可燃气体报警控制器检测的重要性
可燃气体报警控制器是工业、民用场所中保障安全的关键设备,其核心功能是实时监测环境中可燃气体的浓度,并在达到预设阈值时触发报警及联动控制措施。随着石油化工、燃气输配、危化品仓储等领域的广泛应用,控制器的可靠性直接关系到人员生命和财产安全。然而,设备长期运行可能因传感器老化、电路故障或环境干扰导致性能下降。因此,定期开展专业检测是确保其功能有效性的必要手段。通过系统性检测,不仅能验证设备的基础参数,还能发现潜在风险,避免因误报、漏报引发的安全事故。
检测项目及标准要求
1. 外观与结构检查
检测人员需确认控制器外壳无破损、腐蚀现象,按键与指示灯功能正常。安装位置应符合GB 15322.1-2019要求,避免高温、潮湿或强电磁干扰环境。接线端子紧固性、标识清晰度以及防爆型设备的结构密封性均为重点检查内容。
2. 基本功能测试
包括电源切换(主备电自动转换)、故障自诊断、声光报警启动等功能的验证。需模拟主电源断电场景,测试备用电池续航时间是否≥8小时,并检查报警音量是否达到80dB以上(距设备1米处测量)。
3. 响应时间与报警精度
使用标准气体标定装置,向传感器通入50%LEL浓度的甲烷或异丁烷气体,测试控制器从气体接触到发出报警信号的时间,国标规定一级报警响应时间应≤30秒。同时需验证报警阈值偏差是否在±5%LEL范围内,确保浓度显示值的准确性。
4. 联动控制功能验证
