热真空试验检测:保障航天产品可靠性的关键环节
热真空试验是航天器、卫星组件及高端电子设备研发过程中不可或缺的环境模拟测试项目,主要用于验证产品在极端真空与温度交变条件下的性能稳定性。在太空环境中,设备不仅面临近乎绝对真空(10⁻³至10⁻⁶ Pa)的考验,还需承受剧烈温度波动(-180℃至+150℃),而热真空试验正是通过模拟这种复合环境,提前暴露产品潜在的设计缺陷与材料失效风险。据统计,航天器在轨故障中约30%与环境适应性不足直接相关,这使得热真空试验成为降低任务风险、延长设备寿命的核心技术手段。
核心检测项目解析
1. 热循环性能测试
通过程序化控温系统模拟航天器进出日照区时的温度骤变(典型循环次数为12-50次),检测材料热胀冷缩、焊点开裂、结构变形等问题。试验中需记录设备关键部位的温度梯度与响应时间,评估热控系统的有效性。
2. 真空漏率检测
采用氦质谱检漏仪对密封部件进行微泄漏检测,灵敏度可达10⁻⁹ Pa·m³/s。重点监测推进系统燃料舱、光学仪器腔体等关键部位,确保真空环境下气体逸出量符合设计要求(通常要求总漏率≤1×10⁻⁶ Pa·m³/s)。
3. 材料放气特性评估
