芯片剪切强度检测:确保电子元器件可靠性的关键指标
在半导体制造与封装工艺中,芯片剪切强度检测是评估芯片与基板、封装材料结合质量的核心测试项目。随着电子设备向微型化、高集成度方向发展,微米级芯片的机械稳定性直接决定了产品的抗冲击性、耐温变性和长期使用可靠性。这项检测通过模拟芯片在封装、焊接、运输及使用过程中可能承受的机械应力,量化分析其抗剪切能力,可有效预防因机械失效导致的电路断路、焊点脱落等质量事故。
检测原理与技术标准
剪切强度测试基于ASTM F1269、JESD22-B117等行业标准,采用精密力学测试系统对样品施加平行于芯片表面的剪切力。通过高速传感器记录最大载荷值,结合芯片尺寸计算单位面积的剪切强度。新型设备可实现从5N到5000N的宽量程测试,分辨率达0.01N,并配备红外热像仪同步监测测试过程中的温度变化。
关键检测项目分析
1. 焊点剪切强度检测
采用微探针测试系统对单个焊点进行点测,评估不同焊料合金(如SAC305、SnBi)的机械性能。通过对比老化前后的数据变化,可预测焊点的疲劳寿命。
2. 芯片边缘强度检测
针对齐全封装技术中的晶圆级芯片(WLCSP),使用45°倾斜剪切工具模拟封装应力。检测数据可指导切割工艺优化,防止崩边缺陷。
3. 基板粘接强度检测
对于Flip Chip、SIP等封装结构,采用阶梯式加载模式测试底填胶的粘接强度。配合声发射检测技术,可精确定位界面分层位置。
4. 芯片厚度与尺寸效应检测
建立芯片厚度(50-800μm)与剪切强度的数学模型,分析尺寸缩小对机械性能的影响规律,为3D封装设计提供数据支撑。
5. 温度循环剪切测试
在-55℃至150℃温度范围内进行动态测试,研究热机械应力对界面结合强度的影响,评估器件在极端环境下的可靠性。
