温度变化试验检测的核心价值与应用场景
温度变化试验检测是评估产品在极端温度环境下的可靠性和耐久性的重要手段,广泛应用于电子元器件、汽车零部件、航空航天设备、新能源产品等领域。通过模拟产品在高温、低温及快速温变条件下的工作状态,该检测可验证材料热膨胀系数匹配性、焊接点抗疲劳性、密封结构稳定性等关键性能。在工业4.0时代,随着产品复杂度提升和使用环境多样化,温度循环试验已成为质量管控体系中不可或缺的环节。根据国际标准IEC 60068-2-14和GB/T 2423.22,完整的温度变化试验需包含温度范围、温变速率、循环次数等核心参数的系统验证。
关键检测项目解析
1. 温度范围测试
检测设备需覆盖产品标称工作温度的120%范围,例如车载电子要求-40℃至+125℃的极限测试。通过高低温交变箱实现温度精准控制,验证材料玻璃化转变温度(Tg)是否达标。
2. 温变速率测试
依据MIL-STD-810G标准,常规试验采用5℃/min变化速率,严苛条件可达15℃/min。重点监测快速温变导致的PCB板微裂纹、BGA封装焊点失效等问题,使用红外热像仪记录温度场分布。
3. 循环次数验证
根据产品寿命周期设定循环次数,典型方案包含100次温度冲击循环。通过Weibull分布分析失效数据,计算加速老化系数,验证产品在10年使用周期内的可靠性。