检测报警时控制器是否能自动启动排风系统、关闭电磁阀或发送远程信号至监控中心。需通过模拟信号测试继电器输出状态,并记录执行机构的动作延迟时间(一般要求≤10秒)。
5. 抗干扰能力测试
在设备正常工作状态下,施加频率为1MHz~1GHz的电磁干扰,观察是否出现误报警。同时需测试高湿度(RH≥95%)、温度骤变(-20℃~+55℃循环)等极端环境下的运行稳定性。
6. 数据记录与通讯功能
检查控制器的事件存储容量,要求至少记录最近1000条报警、故障信息,并通过RS485或无线模块测试数据上传至上位机系统的完整性和实时性。历史数据导出功能需支持Excel或PDF格式。
检测周期与结果处理
根据AQ/T 3046-2013规范,建议每半年进行一次全面检测,新装设备需在运行72小时后进行首次校准。检测完成后应出具包含修正系数、传感器剩余寿命评估的详细报告,对不达标项须立即停用并更换核心元件。检测机构须持有CMA认证资质,确保检测结果的法定效力。
结语
可燃气体报警控制器的专业化检测是构建安全生产防线的重要环节。通过覆盖硬件、软件、环境的全方位检测体系,可显著降低爆炸事故风险。企业应建立完善的检测档案,结合智能监测平台实现设备全生命周期管理,切实提升气体泄漏防控能力。
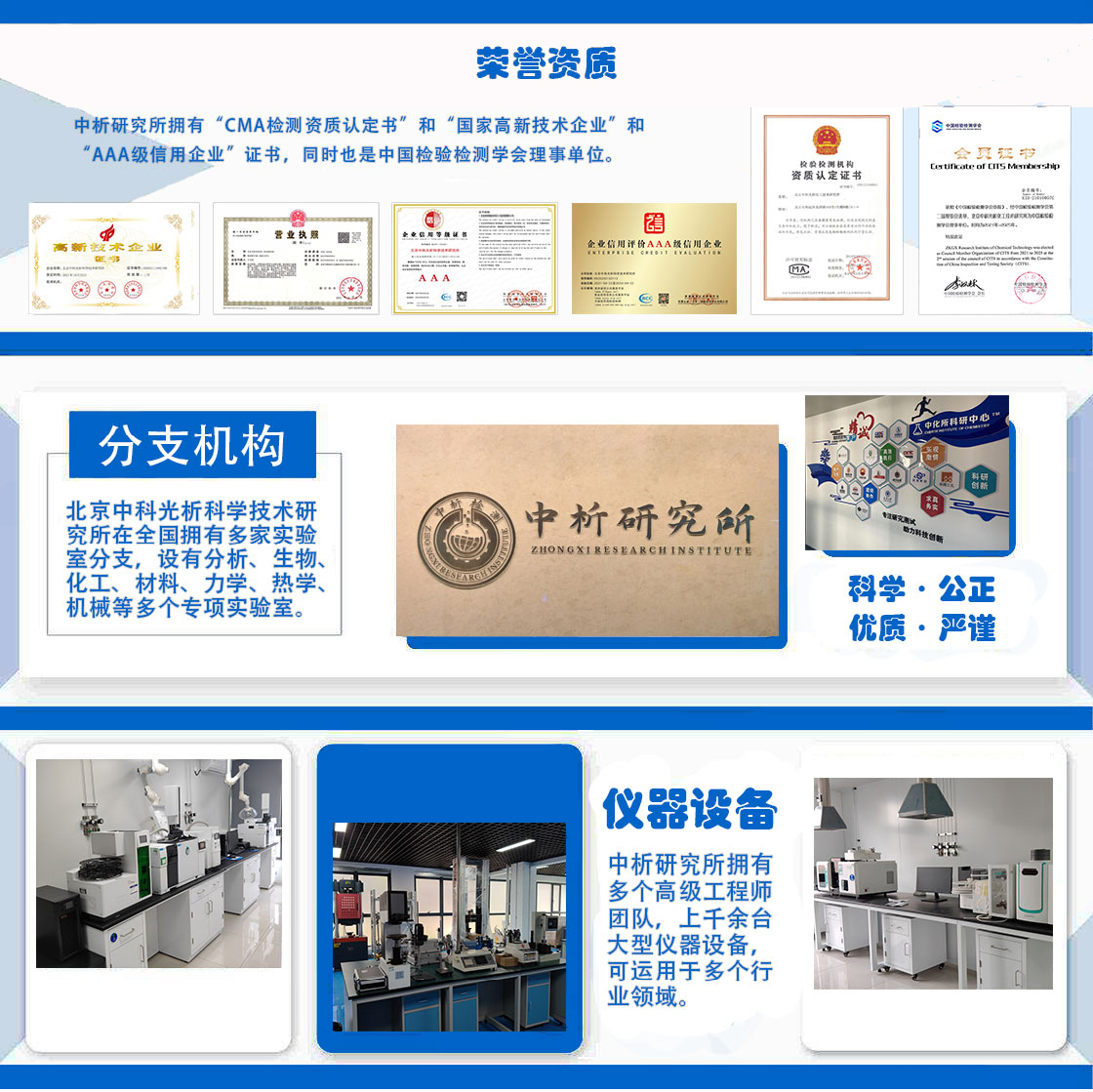
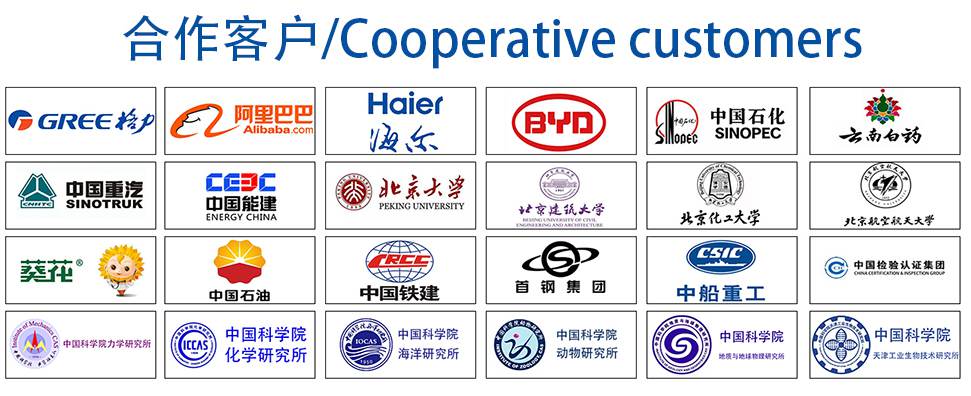