常见失效模式与解决方案
检测过程中常见的失效模式包括界面断裂(占62%)、焊料撕裂(28%)和基材破坏(10%)。通过金相显微镜和SEM/EDS分析断口形貌,可追溯失效根源:当界面IMC层厚度超过5μm时,脆性断裂风险增加30%;而焊料空洞率超过15%将导致剪切强度下降40%。
齐全检测技术发展
最新研发的微机电系统(MEMS)原位测试装置可实现亚微米级位移控制,结合数字图像相关(DIC)技术,可实时捕捉芯片变形过程。部分实验室已采用AI算法建立强度预测模型,将检测周期缩短70%,异常检出率提升至99.6%。
检测流程标准化
典型检测流程包含五大环节:样品预处理(烘烤除湿)、基准面校准(平面度≤0.005mm)、参数设置(加载速率0.1-10mm/min)、数据采集(采样率≥1kHz)、结果分析(Weibull分布拟合)。每个环节均需执行ISO/IEC 17025标准的质量控制程序。
行业应用与质量控制
在汽车电子领域,AEC-Q100标准要求芯片需通过200次温度循环后的剪切强度测试;工业级器件则需满足IPC-9701规定的50g机械冲击后强度保持率≥80%。通过建立SPC控制图,企业可将制程能力指数(Cpk)稳定在1.67以上,确保产品批次一致性。
结语
芯片剪切强度检测作为电子元器件质量验证的关键环节,其检测精度直接影响产品可靠性和企业信誉。随着新材料、新封装技术的不断涌现,检测方法正在向多物理场耦合测试、智能化数据分析方向演进,为半导体行业高质量发展提供重要技术支撑。
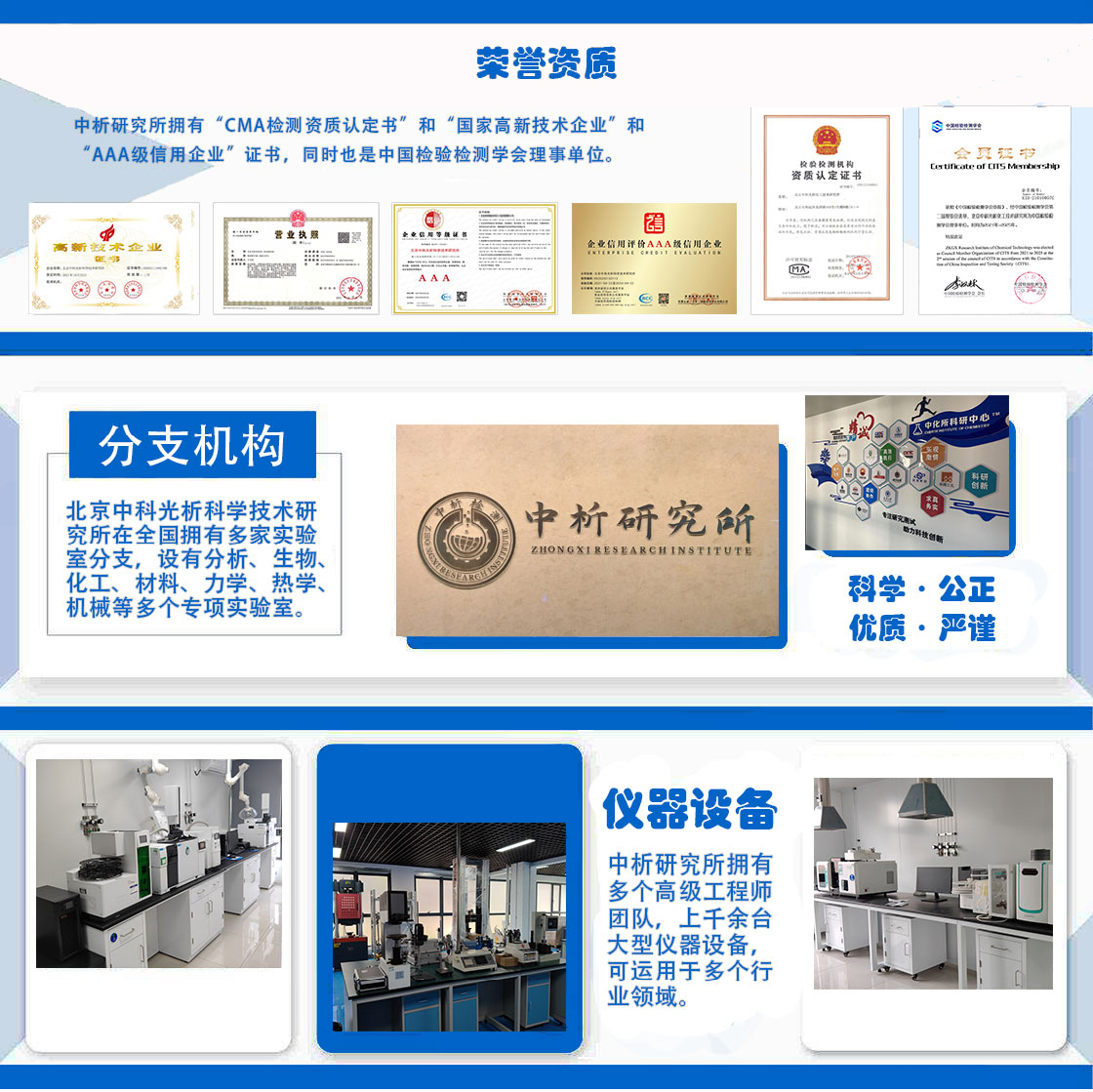
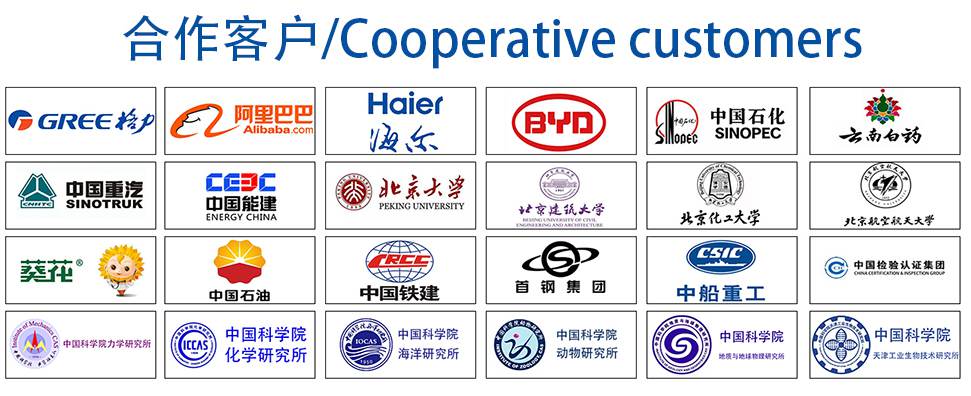