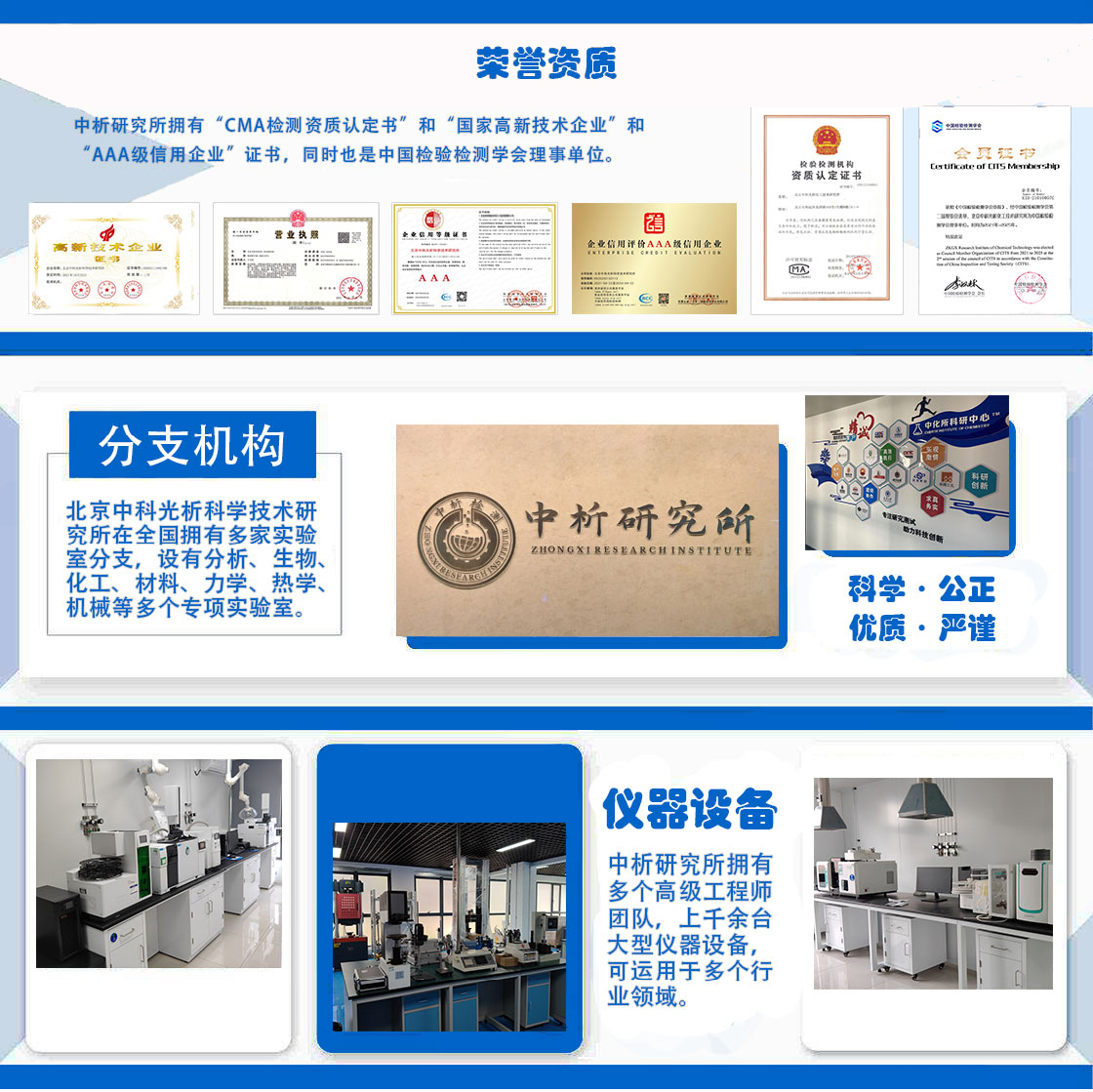
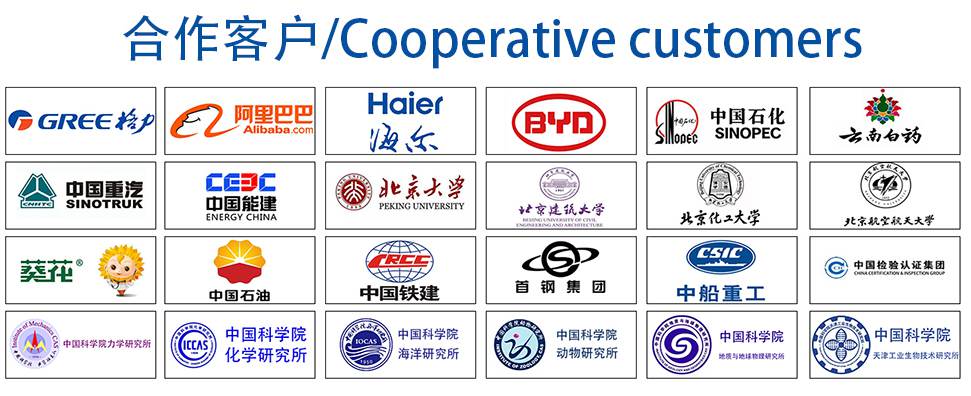