4. 温度冲击试验
采用两箱法(高温箱与低温箱瞬时切换)或液氮制冷方式,实现-65℃至+150℃的剧烈温度冲击。重点关注陶瓷电容开裂、金属触点氧化等瞬时失效模式。
5. 恢复时间测试
在试验结束后保持常温环境24小时,检测产品电气性能恢复率。要求介电强度、绝缘电阻等关键指标波动不超过初始值的±5%。
检测设备与标准体系
现代温度试验箱配备PID智能控温系统,温度均匀度可达±0.5℃。检测过程需遵循ISO 16750-4(汽车电子)、JESD22-A104(半导体器件)等专项标准。实验室需取得 认可资质,检测报告应包含温变曲线图谱、失效模式分析及MTBF(平均无故障时间)计算等核心数据。
行业应用与质量提升
新能源汽车电池包通过200次-30℃至60℃循环测试后,电池容量衰减需控制在3%以内;航天器组件需通过50次-196℃至+120℃的液氮冲击测试。企业通过完善温度变化试验体系,可将产品早期失效率降低40%,显著提升市场竞争力。
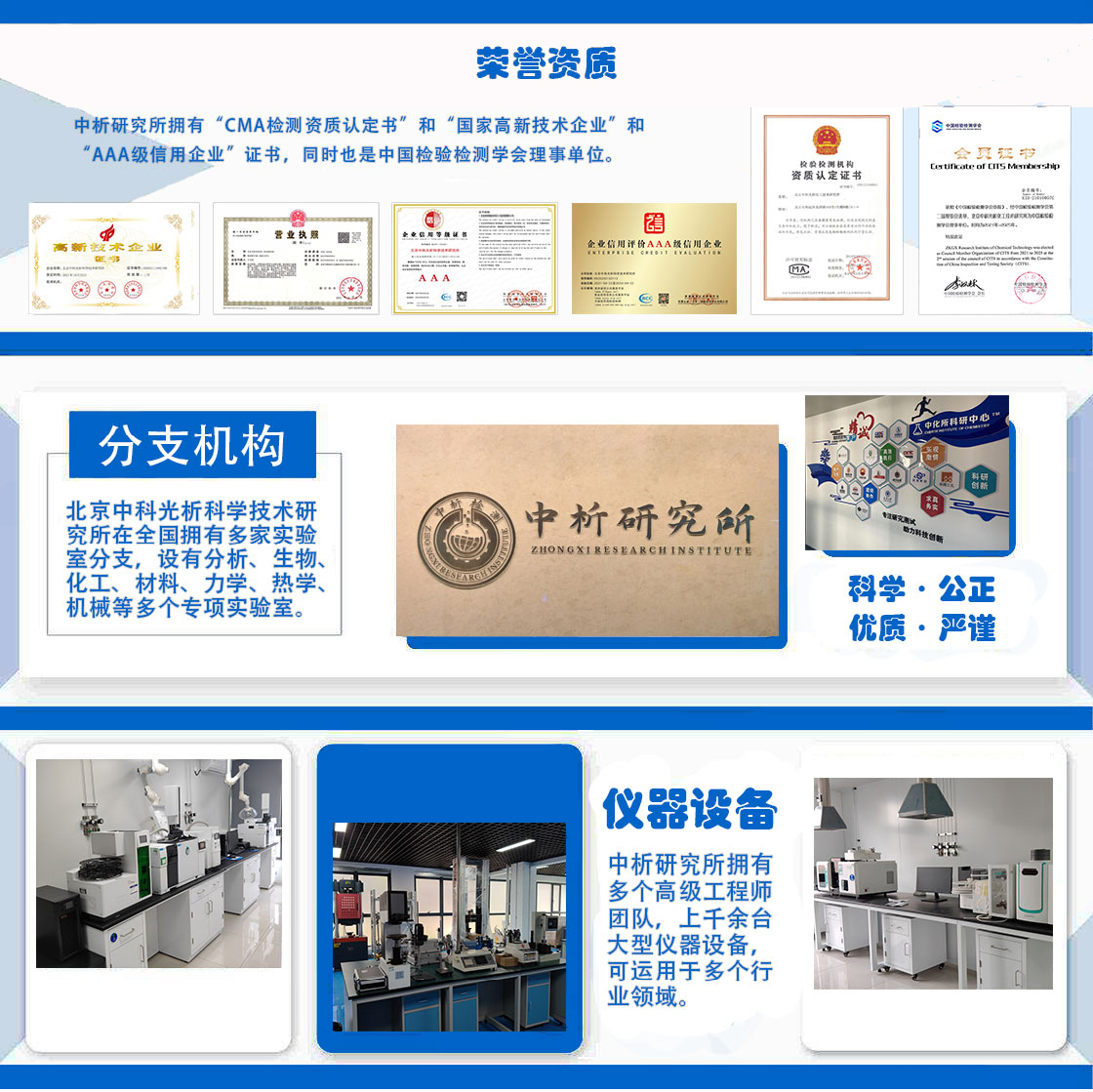
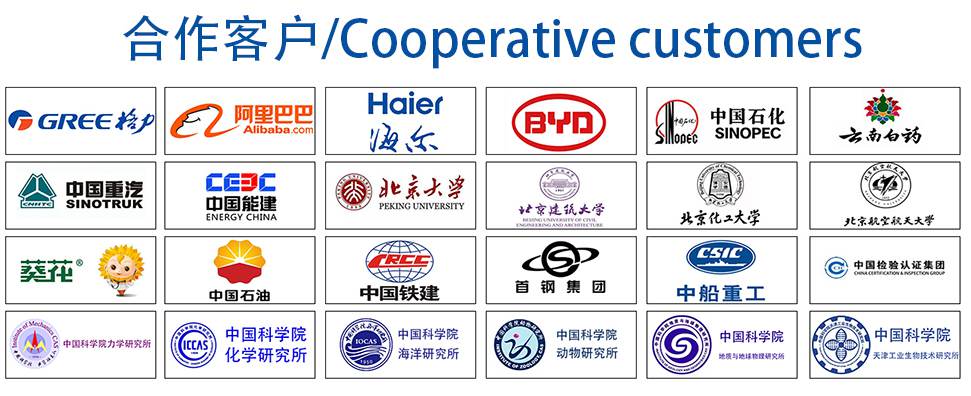