在真空环境中持续加热样品(85℃/24h),利用四极质谱仪分析释放的挥发性有机物(TVOC)含量。此测试可防止材料脱气污染光学镜头或冷凝在低温表面,尤其对星敏感器、红外相机等精密设备至关重要。
4. 电子设备功能验证
在热真空舱内实时监测电路板、芯片组、连接器等在温度循环中的电性能参数(如阻抗、信号完整性、功耗等),验证真空环境对电子元器件散热特性、介质耐压强度的影响。
5. 机械结构稳定性测试
利用真空环境下的“冷焊”效应检测活动部件(如太阳翼铰链、天线展开机构)的运动可靠性,同时评估复合材料层压板、胶接界面在热应力作用下的力学性能衰减。
试验标准与设备要求
热真空试验需严格遵循ECSS-E-ST-10-03C、MIL-STD-1540E等国际标准,试验舱需具备精确控温(±1℃)、快速抽气(10⁻⁴ Pa级真空度)及多通道数据采集能力。典型设备包括液氮冷屏系统、分子泵组、红外加热阵列和高精度压力传感器网络。
结语
通过系统化的热真空试验检测,可提前发现产品90%以上的环境适应性缺陷,显著降低在轨故障率。随着商业航天与新卫星星座计划的快速发展,高效精准的热真空试验已成为航天供应链质量控制的刚性需求。
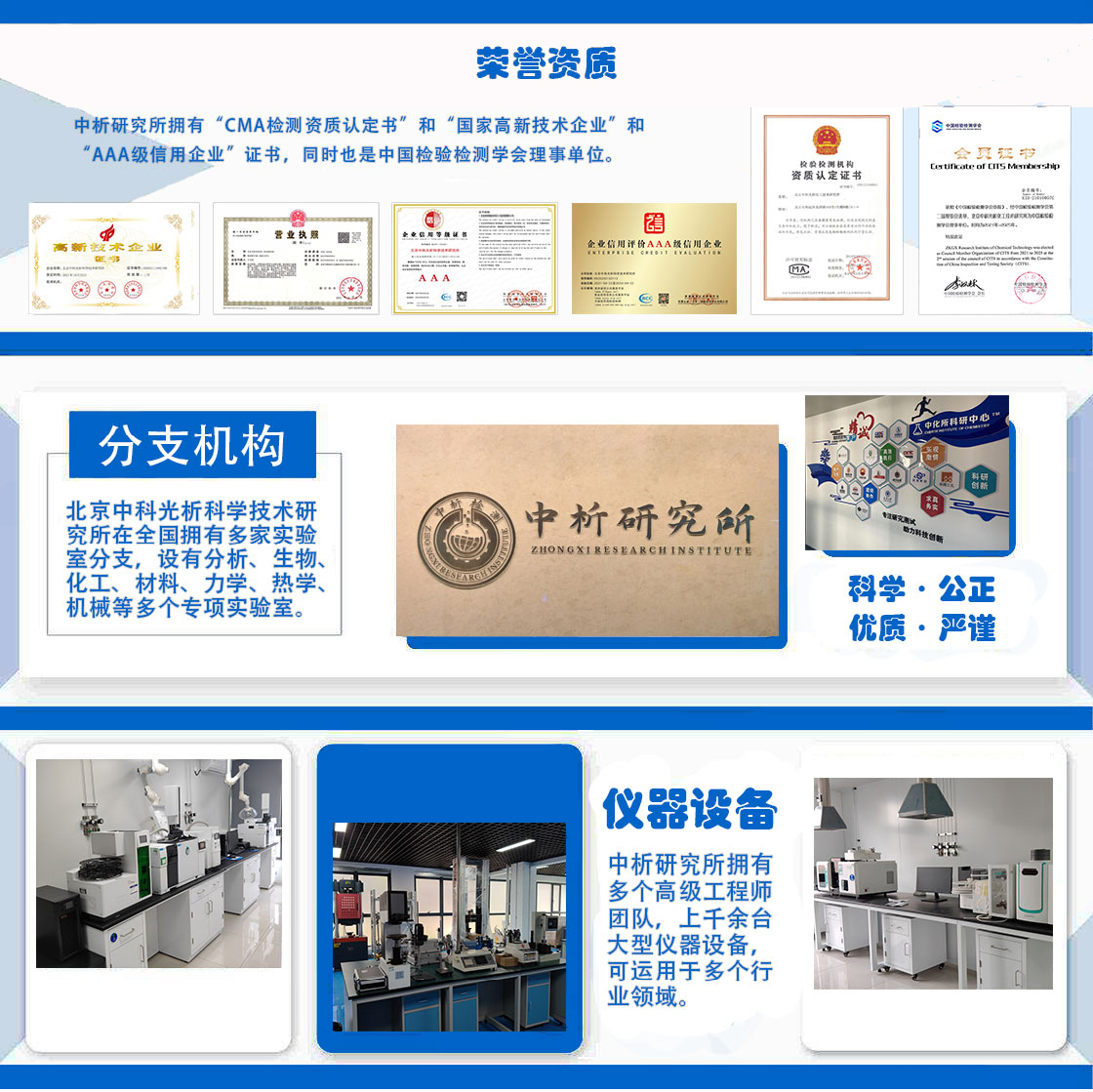
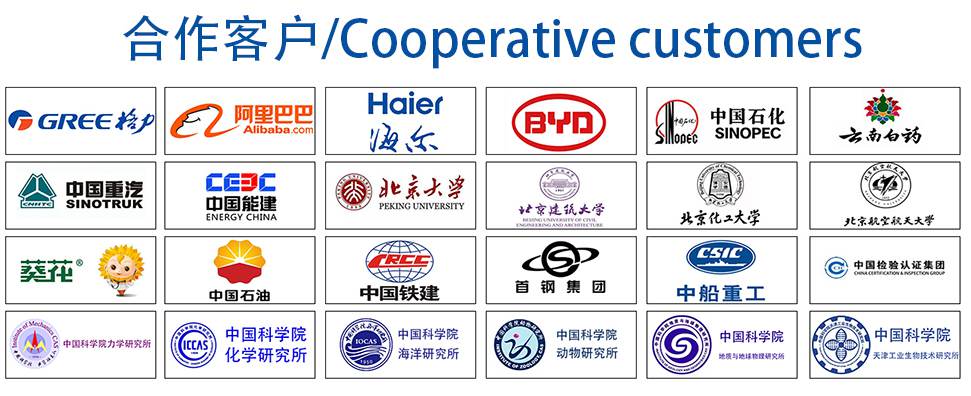