非专业用可视附件检测的核心内容与重要性
在工业制造、建筑工程及日常设备维护中,非专业用可视附件检测是保障设备安全性和功能完整性的重要环节。这类检测主要面向无需复杂仪器即可通过肉眼或简单工具观察的组件,其核心目标是快速识别表面缺陷、结构异常或使用痕迹。与专业检测相比,非专业检测更强调操作的简易性和结果的直观性,适用于日常巡检、初步故障排查或小规模维修场景。通过规范化的检测流程,可以有效降低因附件损坏导致的安全隐患,延长设备使用寿命。
外观完整性检测
作为基础检测项目,需重点检查附件表面是否存在裂纹、变形或腐蚀现象。例如金属部件的氧化锈蚀、塑料件的开裂老化等,使用放大镜可辅助观察细小微纹。同时需确认连接部位(如螺栓、卡扣)是否松动,接口处密封材料是否完整,避免因物理损伤引发功能失效。
尺寸匹配度验证
通过简易量具(如游标卡尺、卷尺)测量附件实际尺寸与设计参数的偏差。重点关注安装孔位间距、轴径公差等关键尺寸,允许误差范围需参照设备手册标准。特殊形状附件可采用对比模板法,快速判断形变程度是否符合使用要求。
功能性痕迹分析
观察附件表面磨损、划痕的分布规律,判断是否属于正常使用痕迹。如传动齿轮的齿面磨损是否对称均匀,轴承滚道是否出现异常凹坑。同时检查润滑介质残留状态,油污结焦或干涸可能预示润滑系统故障。
标识与材质辨识
核查附件铭牌信息(型号、规格、材质)是否清晰可辨,防止误用替代材料。通过磁铁吸附测试、断面颜色观察等方法进行基础材质判断。特殊环境下还需确认防腐蚀涂层、绝缘层的完整性,确保其防护功能有效。
环境适应性评估
针对设备运行环境,检查附件是否存在因温度、湿度变化导致的性能劣化。如橡胶密封圈硬化、电缆表皮龟裂等老化现象。同时排查附件周边是否存在污染物堆积、化学腐蚀痕迹等环境致损因素。
通过上述系统的非专业可视检测,操作人员可在早期阶段发现80%以上的典型附件问题。需要强调的是,发现异常情况时应及时记录并联系专业技术人员进行深度诊断,避免因不当处理引发二次损伤。
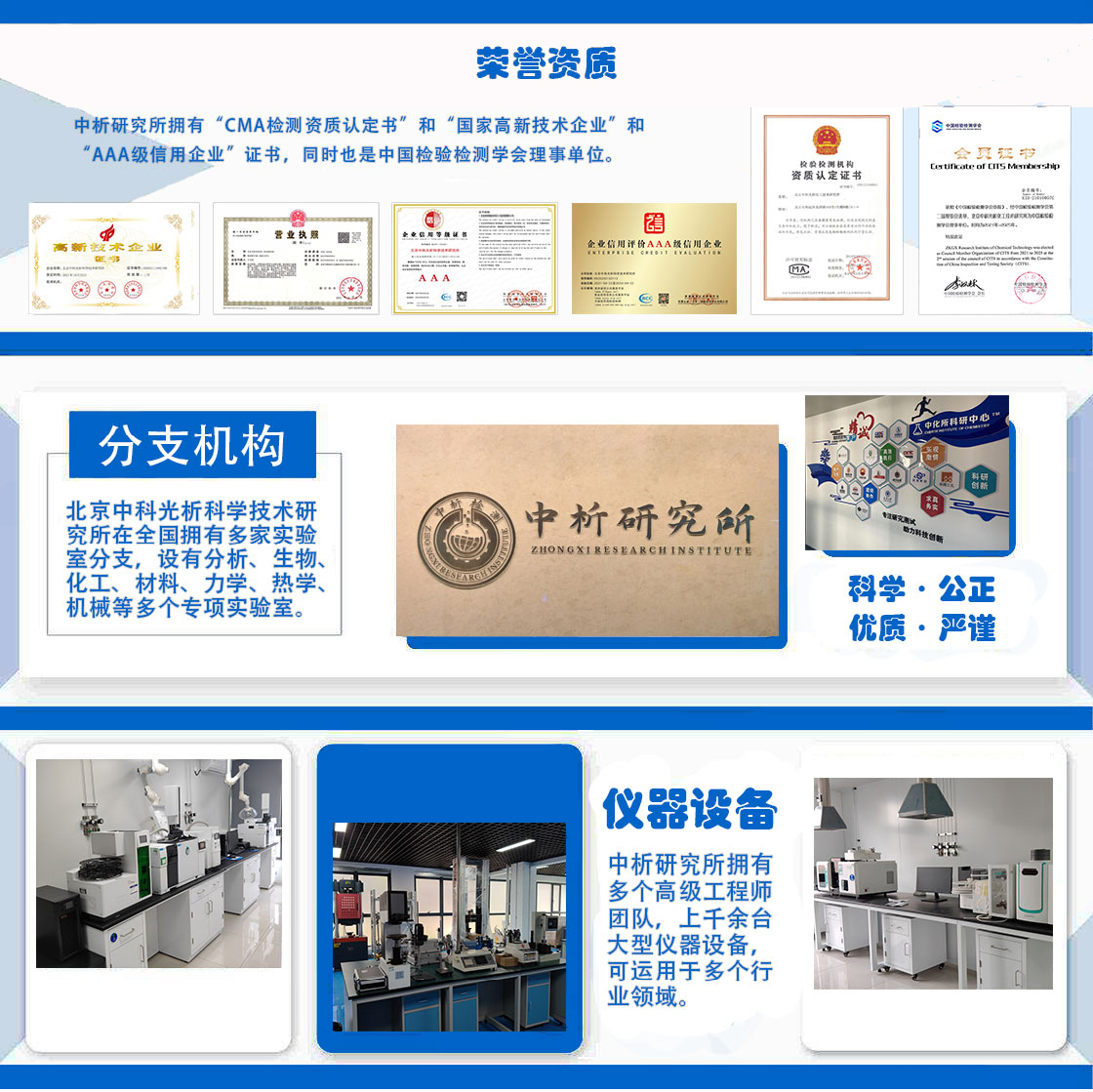
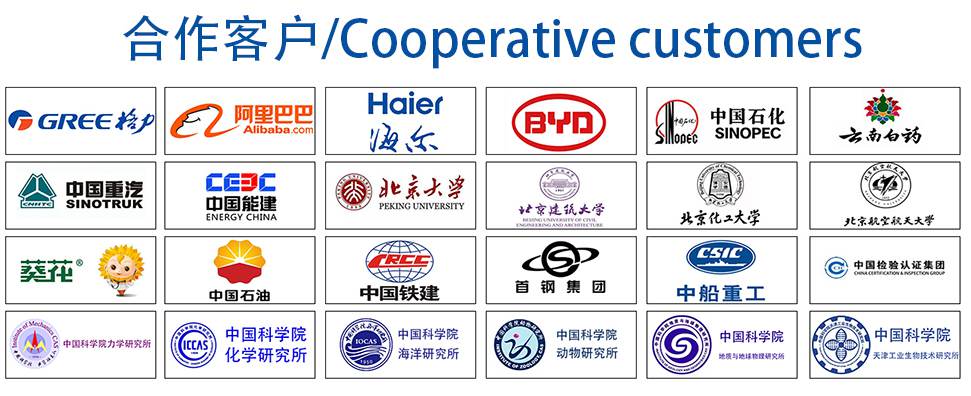